The Significance of the 1% Cutting Wheel in Precision Engineering
The world of precision engineering and machining is ever-evolving, with advancements in technology continuously shaping the tools and equipment used in manufacturing. Among these advancements, the 1% cutting wheel stands out as a pivotal innovation, offering a unique blend of efficiency, precision, and versatility that significantly enhances machining processes.
What is a 1% Cutting Wheel?
The term 1% cutting wheel often refers to a cutting wheel that is designed to operate with an impressive degree of accuracy, capable of making precision cuts with minimal material loss. These cutting wheels are typically used for various applications, including metalwork, woodworking, and industrial fabrication. The 1% denotes the cutting wheel’s exceptional ability to maintain high accuracy and minimal deviation from specified dimensions during operations.
These cutting wheels are constructed from high-quality materials, often reinforced with abrasives that increase both their durability and cutting efficiency. Common materials used in the making of these wheels include aluminum oxide, silicon carbide, and diamond, depending on the application and material being cut.
Advantages of Using 1% Cutting Wheels
1. Precision Cutting The primary advantage of the 1% cutting wheel lies in its ability to perform precise cuts consistently. This precision is particularly important in industries where exact dimensions are critical for fitting components together, such as in aerospace, automotive, and construction.
2. Efficiency With a cutting wheel that maintains high performance, manufacturers can achieve cleaner cuts in shorter times. This efficiency translates into less time spent on grinding or finishing processes, thus reducing overall production cycles.
3. Reduced Material Waste The design of the 1% cutting wheel minimizes the width of the cut, allowing for less wastage of raw materials. This characteristic not only saves costs but is also beneficial from an environmental perspective, as it promotes more sustainable manufacturing practices.
1 mm cutting wheel
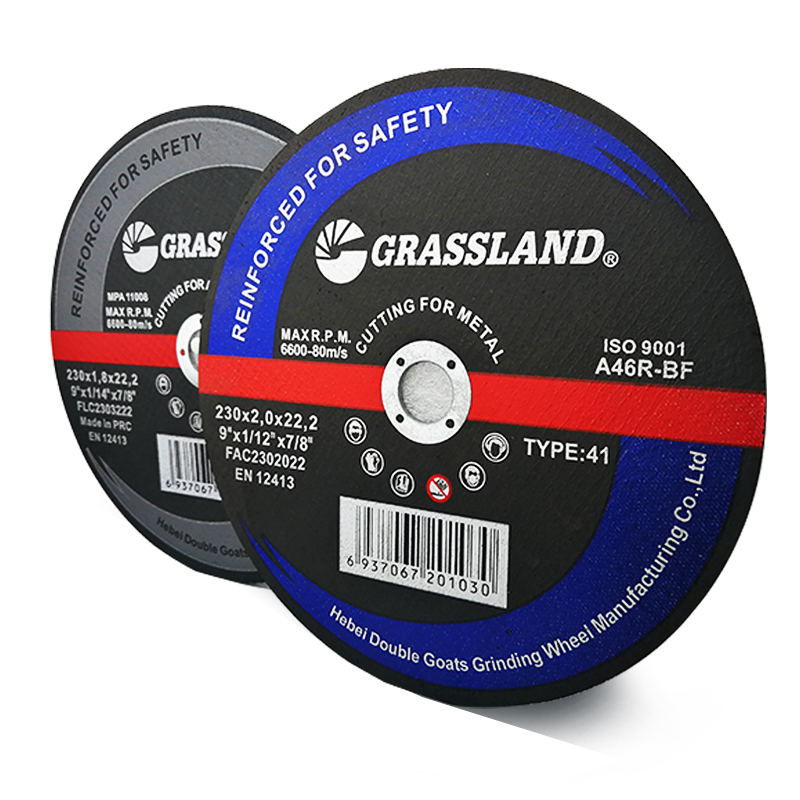
4. Versatility 1% cutting wheels can be used on a wide array of materials, including metals, plastics, and composites. This versatility makes them essential tools in various sectors, enabling machinists and engineers to utilize a single wheel for multiple projects.
5. Enhanced Safety Many modern cutting wheels, including the 1% variants, are designed with safety features that reduce the risk of accidents during operation. This is crucial in high-speed environments where precision and safety are paramount.
Applications in Various Industries
1. Manufacturing In manufacturing processes, precision is key. The 1% cutting wheel is extensively used in cutting metal sheets, rods, and intricate parts that require tight tolerances. Its effectiveness ensures that manufacturers can produce high-quality products consistently.
2. Construction In the construction industry, these cutting wheels are vital for tasks such as cutting rebar and other structural materials. The ability to make precise cuts helps in maintaining the integrity of structures.
3. Aerospace and Automotive Both industries rely heavily on precision machining to produce components that meet rigorous safety and performance standards. The 1% cutting wheel is a preferred choice for cutting high-strength alloys and other difficult-to-machine materials.
Conclusion
The 1% cutting wheel is an essential tool in the realm of precision engineering. Its advantages of precision, efficiency, reduced waste, versatility, and enhanced safety make it a preferred choice among manufacturers and engineers alike. As industries continue to demand higher standards of quality and efficiency, the role of such innovative tools will undoubtedly grow, further shaping the landscape of modern machining and manufacturing processes. Embracing advancements like the 1% cutting wheel is crucial for companies seeking to maintain their competitive edge in an increasingly demanding marketplace.
Post time:Dec - 15 - 2024