Understanding Metal Cutting Discs Composition and Uses
Metal cutting discs, also known as metal cutting wheels or blades, are essential tools in various industries and DIY projects. Used primarily with angle grinders, these discs are designed for efficiently cutting through different types of metals, including steel, aluminum, and various alloys. To appreciate the effectiveness of these discs, it is important to understand what they are made of and how those materials influence their performance.
Composition of Metal Cutting Discs
Metal cutting discs are typically made from a combination of materials that enhance their durability, cutting efficiency, and safety
. The primary components of these discs include1. Abrasive Materials - The most common abrasive materials used in metal cutting discs are alumina (aluminum oxide) and zirconia alumina. These materials are integral to the cutting process, providing the necessary hardness to effectively grind through metal. - Some specialized discs may use diamond particles, especially in applications requiring cutting through hard materials like stainless steel or other tough alloys.
2. Bonding Agents - The abrasives need to be held together, which is where bonding agents come into play. These agents are typically made from resin or other synthetic compounds. The bonding material forms a matrix that holds the abrasive particles in place while allowing them to wear down and expose new edges during use. - Different bonding agents lead to discs designed for various applications, ranging from soft to hard metals.
3. Reinforcement - To enhance safety and durability, cutting discs are often reinforced with fiberglass or other synthetic materials. This reinforcement prevents the disc from shattering during use, which can occur due to high RPMs or excessive pressure. - The number of layers and the type of reinforcement depend on the intended use of the disc. For instance, more demanding applications may require thicker and more heavily reinforced discs.
4. Size and Thickness - Metal cutting discs come in various sizes and thicknesses, which affect their cutting capabilities and versatility. Thinner discs (often around 1mm to 3mm thick) are generally preferred for quick, clean cuts, whereas thicker discs provide greater stability and durability for heavy-duty cutting tasks. - Diameter also plays a crucial role; larger discs are better for cutting through thicker materials, while smaller discs are ideal for intricately detailed work.
what are metal cutting discs made of
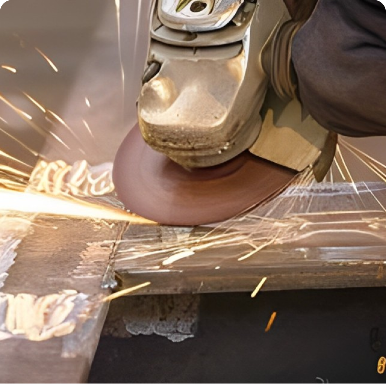
Applications of Metal Cutting Discs
The versatility of metal cutting discs makes them suitable for a wide range of applications
- Construction and Metal Fabrication Metal cutting discs are used to cut metal sheets, bars, and pipes in construction sites and fabrication shops. They are essential for tasks such as building frames, creating reinforcements, and more. - Automotive Industry In the automotive sector, these discs are employed for cutting various components during repairs, modifications, and custom fabrications. - DIY Projects Hobbyists and DIY enthusiasts often use metal cutting discs for home improvement projects, metal art, and repairs.
Safety Considerations
While metal cutting discs are incredibly useful, it is crucial to prioritize safety. Proper training in using angle grinders, wearing protective gear (gloves, goggles, and face shields), and following manufacturer guidelines are all vital to ensure safe operation.
Conclusion
In summary, metal cutting discs are sophisticated tools composed of various abrasive materials, bonding agents, and reinforcements designed to enhance cutting efficiency and safety. Their diverse applications across industries showcase their importance in metalworking, while understanding their composition helps users choose the right disc for their specific needs. By prioritizing safety and selecting the appropriate materials, users can achieve optimal performance and results in their cutting tasks.
Post time:Dec - 15 - 2024