Using a Flap Disc A Comprehensive Guide
Flap discs are essential tools in the world of metalworking, woodworking, and fabrication. They offer a versatile solution for various tasks, including grinding, deburring, blending, and finishing surfaces. Understanding how to effectively use flap discs can significantly enhance your productivity and improve the quality of your work. In this article, we will explore what flap discs are, their applications, and tips for using them effectively.
What is a Flap Disc?
A flap disc is a type of abrasive tool composed of multiple overlapping layers or flaps of abrasive material mounted on a backing plate. These flaps are typically made from aluminum oxide or zirconia, which provide longevity and efficiency when performing grinding tasks. The design allows for the dispersal of heat and debris, making flap discs less prone to clogging compared to traditional grinding wheels.
Flap discs are available in various diameters and grit sizes, allowing users to select the right disc for their specific tasks. The grit size indicates the coarseness of the abrasive material, with lower numbers representing coarser grits that remove material quickly, while higher numbers represent finer grits suitable for finishing work.
Applications of Flap Discs
1. Grinding Flap discs are primarily used for grinding metal surfaces. They can effectively remove material from weld seams, burrs, and surface imperfections.
2. Deburring When working with metal pieces, burrs often protrude from the surface and can be sharp. Flap discs can smooth these edges, making the final product safer and more aesthetically pleasing.
3. Blending In many cases, different types of finishes need to be blended together seamlessly. Flap discs are excellent for achieving this, providing a uniform finish across various materials.
4. Finishing For intricate work and final touch-ups, flap discs can create a polished surface. This is particularly useful in artistic metalworking or when preparing surfaces for painting or coating.
Choosing the Right Flap Disc
Selecting the appropriate flap disc for your project can significantly impact your results. Consider the following factors
using a flap disc
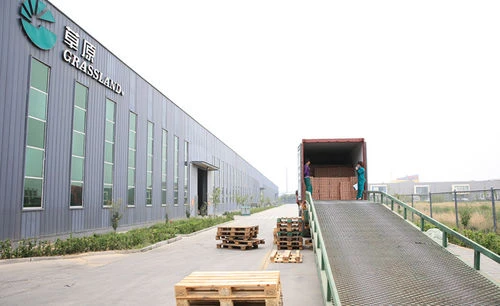
- Material The type of material you’ll be working on (steel, aluminum, etc.) will dictate the choice of abrasive. Zirconia is best for heavy-duty applications, while aluminum oxide works well for lighter tasks.
- Grit Size Assess the extent of material removal needed. For aggressive grinding, a lower grit (24-60) is suitable. For finishing and polishing, opt for a higher grit (80-120).
- Disc Shape Flap discs come in two shapes flat and conical. Flat discs are ideal for flat surfaces, while conical discs are better for working on edges and contours.
Tips for Effective Use
1. Safety First Always wear appropriate personal protective equipment, such as safety goggles and gloves. Ensure that the working area is well-ventilated to mitigate dust exposure.
2. Proper Speed Setting Use a tool with adjustable speed settings. High RPMs (revolutions per minute) can enhance the efficiency of flap discs but can also increase the risk of damage to the material if not controlled.
3. Angle of Application Maintain a consistent angle of approximately 15-30 degrees to ensure even wear on the disc and to achieve a smooth finish.
4. Avoid Overheating Overheating can cause the flap disc to wear prematurely and may damage the workpiece. Use steady, even pressure rather than pressing too hard.
5. Regular Replacement Keep an eye on the condition of your flap disc. Once the flaps start to wear down or the performance diminishes, it’s time for a replacement to maintain efficiency.
Conclusion
Flap discs are a versatile and invaluable tool for anyone involved in metal or woodwork. By selecting the right type, understanding their applications, and using them with care, you can achieve excellent results in your projects. Whether you're a professional tradesperson or a DIY enthusiast, incorporating flap discs into your toolkit will undoubtedly elevate your craftsmanship.
Post time:Dec - 12 - 2024