Types of Grinding A Comprehensive Overview
Grinding is a crucial process in manufacturing and material processing, known for its ability to achieve precise dimensions and fine surface finishes. It involves the use of an abrasive tool to remove material from a workpiece, allowing for a variety of applications across different industries. In this article, we will explore the several types of grinding processes, their techniques, and their specific uses.
1. Surface Grinding
Surface grinding is one of the most common types of grinding. It involves the use of a rotating abrasive wheel to smooth the flat surfaces of a workpiece. This method ensures high precision in the finished product, making it suitable for applications where dimensional accuracy is critical. Surface grinding is widely used in tool manufacturing, production of flat components, and refining parts that require a smooth surface finish.
Cylindrical grinding is used for grinding the outer surface of cylindrical objects. The workpiece is placed between centers, or it is mounted on a chuck, while the grinding wheel rotates around it. This process can be categorized into two types external cylindrical grinding and internal cylindrical grinding. External cylindrical grinding focuses on the outer surface, while internal cylindrical grinding targets the inside diameter of a holes or tubes. Because of its precision, this method is commonly used in manufacturing shafts, sleeves, and other cylindrical parts.
3. Centerless Grinding
Centerless grinding is unique because it does not require the use of a machine setup that includes a fixture to hold the workpiece. Instead, the workpiece is supported by a roller, and the grinding wheel removes material while the piece continuously rotates through the machine. This method is ideal for high-volume production, as it allows for efficient processing of components like bars and tubes without the need for additional clamping mechanisms. It is commonly used in manufacturing applications requiring speed and precision.
types of grinding
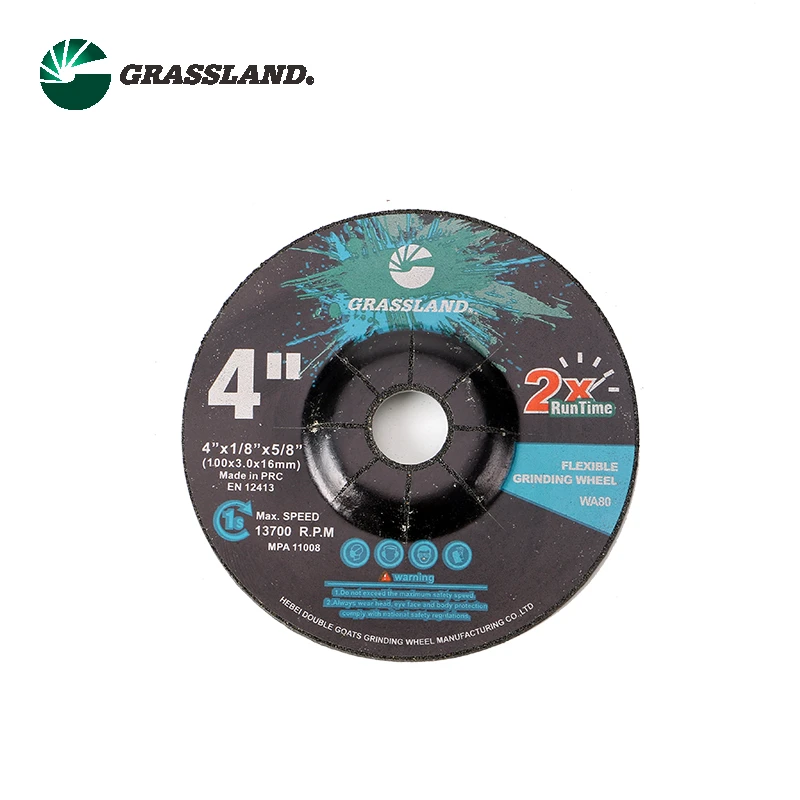
4. Tool and Cutter Grinding
Tool and cutter grinding is a specialized form of grinding aimed at sharpening and shaping cutting tools. This process plays a vital role in maintaining the efficiency of tools such as drill bits, end mills, and other cutting implements. Using a tool and cutter grinder, manufacturers can precisely sharpen tools to restore their cutting effectiveness, significantly reducing production costs and downtime associated with tool wear.
5. Wet and Dry Grinding
Grinding can also be categorized as wet or dry, based on the use of coolant during the process. Wet grinding involves the use of water or other coolants to eliminate heat generated from friction while enhancing the grinding performance. This method is ideal for working with delicate materials that may break down under excessive heat. Conversely, dry grinding does not employ coolants, making it suitable for operations where contamination must be avoided or where materials would react adversely to moisture.
6. Precision Grinding
Precision grinding is an advanced form of grinding that aims at achieving very tight tolerances and high surface finishes. It often combines several grinding methods and utilizes specialized equipment tailored to specific requirements. This method is critical in industries such as aerospace, automotive, and electronics, where parts must meet stringent specifications to ensure functionality and safety.
Conclusion
In summary, grinding is an essential operation in various manufacturing processes that demand precision and efficiency. Each type of grinding—be it surface, cylindrical, centerless, tool and cutter, or precision grinding—has its distinct techniques, advantages, and applications. Understanding these different methods allows businesses to choose the right grinding process for their specific needs, ultimately contributing to the quality and efficiency of their production. Whether it’s sharpening tools, smoothing surfaces, or achieving tight tolerances, grinding remains a fundamental aspect of modern manufacturing.
Post time:Dec - 14 - 2024