The Use and Benefits of Zirconia Flap Discs in Abrasive Processes
Zirconia flap discs are increasingly becoming a popular choice in various industrial applications for grinding, blending, and finishing materials. These specialized abrasives stand out due to their unique composition of zirconia alumina, which provides exceptional durability and performance in multiple contexts. In this article, we will explore the advantages, applications, and optimal use of zirconia flap discs in abrasive processes.
Understanding Zirconia Flap Discs
Flap discs are tools composed of a central hub, with overlapping pieces of abrasive cloth arranged radially around it. Zirconia flap discs are specifically made from zirconium oxide, a material that possesses remarkable hardness and toughness. This makes zirconia flap discs well-suited for heavy metal grinding and high-pressure applications. The combination of improved performance and longer life expectancy places them ahead of other abrasive products like aluminum oxide discs.
Advantages of Zirconia Flap Discs
1. Durability One of the most significant advantages of zirconia flap discs is their long lifespan. The zirconium oxide grains maintain their cutting ability longer than other abrasives, making them ideal for continuous use in tough applications.
2. Versatility Zirconia flap discs can be used on a range of materials, including stainless steel, carbon steel, and non-ferrous metals. Their versatility allows them to perform well in both grinding and finishing operations, reducing the need for multiple tools.
3. Enhanced Productivity Due to their high removal rates, zirconia flap discs increase productivity in abrasive operations. The efficiency of these discs aids in reducing overall processing time without compromising the surface finish.
4. Consistent Finish The fabric layers in zirconia flap discs provide a finer finish than traditional grinding wheels. This consistency is crucial for industries requiring precision, such as automotive, aerospace, and metal fabrication.
5. Reduced Heat Generation Zirconia flap discs are designed to dissipate heat better than conventional abrasives, which minimizes the risk of warping or damaging the workpiece. This characteristic is especially vital when working with heat-sensitive materials.
Applications of Zirconia Flap Discs
zirconia flap disc use
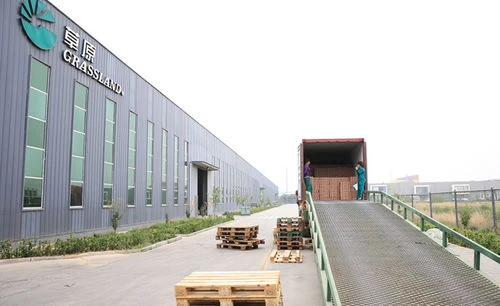
Zirconia flap discs find their application across various sectors. In metalworking, they are commonly used for deburring, surface preparation, and weld blending. In woodworking, these discs help achieve a smooth finish on hardwood surfaces. The construction industry also benefits from zirconia flap discs for shaping and smoothing concrete and masonry surfaces.
In the automotive industry, where precision is paramount, zirconia flap discs assist in eliminating imperfections on engine parts and chassis components. Similarly, the aerospace sector utilizes these discs to ensure that components meet stringent industry standards regarding surface finish and structural integrity.
Best Practices for Using Zirconia Flap Discs
To maximize the benefits of zirconia flap discs, it is essential to follow specific best practices during usage
- Choose the Right Grit Selecting the appropriate grit is crucial for achieving the desired surface finish. Coarser grits (e.g., 40-60) are suitable for aggressive material removal, while finer grits (e.g., 80-120) are better for finishing tasks.
- Apply Appropriate Pressure Excessive pressure during the grinding process can lead to premature wear of the flap disc and increased heat generation. A steady, moderate pressure is recommended to optimize performance and lifespan.
- Maintain Proper Angle For best results, use the flap disc at the correct angle (usually 15 to 30 degrees) to the workpiece. This position allows for effective material removal while maintaining control and stability.
- Regular Inspection Inspect flap discs regularly for wear and damage. Replacing discs when they become worn out ensures continued efficiency and safety.
Conclusion
Zirconia flap discs are indispensable tools in modern abrasive processes, offering unmatched durability and versatility across a wide variety of materials and applications. Their ability to improve productivity and deliver high-quality finishes makes them a go-to solution for professionals in numerous industries. By adhering to best practices and understanding the unique properties of these discs, users can effectively harness their advantages for superior results in their projects. As technology advances, the role of zirconia flap discs is likely to expand, further cementing their place in the world of surface treatment and material finishing.
Post time:Dec - 11 - 2024