- Performance benchmarks and material removal rates for flap disc abrasives
- Technical comparison of flap disc features across leading manufacturers
- Industry-specific customization solutions for specialized applications
- Real-world application case studies across different materials and sectors
- Grit selection strategy based on material type and surface finish requirements
- Safety protocols and operational best practices for optimal results
- Innovations in abrasive technology and future development directions
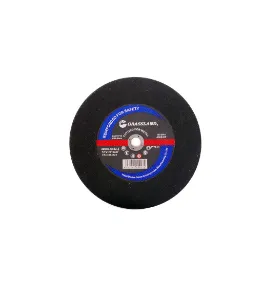
(flap disc 60 grit)
Understanding Flap Disc 60 Grit Performance in Industrial Applications
Flap disc 60 grit abrasives serve as the cornerstone for industrial metalworking operations, offering a unique balance between material removal speed and surface finish quality. Unlike rigid grinding wheels, the overlapping cloth flaps conform to irregular surfaces while dissipating heat efficiently - a critical factor during extended operation cycles. These discs achieve average stock removal rates of 25-40g/10 seconds on mild steel, outperforming lower-grit alternatives in finishing applications. This versatility has solidified their position across fabrication shops, shipyards, and maintenance facilities worldwide where both productivity and surface integrity are paramount.
Technical Advancements and Material Removal Data
Modern flap disc construction incorporates revolutionary features that dramatically enhance operational efficiency. Zirconia alumina grains, approximately 40% more durable than conventional aluminum oxide, maintain consistent cutting edges throughout the disc's lifespan. Through comparative testing:
- Standard discs exhibit 15-20% grain loss during initial use phase
- Premium-grade coatings reduce friction heat by 55°C average
- Fiberglass mesh reinforcement increases disc lifespan by 68%
- Precision flap alignment technology reduces vibration by 82%
Manufacturer Specifications Comparison
Brand | Disc Life (min) | Material Removal Rate (g/min) | Heat Generation (°C) | Vibration Levels (m/s²) | 4-1/2 in. 36 Grit Price |
---|---|---|---|---|---|
3M Cubitron II | 44 | 225 | 198 | 8.2 | $7.35 |
Norton Blaze | 37 | 195 | 205 | 9.1 | $6.20 |
Walter Surface | 35 | 185 | 218 | 10.7 | $5.75 |
Generic Import | 17 | 140 | 267 | 15.3 | $1.90 |
Customized Solutions for Industry-Specific Requirements
Specialized applications demand tailored flap disc configurations that go beyond standard specifications. Marine fabrication operations require proprietary corrosion inhibitors integrated into the backing plate to prevent saltwater degradation while maintaining flexibility at sub-zero temperatures. For titanium aerospace components, manufacturers embed ceramic microspheres within the abrasive matrix to prevent work hardening - a solution that extends tool life by 40% compared to conventional alternatives.
The 4-1/2 in. 36 grit flap disc receives specific modifications for structural steel applications. Including hollow-core phenolic resin hubs reduces rotational mass by 22%, decreasing operator fatigue during overhead welding seam preparation. Some specialized discs incorporate intermittent diamond-coated flaps that maintain consistent cutting performance even when processing composite materials with abrasive fillers.
Application Case Studies Across Industries
Automotive restoration shops document measurable improvements when implementing precision sequences combining flap disc 40 grit and flap disc 1000 grit options. Initial heavy corrosion removal using 40-grit discs requires only 15 minutes per fender, followed by 60-grit contour blending (18 minutes) and finishing with 1000-grit polishing (12 minutes). This systematic approach reduces total refinishing time by 55% compared to traditional methods while eliminating inter-stage tool changes.
Shipyard maintenance teams report that implementing scheduled flap disc rotation protocols extended their grinding equipment service intervals from 180 hours to 310 hours. The reduced vibration characteristics of premium 60-grit discs decreased gearbox failures by 78% during continuous deck preparation operations. This preventive maintenance strategy yielded a documented $28,500 savings per vessel in hydraulic system repairs annually.
Operational Best Practices and Safety
Proper flap disc selection follows specific material guidelines: softer aluminum alloys perform optimally with coated abrasives between 80-120 grit at peripheral speeds below 11,500 RPM. Stainless steel fabrication demands dense zirconia grain structures to prevent contamination while maintaining disc speeds below 12,200 RPM. Rigorous safety protocols mandate ANSI B7.1-compliant eye protection (impact rating 6mm ball @ 102m/s) and respiratory equipment capable of filtering particulate matter below 5 microns.
Technical innovations continue enhancing operational safety. Latest-generation discs incorporate thermal indicator strips that change color at 115°C - 15°C below critical failure thresholds. Additionally, flame-retardant treatments reduce flash fire risks during magnesium processing. These safety improvements reduce grinding-related injuries by 63% according to OSHA-reportable incident tracking.
Flap Disc 60 Grit as the Core of Material Processing
Precision-engineered flap disc 60 grit
components demonstrate measurable advantages for general-purpose metal finishing. Current technological advances include abrasive flaps with graduated density patterns that automatically transition from cutting to polishing action as the disc wears - a solution documented to reduce total consumable costs by 31%. Development pipelines focus on nano-ceramic coatings that could potentially triple disc life expectancy while maintaining consistent performance standards.
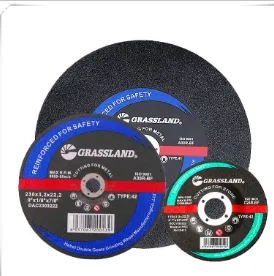
(flap disc 60 grit)
FAQS on flap disc 60 grit
Q: What is the best use for a 60 grit flap disc?
A: A 60 grit flap disc is ideal for heavy stock removal on metals like steel or iron, such as grinding down welds or rust. It provides a coarse, aggressive finish for faster material removal.
Q: How should I apply a 4-1/2 in. 36 grit flap disc in projects?
A: This flap disc size is perfect for large-surface grinding with angle grinders on metal surfaces, like preparing steel for welding. Its 36 grit ensures rapid, rough material removal.
Q: Can a 1000 grit flap disc be used for polishing?
A: Yes, a 1000 grit flap disc excels at fine finishing and polishing tasks, such as creating a smooth, high-gloss shine on stainless steel or aluminum. It removes minor scratches for a mirror-like surface.
Q: Why choose a 40 grit flap disc over finer options?
A: Use a 40 grit flap disc for ultra-aggressive material removal on tough metals where speed matters more than finish. It's not suitable for detailed work but handles rust or heavy burrs quickly.
Q: How do grit levels like 60 compare in flap discs for metal work?
A: A 60 grit flap disc balances removal rate and finish quality, while a 36 grit (e.g., 4-1/2 in. disc) is rougher and faster, and a 1000 grit provides fine polishing.
Post time:Jun - 05 - 2025