Types of Grinding Wheel Materials
Grinding wheels are an essential component in various machining processes, utilized for grinding, cutting, and shaping metal and other materials. The effectiveness and efficiency of these wheels largely depend on the type of material used in their construction. Several materials are employed in the making of grinding wheels, each offering unique properties that cater to different applications. This article discusses the primary types of grinding wheel materials and their characteristics.
Aluminum oxide is the most commonly used material in grinding wheels. It is known for its durability and is suitable for grinding ferrous metals. This versatile material comes in several forms, including white aluminum oxide for high-quality applications and brown aluminum oxide, which is more economical and widely used for general-purpose grinding. Aluminum oxide wheels are effective in achieving a good surface finish and are ideal for cutting applications.
2. Silicon Carbide
Silicon carbide grinding wheels are made from silicon and carbon. They are typically used for grinding non-ferrous metals such as copper, brass, and aluminum. Silicon carbide is harder than aluminum oxide, providing excellent performance in grinding applications that require a sharper cutting edge. These wheels are also effective for materials like glass and stone. However, due to their brittleness, they must be handled with care to prevent chipping or breaking.
3. Cubic Boron Nitride (CBN)
types of grinding wheel material
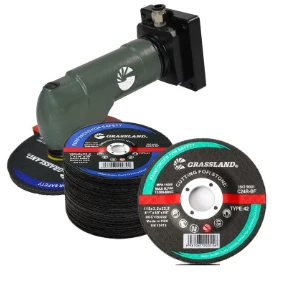
Cubic boron nitride is an advanced abrasive material and the second hardest material after diamond. CBN grinding wheels are mainly used for high-speed grinding of hard steels and superalloys, making them suitable for industries that require precision machining. They offer excellent thermal stability and resistance to wear, resulting in longer life compared to conventional abrasives. Due to their properties, CBN wheels are often employed in the automotive and aerospace sectors for grinding tasks that demand high precision and minimal thermal distortion.
4. Diamond
Diamond grinding wheels are the top-performing abrasive tools available and are utilized for grinding the hardest materials, including ceramics, glass, and composite materials. They provide superior cutting performance and longevity compared to other grinding wheel materials. Diamond wheels are available in various shapes and sizes, suitable for different applications such as surface grinding, profile grinding, and precision grinding. While they are more expensive, the benefits of reduced tool wear and increased efficiency make them a worthwhile investment for specialized applications.
5. Resin Bonded Wheels
Resin bonded grinding wheels incorporate synthetic resins as a bonding agent, providing excellent flexibility and stability. These wheels can feature different abrasives, such as aluminum oxide or silicon carbide, allowing them to be tailored for specific applications. They are particularly effective for grinding applications involving intricate shapes and fine finishes due to their ability to conform to workpiece contours. The resin bond offers good shock resistance and can withstand higher operating speeds, making them suitable for a variety of industries.
Conclusion
Selecting the right grinding wheel material is crucial for achieving optimal results in various machining operations. Understanding the characteristics and applications of different materials, such as aluminum oxide, silicon carbide, cubic boron nitride, diamond, and resin-bonded wheels, allows manufacturers to choose the appropriate tools for their specific needs. As technology and research in abrasive materials continue to advance, the development of new grinding wheel formulations is likely to enhance performance and efficiency across numerous industries. Whether for industrial applications or DIY projects, the right grinding wheel can significantly impact productivity and machining quality.
Post time:Dec - 05 - 2024