Different Types of Grinding Wheels and Their Uses
Grinding wheels are essential tools in various machining and manufacturing processes. They consist of abrasive particles that grind, shape, or polish materials, particularly metals. The performance and efficiency of grinding processes largely depend on the type of grinding wheel used. Understanding the different types of grinding wheels is crucial for selecting the right wheel for specific applications. This article explores the various types of grinding wheels and their uses.
1. Straight Grinding Wheels
Straight grinding wheels are the most common type and are typically used in a bench grinder. These wheels are flat and offer a wide range of applications, including surface grinding, cylindrical grinding, and tool and cutter grinding. They are designed for grinding flat surfaces and can be made from various materials, including aluminum oxide, silicon carbide, and diamond, depending on the material being worked on.
2. Cylinder and Wheel Grinding Wheels
Cylinder and wheel grinding wheels have a cylindrical shape and are used primarily for external grinding applications. The edges of these wheels are designed to grind the workpiece's outer surface, making them ideal for creating intricate shapes and profiles. Their design allows for a larger contact area, which can improve efficiency and reduce overheating during operations.
3. Cup Grinding Wheels
Cup grinding wheels are specialized for grinding complex shapes and are often used in die grinding applications. Their bowl-like structure allows for grinding on the interior or exterior edges of components. They are commonly employed in the automotive industry for finishing tasks and can work on various materials, including metal, glass, and ceramics.
Similar to cup wheels, flared-cup grinding wheels have a more pronounced conical shape. These wheels are effective for grinding in harder-to-reach areas and are often used in tool and die work. The flared design enables them to access intricate corners and dimensions while providing a stable grinding surface, making them versatile for detailed machining tasks.
what are the different types of grinding wheels
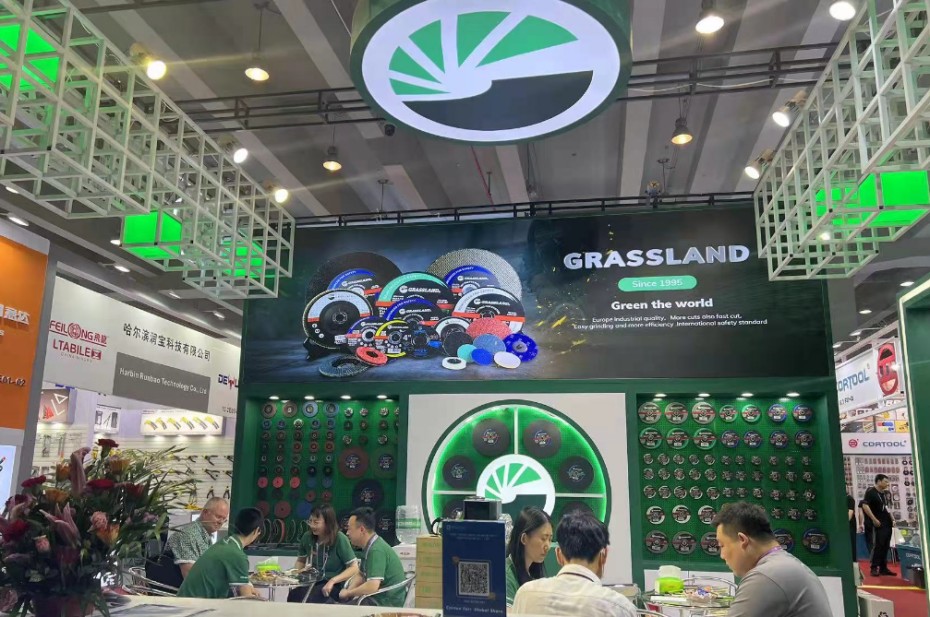
5. Segmented Grinding Wheels
Segmented grinding wheels feature a series of distinct segments separated by spacing grooves. This design helps reduce overheating and can increase the efficiency of material removal. Segmented wheels are often used for heavy grinding applications, and their construction allows for greater airflow, making them ideal for grinding hard materials or performing high-speed tasks.
6. Diamond Grinding Wheels
Diamond grinding wheels are specifically engineered to handle very hard materials, such as ceramics, composites, and tungsten carbide. With diamonds embedded in the abrasive matrix, these wheels offer superior performance in grinding, polishing, and even cutting. They are especially useful in industries like stone and masonry or for applications where extreme precision is required.
7. CBN Grinding Wheels
Cubic boron nitride (CBN) grinding wheels are known for their exceptional hardness and thermal stability. Like diamond wheels, CBN wheels are used for grinding hard materials, primarily ferrous metals. They are highly efficient in producing fine finishes and tight tolerances, making them a favored choice in precision applications.
8. Resin Bonded Grinding Wheels
Resin-bonded grinding wheels provide flexibility and better shock absorption compared to metal-bonded wheels. The resin allows for more precise grinding and is often used in various applications, including surface grinding, tool sharpening, and general-purpose grinding. Their versatility makes them a popular choice among metalworkers and machinists.
Conclusion
Selecting the appropriate grinding wheel is vital for maximizing performance and achieving desired results in machining processes. The variety of grinding wheels available today caters to different materials and applications, making it essential for professionals to choose wisely. Whether it's for precision grinding, surface finishing, or shaping complex geometries, understanding the various types of grinding wheels ensures optimal results in any manufacturing setting.
Post time:Oct - 13 - 2024