Types of Grinding A Comprehensive Overview
Grinding is an essential process in various industries, from manufacturing to food production. It's used for producing fine materials, shaping components, and achieving desired surface finishes. While it may seem straightforward, grinding encompasses several different methods and techniques, each suited for specific applications. In this article, we will explore the various types of grinding processes, their uses, and the equipment involved.
1. Surface Grinding
Surface grinding is a widely used machining process where a flat surface is produced using a rotating grinding wheel. This technique is particularly effective for achieving precise dimensions and high-quality finishes. The grinding wheel is typically made of abrasive materials, and the process involves moving the workpiece across the wheel or vice versa. Surface grinding is common in tool and die making, as well as in the manufacturing of precision components.
2. Cylindrical Grinding
Cylindrical grinding is employed to produce cylindrical workpieces. In this process, both the workpiece and the grinding wheel rotate; the workpiece is held between two centers or mounted on a chuck while the grinding wheel moves along its axis. There are two main types of cylindrical grinding external and internal. External cylindrical grinding focuses on the outer diameter of the workpiece, while internal cylindrical grinding deals with the inner surface. This technique is crucial in industries manufacturing shafts, pins, and various engine components.
3. Centerless Grinding
Centerless grinding differs from traditional cylindrical grinding in that it does not require the workpiece to be mounted between centers. Instead, it is supported by a work rest and held in place by a regulating wheel. This method can achieve high production rates and is often used for grinding long, thin workpieces. It is especially beneficial for processing bars and tubes, making it suitable for manufacturing applications where precision and efficiency are paramount.
4
. Bench Grindingtypes of grinding
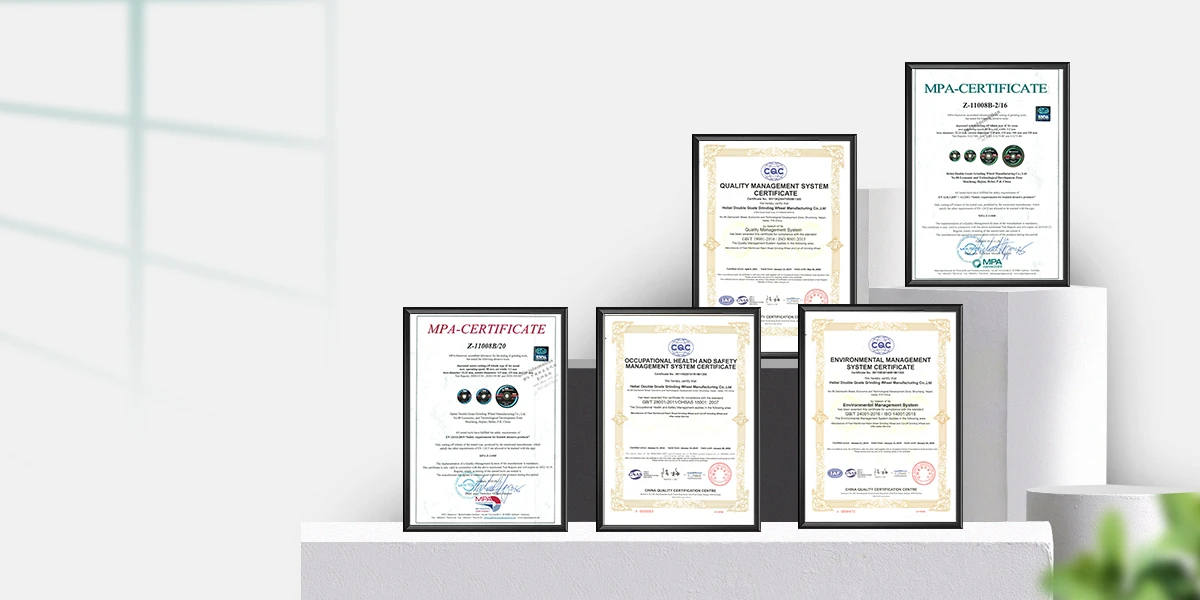
Bench grinding is a common practice in workshops and small-scale manufacturing environments. It involves mounting a grinding wheel on a bench or pedestal, allowing operators to grind small workpieces using a handheld tool or by manually bringing the workpiece to the wheel. Bench grinders are versatile and can be used for sharpening tools, deburring, and removing material from metal surfaces. Due to their ease of use, they are favored by hobbyists and artisans alike.
5. Gear Grinding
Gear grinding is a specific type of grinding used to create gears with high accuracy. This process often involves grinding the tooth surfaces of gears after they have been cut and heat-treated. Gear grinding improves the finish and ensures the teeth are properly shaped for meshing with other gears. This technique is crucial in the automotive and aerospace industries, where precision is vital for performance and reliability.
6. Tool and Cutter Grinding
Tool and cutter grinding is a specialized form of grinding that focuses on sharpening and shaping cutting tools. This process enables the reconditioning of tools such as drills, end mills, and lathe tools, extending their lifespan and maintaining effectiveness. Tool grinders typically use a variety of attachments and fixtures to hold the tools securely while they undergo the grinding process.
7. Wet and Dry Grinding
Grinding can be done using either wet or dry methods. Wet grinding involves using a coolant or lubricant during the grinding process, which helps to reduce heat and wear on the grinding wheel and the workpiece. This method is advantageous for materials that can be easily damaged by heat, such as certain metals and ceramics. In contrast, dry grinding is performed without coolant, often used for applications requiring higher material removal rates or for non-metallic materials.
Conclusion
The diversity of grinding techniques reflects the varying demands of different industries. From surface and cylindrical grinding to specialized processes like gear grinding, each method serves a unique purpose, contributing to the overall efficiency and precision of manufacturing processes. Understanding the different types of grinding allows businesses to select the most appropriate methods for their specific applications, ultimately leading to better quality products and optimized production workflows. Whether it’s for creating finely machined parts or sharpening tools, grinding remains a cornerstone of modern manufacturing.
Post time:Dec - 17 - 2024