Types of Bond in Grinding Wheels
Grinding wheels are essential tools in various industrial applications, particularly in metalworking and manufacturing. The effectiveness and performance of a grinding wheel largely depend on its bond type, which dictates the wheel's structure, durability, and the quality of the grinding process. Understanding the different types of bonds in grinding wheels can significantly enhance the selection and application of these tools in specific tasks.
1. Vitrified Bond
Vitrified bonds are among the most popular types of bonds used in grinding wheels, thanks to their exceptional strength and thermal stability. These wheels are made from a mixture of clay, feldspar, and other compounds that are heated at high temperatures to create a glazed, glassy material. Vitrified bond wheels are ideal for producing fine finishes and are typically used for precision grinding applications. They can resist wear and maintain their shape well under pressure. Additionally, due to their porous nature, these bonds allow for the effective removal of chips and coolant, which helps in maintaining a cooler grinding environment.
2. Resinoid Bond
Resinoid bonds are made from synthetic resins and provide a balance between resilience and strength. These bonds are known for their ability to absorb shock and vibrations, making them suitable for precision grinding applications. Resinoid bond wheels tend to provide a smooth finish and are particularly effective in grinding hard materials. They are also commonly used in applications where a cooler cutting action is essential since they generate less heat compared to other bond types. Moreover, resinoid bonds are less brittle than vitrified bonds, offering a longer lifespan in many grinding tasks.
3. Metal Bond
types of bond in grinding wheel
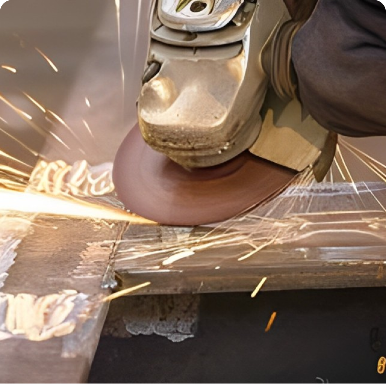
Metal-bonded grinding wheels are made by sintering metal powders together to form a durable bond. These wheels are known for their mechanical strength and ability to maintain their shape under heavy loads. Because of their robust nature, metal bond wheels are highly effective for grinding hard materials, such as ceramics, carbide, and glass. They excel in applications where high durability is required, such as in heavy-duty grinding operations. However, they may not produce as fine a finish as vitrified or resinoid bonds, making them less suitable for tasks that demand precision.
4. Electroplated Bond
Electroplated bonds involve the deposition of a layer of abrasive grit onto a metallic substrate using an electroplating process. This type of bond is known for its high precision and ability to produce fine finishes. Electroplated wheels provide fast cutting action and are often used in specialized applications, such as grinding intricate shapes or profiles. They are notable for their exceptional adhesion and can be engineered to have very specific properties, depending on the type of material being worked on.
5. Ceramic Bond
Ceramic bonds are another advanced bond type primarily used in high-performance grinding applications. These wheels are constructed from ceramic materials that provide excellent hardness and wear resistance. They are particularly effective at operating under high temperatures, making them suitable for demanding tasks. Ceramic bonded wheels offer a unique combination of durability and cutting efficiency, and they are often used in industries such as aerospace and automotive manufacturing.
Conclusion
The choice of bond in a grinding wheel plays a crucial role in determining its performance and suitability for specific tasks. Vitrified, resinoid, metal, electroplated, and ceramic bonds each offer unique advantages tailored to different grinding applications. By understanding the characteristics and benefits of each bond type, users can make informed decisions that enhance productivity, precision, and the overall quality of their grinding operations. Selecting the right grinding wheel bond is not just a matter of preference but a critical aspect of achieving optimal results in machining and manufacturing processes.
Post time:Nov - 21 - 2024