Types of Bonds in Grinding Wheels
Grinding wheels are indispensable tools in various industrial applications, from metalwork to glass cutting. Their performance largely depends on the types of bonds that hold the abrasive grains together. Understanding these bond types is crucial for selecting the right grinding wheel for specific tasks. In this article, we will explore the various types of bonds used in grinding wheels, namely vitrified, resin, metal, and rubber bonds, and discuss their unique characteristics and applications.
Vitrified Bonds
Vitrified bonds are one of the most common types used in grinding wheels. They are composed of clay, feldspar, and other materials, which are subjected to high temperatures during the manufacturing process. This results in a glass-like structure that provides excellent stability, strength, and thermal resistance. Vitrified bonding is particularly suitable for precision grinding applications, as it allows for high-accuracy results and a long tool life.
These wheels exhibit good wear resistance and can withstand high grinding pressures and speeds. Furthermore, they do not absorb moisture, which aids in maintaining wheel integrity over time. Vitrified bond wheels are often found in applications involving grinding metals, ceramics, and other hard materials.
Resin Bonds
Resin bonds are another popular choice in grinding wheel manufacturing. Made from synthetic resins and other organic materials, these bonds offer a unique combination of flexibility and strength. Resin bond wheels are particularly effective for producing a smooth surface finish, making them ideal for applications such as tool sharpening and woodwork.
One of the most significant advantages of resin bonds is their ability to adapt to various abrasive materials, enabling manufacturers to create wheels tailored for specific tasks. Additionally, resin bond wheels can withstand high temperatures, but they may not perform as well as vitrified bonds in extremely high-speed applications. Because of their versatility, resin bond wheels are commonly used in the automotive, aerospace, and woodworking industries.
types of bond in grinding wheel
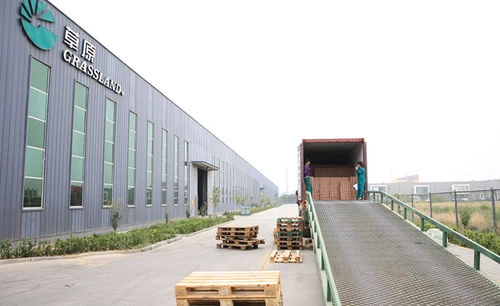
Metal Bonds
Metal bonds consist of a mixture of metal powders, which are compressed and sintered during manufacturing. These wheels are characterized by their durability and high wear resistance, making them particularly well-suited for heavy-duty grinding applications. Metal bond wheels are often used in the production of diamond grinding tools, which are effective in machining hard materials like carbide and glass.
One of the key advantages of metal bonds is their ability to retain the abrasive material for a longer period, resulting in a longer lifespan for the grinding wheel. However, they are generally harder and less forgiving than other bond types, which can lead to a rougher surface finish. Metal bond wheels are frequently used in industries such as stone and concrete processing, as well as in specialized grinding operations.
Rubber Bonds
Rubber bonds are less common but serve specific applications where flexibility and shock absorption are essential. These bonds consist of rubber polymers that bind the abrasive grains together, resulting in a wheel that can conform to the workpiece's shape. Rubber bond wheels are widely used in specialized grinding operations, such as the manufacturing of precision parts and tools where a finer finish is required.
The key advantage of rubber bonds is their ability to absorb vibrations and reduce chatter during the grinding process. This feature enhances the overall performance and quality of the finished product. However, rubber bond wheels may have a shorter lifespan compared to vitrified and metal bonds, making them suitable primarily for specific applications where flexibility is prioritized.
Conclusion
In summary, the choice of bond in grinding wheels significantly influences their performance and suitability for various applications. Vitrified bonds provide strength and precision, resin bonds offer versatility and smooth finishes, metal bonds deliver durability for heavy-duty tasks, and rubber bonds excel in flexibility and vibration reduction. Understanding these bond types allows manufacturers and operators to select the right grinding wheel for their specific needs, thus enhancing productivity and ensuring high-quality outcomes. When selecting a grinding wheel, it is crucial to consider the intended application, material to be processed, and the expected quality of the finish. With the right selection, grinding wheels can achieve optimal performance and efficiency, ultimately benefiting the end product and the manufacturing process.
Post time:Dec - 20 - 2024