Types of Grinding Wheels and Their Uses
Grinding wheels are essential tools in various industries, primarily used for grinding, cutting, and polishing materials. These wheels are composed of abrasive particles bonded together in a circular shape, rotating at high speeds to aid in material removal. The type of grinding wheel selected can significantly influence the efficiency and quality of the grinding process. Understanding the different types of grinding wheels and their uses is crucial for achieving optimal results in metalworking, woodworking, and other applications.
1. Alumina Grinding Wheels
Alumina grinding wheels, made primarily from aluminum oxide, are among the most common types used for various applications. They are ideal for grinding high-strength materials, including steel, stainless steel, and cast iron. These wheels provide a high level of durability and wear resistance, making them suitable for heavy-duty grinding tasks. Because of their versatility, alumina wheels can be used in both bench grinders and portable grinders.
2. Silicon Carbide Grinding Wheels
Silicon carbide grinding wheels are composed of silicon carbide abrasives and are ideal for grinding softer materials such as aluminum, copper, and brass. They are known for their sharp edges and ability to cut quickly, making them a great choice for polishing and grinding non-ferrous metals. These wheels are also effective in cleaning and deburring, as they create a finer finish than other types of grinding wheels.
3. Diamond Grinding Wheels
Diamond grinding wheels are considered the most efficient grinding tools available, primarily used for grinding hard materials such as ceramics, glass, and stone. The diamond abrasives embedded in the wheel provide superior cutting capabilities and long service life. Although they can be more expensive than other grinding wheels, their efficiency often justifies the cost, especially for industrial applications. Diamond wheels are commonly used in construction, manufacturing, and even in labs for precise cutting tasks.
4. Cubic Boron Nitride (CBN) Grinding Wheels
types of grinding wheels and their uses
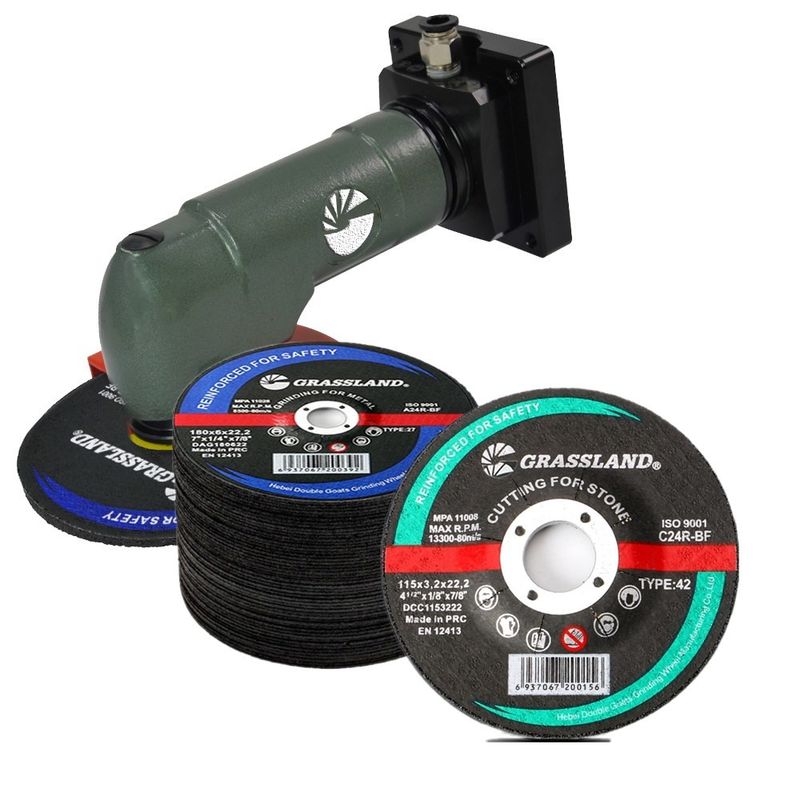
Cubic boron nitride, or CBN, is the second hardest material known after diamond. CBN grinding wheels are specifically designed for grinding ferrous materials, including hardened steel and tool steels. They provide excellent heat resistance and can achieve high precision and surface finishes. These wheels are often used in industries that require extreme accuracy and quality, such as aerospace and automotive manufacturing.
5. Resin Bond Grinding Wheels
Resin bond grinding wheels are made with a bonding agent that can withstand high speeds and temperatures. These wheels are versatile and can be used for a range of operations, including grinding, cutting, and shaping. Resin bond wheels provide a good balance between speed and finish quality and are often used in applications where both are critical. They are excellent for achieving fine finishes while maintaining durable performance.
6. Vitrified Bond Grinding Wheels
Vitrified bond grinding wheels are created using a mixture of abrasive particles and glass-like bonding materials. They provide superior strength, thermal stability, and wear resistance, making them suitable for precision applications. Vitrified wheels are commonly used in creations that require a sharp cutting edge, such as tool and cutter grinding. They can be used on a variety of machines, including surface grinders, cylindrical grinders, and tool grinders.
7. Specialty Grinding Wheels
In addition to the standard types of grinding wheels, there are also specialty wheels designed for specific applications. These include wheels for grinding specific shapes, such as cup wheels for internal grinding, and flap wheels, which consist of multiple layers of abrasive flaps that can provide a more flexible and finer finish. Specialty wheels may be tailored for specific industries or tasks, ensuring optimal performance in unique situations.
Conclusion
Selecting the right grinding wheel is critical for achieving efficiency and quality in machining processes. With various options available—including alumina, silicon carbide, diamond, CBN, resin bond, and vitrified bond wheels—professionals must consider the material being worked on, the desired finish, and the specific requirements of their projects. By understanding the unique characteristics and applications of each type of grinding wheel, operators can enhance their productivity and ensure the best results in their grinding tasks.
Post time:Nov - 25 - 2024