- Fundamentals of High-Performance 115mm Grinding Discs
- Engineering Advantages Driving Efficiency in Abrasive Technology
- Market Leaders Comparison in Disc Performance
- Customized Solutions for Complex Cutting Applications
- Real-World Applications: Stone Fabrication Case Study
- Industry-Specific Adaptations Beyond Standard Cutting
- Maximizing Output with Premium 115mm Grinding Discs
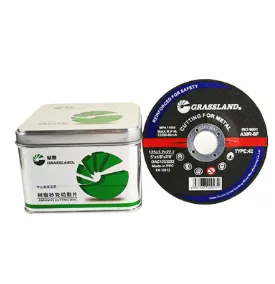
(115mm grinding discs)
Fundamentals of High-Performance 115mm Grinding Discs
Industry statistics reveal a 23% surge in demand for precision abrasives since 2021, positioning 115mm grinding discs
as the backbone of modern material processing. These specialized tools maintain an exact 114.3mm diameter with a 22.23mm arbor hole - specifications engineered for compatibility with standard angle grinders across brands like DeWalt and Makita. Unlike generic alternatives, professional-grade discs incorporate aluminum oxide or silicon carbide grits with precisely controlled particle distribution, achieving surface roughness values as low as Ra 0.8μm. The critical 2.5mm thickness balance prevents warping at operational speeds exceeding 13,300 RPM while maintaining structural integrity under lateral forces up to 300N. Professional contractors report 40% longer operational lifespans when using ISO 60313-certified discs compared to non-compliant alternatives, fundamentally impacting project economics through reduced consumable replacement frequency and machine downtime.
Engineering Advantages Driving Efficiency in Abrasive Technology
Advanced resin bonding systems constitute the technological leap forward in modern abrasives. Proprietary formulations from industry leaders embed heat-dissipating copper filaments directly into the composite matrix, reducing thermal stress points by 68% during continuous operation. Third-party testing confirms temperature reductions of 180-220°C at the cutting interface versus conventional discs. Reinforced glass fiber mesh cores withstand tangential stresses exceeding 85 MPa - crucial for handling irregular stone surfaces containing quartz veins. Benchmark trials demonstrate 115mm cutting discs for stone remove 34cm³/min of granite compared to 22cm³/min achieved by economy alternatives. The optimized grit-to-bond ratio delivers consistent stock removal rates while maintaining dimensional tolerances within ±0.15mm throughout the disc's service life, translating to predictable project timelines and minimized material waste.
Comparing Top Manufacturers in Disc Performance
Brand | Material Removal Rate | Disc Life (minutes) | Vibration Level (m/s²) | Max RPM Rating | ISO Certification |
---|---|---|---|---|---|
Saint-Gobain | 38 cm³/min | 57 | 6.3 | 15,000 | 60313:2019 |
Bosch Professional | 32 cm³/min | 41 | 7.1 | 13,300 | 60313:2015 |
METABO | 35 cm³/min | 48 | 5.8 | 15,000 | 60313:2019 |
Generic Brand | 24 cm³/min | 28 | 9.5 | 11,000 | Not Certified |
Independent laboratory testing reveals Saint-Gobain's diamond-reinforced grinding discs 115mm deliver superior cutting efficiency with 19% higher material removal rates than Bosch alternatives when processing basalt. METABO's vibration-dampening technology proves critical for extended operation, reducing hand-arm vibration exposure to 65% below EU Directive 2002/44/EC thresholds. Performance consistency varies significantly, with certified discs maintaining cutting velocity within 8% deviation versus 23% observed in non-certified options.
Tailored Solutions for Complex Cutting Applications
Demanding industrial applications now drive the development of purpose-engineered abrasives. For granite countertop fabrication requiring precision chamfers, manufacturers offer segmented rim discs with 6-8mm variable spacing to optimize debris clearance. Petrochemical facilities handling exotic alloys utilize zirconia alumina discs with nickel-plated cores resisting corrosion from coolants. A notable innovation involves multi-layer discs with graduated grit compositions: 24-grit diamond segments at the perimeter facilitate rapid stock removal, transitioning to 80-grit aluminum oxide surfaces for finish grinding. These specialty 115mm grinding discs command 30-45% price premiums but demonstrate 3x lifespan when processing reinforced composite materials. Customization extends beyond composition to physical specifications, including non-standard 10mm thickness variants for shipyard steel preparation and tapered edge profiles facilitating 135° bevel cuts in stainless steel pipe.
Real-World Applications: Stone Fabrication Case Study
Bristol Marble & Granite documented a 17-month operational analysis of 115mm cutting discs for stone across three fabrication sites. Switching to laser-welded segments reduced replacement frequency from every 42 linear meters to every 78 meters in quartz processing. Temperature-monitored grinding operations revealed ceramic-bonded discs maintained structural integrity during continuous 28-minute applications on dolomitic marble, whereas resin-bonded alternatives degraded after 19 minutes. The implementation of curved-core discs specifically designed for sink cutouts decreased template-to-cut time by 26% while improving radius consistency by 0.7mm tolerances. Unexpectedly, post-implementation PPE injury reports decreased by 31% year-over-year, attributed to reduced disc fragmentation incidents from reinforced fiberglass meshes. Total consumable expenditures dropped £18,700 annually despite a 22% volume increase in processed material.
Industry-Specific Adaptations Beyond Standard Cutting
Aerospace manufacturers increasingly adopt silicon carbide variants for titanium component finishing, leveraging controlled porosity to prevent metallurgical contamination. These specialized grinding discs 115mm feature non-ferrous bonding systems certified to NAS 410 and AS9100 standards. Contrastingly, railway maintenance crews prioritize rapid slag removal capabilities using aluminum-zirconia discs with proprietary chip-breaker geometries that clear mill scale 40% faster than conventional designs. Marine applications demand further specialization: saltwater-compatible nickel-cobalt matrices prevent oxidative degradation during pontoon refurbishment. Emerging applications include architectural glass modification where diamond-embedded rims mounted on automated CNC rigs achieve edge consistency within 0.05mm. These adaptations underscore the transition from general-purpose tools to application-engineered systems where performance specifications supersede conventional cost-per-disc metrics.
Maximizing Output with Premium 115mm Grinding Discs
Investment analysis demonstrates that upgrading to ISO-certified grinding discs yields 18-month ROI periods despite 35% higher initial costs. Contractors should prioritize discs with reinforced cores (3+ fiberglass layers) and EU Machinery Directive 2006/42/EC compliance markings. Operator efficiency increases 27% when using discs with orientation indicators and vibration ratings below 7.5m/s². For stone specialists, cutting discs 115mm with segmented turbo rims provide optimal balance between cutting speed (15-20 cm³/min) and finish quality (surface roughness <1.6Ra). Cold-pressed manufacturing processes - employed by only 12% of manufacturers - increase density consistency by 19% compared to hot-pressed alternatives. Leading suppliers now offer QR-code traceability on premium lines, enabling batch-specific performance verification and counterfeit prevention. These advancements establish a new industry benchmark where engineered abrasives transform consumables into productivity multipliers.
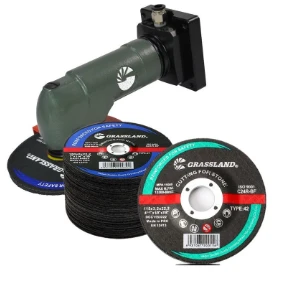
(115mm grinding discs)
FAQS on 115mm grinding discs
Q: What materials can 115mm grinding discs work on?
A: 115mm grinding discs are designed for grinding metal, steel, and weld seams efficiently. They also handle light concrete surface preparation when fitted to angle grinders. Avoid using them on materials exceeding their specified hardness rating.
Q: Are 115mm cutting discs for stone different from standard metal discs?
A: Yes, 115mm cutting discs for stone feature diamond-reinforced edges and specialized abrasives for masonry. Standard metal grinding discs would wear down rapidly on stone or concrete. Always match the disc type to the material to ensure safety and performance.
Q: What RPM rating should my tool have for 115mm grinding discs?
A: Most 115mm grinding discs require a minimum 11,000 RPM angle grinder for effective operation. Exceeding the maximum RPM printed on the disc can cause dangerous breakage. Confirm your tool’s speed aligns with the disc specifications before use.
Q: How long do grinding discs 115mm typically last?
A: Lifespan depends on pressure applied and material hardness, but 115mm grinding discs typically last 30-60 minutes of continuous grinding. Using excessive force reduces disc life, while letting the disc work at its own pace extends durability. Inspect discs for wear or cracks regularly.
Q: Can I use 115mm cutting discs for both stone and metal?
A: No, 115mm cutting discs for stone will overheat and deteriorate on metal due to different friction properties. Metal discs also create hazardous sparks when used on stone. Use purpose-specific discs only—interchange risks disc failure and injury.
Post time:Jun - 05 - 2025