Understanding Types of Grinding Wheels
Grinding wheels are essential tools in various machining operations, widely used for shaping, finishing, and modifying materials. They consist of abrasive particles bonded together to create a hardened wheel. The effectiveness of grinding wheels depends on their composition, structure, and type. In this article, we will explore the different types of grinding wheels, highlighting their unique characteristics and applications.
1. Aluminum Oxide Wheels
Aluminum oxide grinding wheels are among the most common types. They are made from a high-purity aluminum oxide abrasive, known for its versatility and durability. These wheels are ideal for grinding steel, iron, and other ferrous materials. Aluminum oxide wheels are available in various grades, ranging from coarse to fine, allowing operators to select the appropriate wheel for their specific grinding task. Their cost-effectiveness makes them a popular choice in both industrial and domestic settings.
2. Silicon Carbide Wheels
Silicon carbide wheels are made from silicon carbide abrasive, which is particularly effective for hard materials such as ceramics and glass. These wheels are usually dark green or black in color and perform well in applications involving non-ferrous metals. Silicon carbide is also used for grinding softer materials, making these wheels suitable for applications where efficient cutting action is required. Manufacturers often recommend silicon carbide wheels for finishing machined parts.
3. Cubic Boron Nitride (CBN) Wheels
Cubic Boron Nitride wheels are made from one of the hardest materials known, making them exceptionally suitable for grinding hardened steels and superalloys. CBN wheels maintain their shape and cutting ability longer than traditional wheels due to their hardness and thermal stability. This durability reduces the need for frequent wheel changes, ultimately increasing productivity. However, they tend to be more expensive than aluminum oxide and silicon carbide wheels, which limits their applications to high-precision industries such as aerospace and automotive manufacturing.
types of grinding wheels ppt
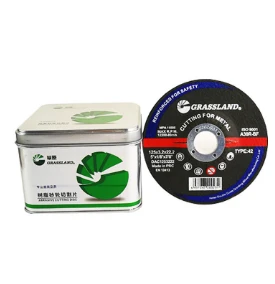
4. Diamond Wheels
Diamond wheels are the hardest grinding wheels available, designed for grinding and finishing hard materials like concrete, ceramics, and stone. They are made with diamond particles bonded to the wheel using a metal or resin matrix. Diamond wheels offer superior cutting speeds and a long lifespan, making them ideal for heavy-duty grinding operations. These wheels find extensive use in the construction industry and in manufacturing processes where precision and efficiency are critical.
5. Fiber Resin Wheels
Fiber resin wheels are lightweight and flexible, making them suitable for various grinding and cutting applications. They are typically used for light grinding, blending, and polishing tasks. The composition of fiber resin wheels allows them to adjust to the contours of the workpiece while providing consistent performance. They are particularly popular for use on stationary grinders and handheld tools.
6. Mounted Points
Mounted points are small grinding wheels bonded to a shaft, making them ideal for precision grinding on areas like small holes or intricate shapes. They are versatile and available in various shapes, sizes, and abrasive materials, allowing for detailed work in both metal and non-metal applications.
Conclusion
The selection of the appropriate grinding wheel type is crucial for achieving desired results in any machining or finishing operation. Understanding the unique properties and applications of different grinding wheels can help operators choose the right wheel for their specific needs. Whether it's aluminum oxide for general use, silicon carbide for non-ferrous materials, CBN and diamond wheels for high-precision tasks, or fiber resin and mounted points for versatile applications, each type of grinding wheel plays a significant role in modern industrial processes. Careful consideration of the material to be worked on and the intended application will ensure optimal performance and efficiency in grinding operations.
Post time:Dec - 16 - 2024