Zirconia vs Ceramic Flap Discs Understanding the Differences and Applications
Flap discs have become essential tools in the field of metalworking and finishing processes. Among the various types available, zirconia and ceramic flap discs are two popular choices known for their durability and effectiveness. Each type offers distinct characteristics suited for different applications. This article delves into the differences between zirconia and ceramic flap discs, highlighting their advantages, applications, and best practices for use.
Material Composition
The primary distinction between zirconia and ceramic flap discs lies in their abrasive material composition. Zirconia flap discs are made from zirconium oxide, a material known for its toughness and durability. This allows zirconia discs to withstand higher temperatures and heavy grinding applications, making them ideal for stainless steel, high-strength alloys, and other hard metals. On the other hand, ceramic flap discs are crafted from aluminum oxide with a specialized ceramic grain structure. This unique composition results in an extremely sharp abrasive that can cut through materials swiftly, making it suitable for aggressive grinding and blending on various surfaces.
Performance and Longevity
When comparing performance, zirconia flap discs stand out for their resilience and prolonged life, particularly in heavy-duty applications. The self-sharpening properties of zirconia allow the discs to maintain their cutting efficiency over time, reducing the number of replacements required during a project. This feature not only provides cost-effectiveness but also ensures a consistent finish, which is paramount in professional environments.
In contrast, ceramic flap discs, while slightly less durable, excel in delivering a fast cut and fine finish. The ceramic grain is designed to fracture during use, exposing fresh, sharp edges that enhance cutting efficiency. This means they provide a superior performance in operations requiring a smooth and refined surface finish. However, they may wear out more quickly than zirconia discs, especially when used on harder materials.
Applications
Both zirconia and ceramic flap discs have their own unique set of applications. Zirconia flap discs are ideal for heavy grinding and deburring, especially on stainless steel and high-tensile materials. They are commonly used in industries such as automotive, aerospace, and metal fabrication due to their robustness and effectiveness in tough conditions.
zirconia vs ceramic flap disc
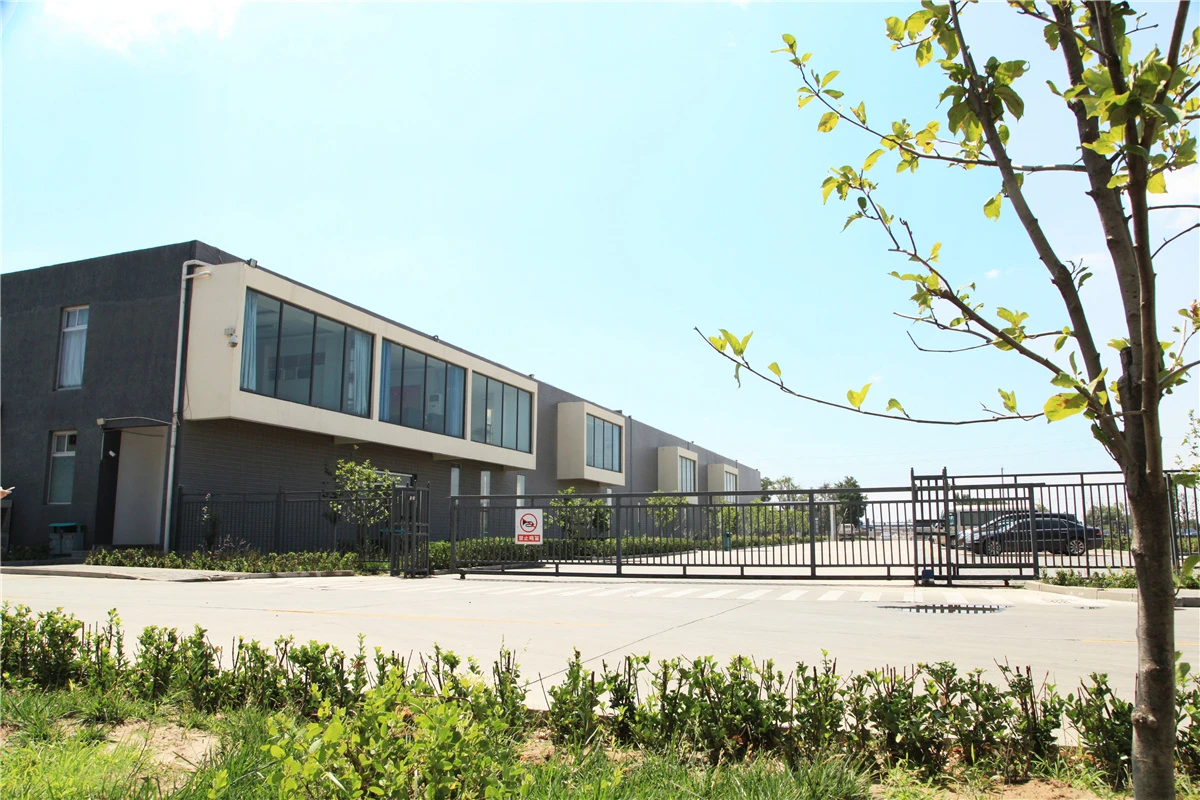
Ceramic flap discs, by contrast, are better suited for applications demanding a finer finish and rapid material removal. They are frequently employed in woodworking, metal art, and surface preparation where a high-quality finish is essential. The fast cut rate of ceramic discs makes them perfect for paint and rust removal, as well as for achieving a polished surface on metals.
Best Practices for Use
To maximize the performance and longevity of both zirconia and ceramic flap discs, users should adopt specific best practices
1. Choose the Right Grit Selecting the appropriate grit is crucial for achieving desired finishes. Coarse grits are effective for aggressive material removal, while finer grits are best for finishing touches. 2. Correct Speed Settings Operating angle grinders at the right RPM is vital. Excessive speeds may cause overheating, whereas too low speeds can reduce cutting efficiency.
3. Proper Pressure Application Balance the pressure applied during grinding. Applying excessive force can lead to premature wear and potentially damage the disc.
4. Material Compatibility Always match the disc type to the material being worked on. For example, opt for zirconia for tough metals and ceramic for softer materials needing a refined finish.
Conclusion
In summary, both zirconia and ceramic flap discs serve invaluable roles in metalworking and finishing processes. By understanding their unique characteristics and applications, users can make informed decisions and enhance productivity. Whether opting for the durability of zirconia or the cutting efficiency of ceramic, selecting the right flap disc is crucial for achieving optimal results in any project.
Post time:Dec - 21 - 2024