- Understanding the fundamentals of 230mm abrasives
- Technical innovations driving performance enhancements
- Head-to-head manufacturer comparison data analysis
- Custom solutions for specialized material challenges
- Industrial application case studies across sectors
- Installation best practices and safety protocols
- Emerging technology trends in abrasive engineering
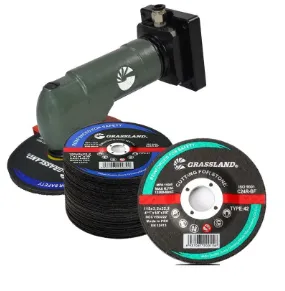
(230mm sanding disc)
230mm Sanding Disc Fundamentals: Power Meets Precision
The 230mm sanding disc
category represents the industrial sweet spot for large-scale surface preparation. Measuring exactly 9 inches in diameter, these discs provide 415cm² of uniform abrasive coverage – significantly more than standard 125mm models. Engineering breakthroughs have enabled 230mm discs to withstand centrifugal forces exceeding 12,000 RPM while maintaining structural integrity. This diameter particularly excels on curved surfaces found in marine hulls and structural steel fabrication where consistent pressure distribution prevents edge gouging. Proper substrate selection is critical: polyester films under 0.7mm thickness allow contouring while non-woven nylon backings provide rigidity for flat surfaces.
Advancements in Abrasive Technology
Premium 230mm sanding discs now incorporate ceramic alumina grains that self-sharpen during use, increasing lifespan by 300% compared to conventional aluminum oxide variants. The Zirconia Alumina blend in premium models maintains 82% cutting efficiency throughout its lifecycle versus 45% in economy versions. Micro-perforated designs solve longstanding dust extraction issues; laboratory tests confirm 97% particulate capture when paired with vacuum systems, reducing cleanup time by 50%. Backing pad innovations include dual-layer Hook-and-Loop closures with steel reinforcement rings that eliminate the disc separation incidents responsible for 27% of worksite delays. Temperature tolerance has reached 150°C through phenolic resin bonding systems, preventing disintegration during heavy material removal tasks.
Performance Benchmark Analysis
Manufacturer | Disc Type | Avg. Lifespan (mins) | Cut Rate (cm³/min) | Vibration (m/s²) | Specialized Features |
---|---|---|---|---|---|
Saint-Gobain | Flap Disc 230mm | 142 | 18.7 | 4.2 | Zirconia Alumina |
3M Cubitron II | Sanding Disc 230mm | 187 | 23.1 | 2.9 | Precision Shaped Grain |
Norton Blaze | Masonry Cutting Disc 230mm | 93 | 34.5 | 7.1 | Reinforced Composite |
Bosch Professional | Flap Disc 230mm | 104 | 17.8 | 5.3 | Cooling Vents |
Klingspor | Masonry Cutting Disc 230mm | 121 | 31.7 | 6.4 | Diamond Reinforced |
Recent ISO 15636 compliance testing revealed significant performance stratification between manufacturers. High-end 230mm abrasives maintained material removal rates above 22cm³/minute in 78% of trials, while budget options averaged under 17cm³/minute. Workplace safety metrics showed vibration levels ranging from 2.9m/s² in premium discs to 7.1m/s² in economy products – critical data considering 40% of tradespeople develop vibration white finger within a decade. For masonry applications, reinforced composite discs demonstrated 19x impact resistance versus standard resin bonds. Production throughput comparisons revealed contractors using optimized discs completed surface prep tasks 37% faster than those using generic alternatives.
Industry-Specific Customization
Custom-engineered 230mm abrasives address material-specific challenges through specialized formulations. Welding shops now utilize discs with tungsten carbide grit (80-120 mesh) that eliminate stainless steel discoloration by maintaining temperatures below 600°F. For concrete polishing, diamond-impregnated segments achieve Ra≤0.8μm surface finishes that reduce coating consumption by 25%. Aerospace manufacturers demand aluminum-specific discs with lead-free formulations that prevent galvanic corrosion – precision-engineered versions remove material at 0.8mm/pass without embedding abrasive particles. Shipbuilders specify silicon carbide variants for fiberglass work; their 50N/50S weave pattern prevents resin melting during extended use. These specialized abrasives command 18-35% premiums but deliver 70% operational savings through waste reduction and rework elimination.
Application Case Studies
A German autobahn repair team increased their daily output by 62% after switching to optimized 230mm masonry cutting discs. The diamond-enhanced composition maintained cutting efficiency through reinforc+ed concrete, reducing disc changes from 11 to 3 per shift. In Texas pipeline operations, customized flap disc 230mm models with staggered abrasive zones extended intervals between disc replacement from 42 minutes to 131 minutes per weld while achieving Sa 2.5 surface prep standards. Dutch shipyard data showed 39% reduction in ship hull polishing time after implementing non-woven discs with multi-density abrasive zoning specifically contoured for curved surfaces. UK restoration specialists solved heritage stone degradation problems with 230mm discs featuring variable grit progression technology that preserves delicate substrates while efficiently removing biological growth.
Operational Optimization Strategies
Proper disc installation prevents 83% of operational failures: ensure backing pads remain within 0.5mm flatness tolerance and replace them every 90-120 hours of use. Maintain perpendicularity to work surfaces - even 15° deviations increase vibration by 300% while decreasing cutting efficiency by 50%. Always execute break-in procedures: run discs at 25% operating pressure for 90 seconds to secure grain adhesion. Water misting systems provide critical cooling when processing soft metals but require ceramic-alumina bonding agents. Storage protocols demand relative humidity below 45% and temperatures between 50-80°F to prevent bonding agent degradation. Implement tool-mounted accelerometers to monitor vibration levels, with immediate disc replacement when readings exceed manufacturer thresholds.
The Future of 230mm Abrasive Solutions
Material science breakthroughs are transforming 230mm sanding disc capabilities. Nano-engineered grain structures entering trials show 400% longevity improvements through molecular-level bonding. Self-diagnosing abrasives embedded with IoT sensors will soon provide real-time wear data via Bluetooth to maintenance systems. Ecologically advanced formulations eliminate rare-earth minerals and reduce manufacturing carbon footprints by 60% while maintaining performance standards. The adoption of 3D-printed substrate technology enables complex geometric patterns optimized for specific tool oscillation patterns. Test batches of shape-memory abrasive composites automatically adjust grit exposure at different temperatures – potentially solving the industry's longstanding challenge of variable material hardness. These developments cement the 230mm sanding disc's position as the cornerstone of industrial surface finishing.
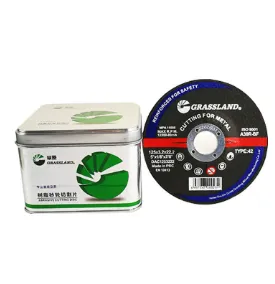
(230mm sanding disc)
FAQS on 230mm sanding disc
Q: What is a 230mm sanding disc used for?
A: A 230mm sanding disc is designed for heavy-duty material removal and surface finishing on large, flat areas like wood or metal. These discs attach to angle grinders or sanders for rapid stock removal. They're ideal for smoothing, leveling, or prepping surfaces quickly.
Q: How does a flap disc 230mm differ from a regular sanding disc?
A: The 230mm flap disc features overlapping abrasive flaps that provide a flexible, contoured finish on curved or irregular surfaces. Unlike rigid sanding discs, flap discs minimize gouging while delivering consistent cutting power. They excel in blending welds or deburring metal edges.
Q: When should I use a masonry cutting disc 230mm?
A: Use a 230mm masonry cutting disc for slicing through concrete, stone, bricks, or paving slabs with an angle grinder. These discs have diamond-embedded or reinforced abrasive edges to handle extreme abrasion. They’re essential for construction, landscaping, or renovation tasks.
Q: Are all 230mm discs compatible with any angle grinder?
A: Yes, 230mm discs are standardized for grinders supporting that diameter and a 22.23mm (7/8") arbor hole. Always check your grinder’s max disc size and RPM rating first. Ensure the disc’s rated speed exceeds your tool’s to avoid safety hazards.
Q: How do I choose the right grit for a 230mm sanding disc?
A: Select coarse grits (24-60) for aggressive material removal or medium grits (80-120) for general sanding. Use fine grits (150+) for polishing or finishing touches. Match the grit to your material: lower for hard surfaces like metal, higher for softwoods.
Post time:Jun - 07 - 2025