The Four Types of Grinding Machines
Grinding machines are essential tools in manufacturing and engineering industries for shaping and finishing materials. These machines help to achieve an improved surface finish, remove excess material, and sharpen or shape workpieces. Understanding the different types of grinding machines can help in selecting the right tool for specific tasks. Here, we will explore the four main types of grinding machines surface grinders, cylindrical grinders, centerless grinders, and tool & cutter grinders.
1. Surface Grinders
Surface grinding machines are used to produce a smooth, flat surface on a workpiece. This type of grinding machine uses a rotating abrasive wheel to remove material from the surface of the workpiece. The workpiece is typically mounted on a magnetic chuck, which holds the piece securely in place during the grinding process.
Surface grinders can be categorized into horizontal and vertical spindle types, depending on the orientation of the spindle to the worktable. The horizontal spindle surface grinder features a rotating wheel that operates parallel to the work surface, while the vertical spindle surface grinder has a wheel that spins perpendicular to the work surface. Surface grinding is commonly used for finishing metals, making adjustments in dimensions, or providing a clean and aesthetic appearance.
Cylindrical grinding machines are designed to handle cylindrical workpieces. The primary function of these machines is to grind the outer surface of cylindrical components, which can include shafts, spindles, and bushings. The critical feature of cylindrical grinders is the ability to rotate the workpiece while the grinding wheel remains stationary or moves in a set path.
These machines can be divided into two categories external and internal cylindrical grinders. External cylindrical grinders grind the outer diameter of the workpiece, while internal cylindrical grinders are used to grind the inner diameter of a workpiece, such as a tube or a hole. Cylindrical grinding is widely used in manufacturing parts with precise dimensions and tight tolerances.
what are the 4 types of grinding machine
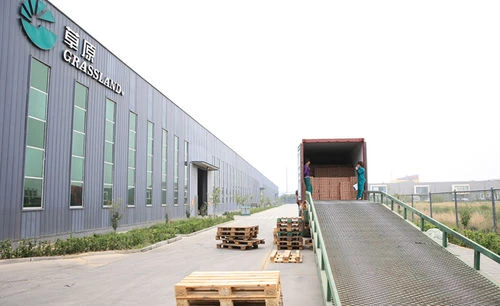
3. Centerless Grinders
Centerless grinding machines are specialized tools that allow for the grinding of a workpiece without the need for a spindle fixture. In these machines, the workpiece is positioned between two grinding wheels the regulating wheel and the grinding wheel. The regulating wheel controls the feed rate, while the grinding wheel removes material from the workpiece.
The unique advantage of centerless grinding is its ability to handle parts that cannot be easily clamped, allowing for increased efficiency and higher production rates. Additionally, centerless grinders are often used for machining small parts in high volumes, making them ideal for industries that require precision components, such as automotive and aerospace.
4. Tool and Cutter Grinders
Tool and cutter grinding machines are versatile machines used for sharpening and fabricating cutting tools and drills. These machines use a rotating wheel to grind the cutting edges of tools to restore their sharpness and improve their performance.
The tool and cutter grinder is designed to handle a wide variety of cutting tools, including end mills, reamers, and complex shapes. The operator can adjust the grinding angle and the position of the tool to achieve the desired cutting edge geometry. This type of grinding machine is crucial for maintaining the efficiency of various cutting tools used in manufacturing and machining processes.
Conclusion
In conclusion, the four types of grinding machines—surface grinders, cylindrical grinders, centerless grinders, and tool and cutter grinders—each serve a distinct purpose in the realm of manufacturing and engineering. Understanding the functionalities and applications of these machines is essential for optimizing production processes and achieving high levels of precision in workpieces. By choosing the appropriate type of grinding machine, manufacturers can enhance productivity, ensure quality control, and maintain a competitive edge in the market. The advancements in grinding technology continue to play a vital role in pushing the boundaries of manufacturing capabilities.
Post time:Dec - 15 - 2024