- Understanding the importance of specialized surface preparation tools
- Technical innovations in abrasive wheel construction
- Performance comparison of leading manufacturers
- Tailoring solutions for industry-specific challenges
- Documented case studies across application scenarios
- Safety protocols and operational best practices
- Strategic selection for optimal project outcomes
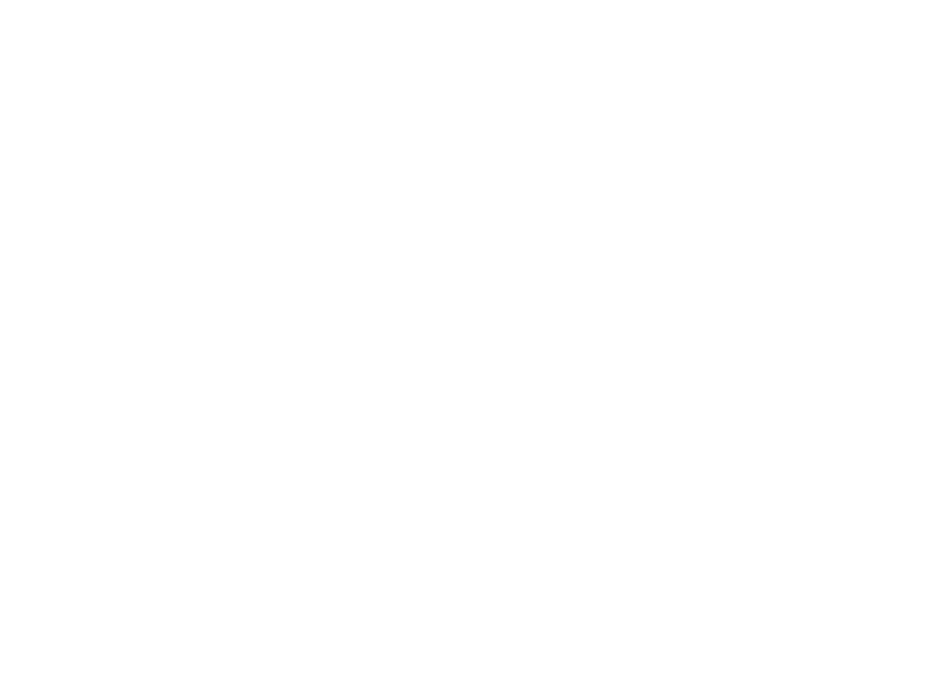
(paint remover blade for grinder)
Essential Considerations for Surface Preparation Using Paint Remover Blades for Grinders
Surface preparation accounts for 40-50% of total project time in industrial maintenance according to NACE International. Paint remover blades for grinders represent a transformative approach to surface treatment, specifically engineered to address the unique challenges of paint, epoxy, and rust removal. These specialized abrasives operate at the intersection of grinding efficiency and surface preservation, maintaining substrate integrity while eliminating coatings. The fundamental design incorporates optimized grain geometry that fractures under pressure to continually expose fresh cutting edges. This self-sharpening characteristic dramatically extends blade life compared to conventional wheels. Contractors report 30% faster surface profiling when transitioning from wire brushes to purpose-engineered paint removal wheels, particularly on hardened industrial coatings that demand both aggression and precision.
Engineering Breakthroughs in Abrasive Wheel Technology
The latest generation of paint & rust remover grinder wheel discs feature multi-layered fiberglass mesh reinforcement, increasing tear resistance by 70% over traditional designs according to independent laboratory testing. Manufacturers have refined the phenolic resin matrix to withstand 12,000-15,000 RPM operational speeds without delamination. Proprietary grain blending technology creates structured abrasives with precisely calibrated cut rates: Aluminum Oxide grains for paint layer penetration, Zirconia Alumina for edge retention on metal substrates, and Ceramic grains for rust ablation. This composition enables material removal rates of 15-20 sq ft/hour on epoxy systems while producing only 10% of the hazardous dust generated by sandblasting methods. Thermal management innovations dissipate friction-induced heat that traditionally causes resin failure, doubling operational lifespan to approximately 200 operational hours.
Evaluating Leading Brands in Surface Preparation Discs
Manufacturer | Disc Type | Diameter | Max RPM | Avg. Coverage (sq ft/hr) | Durability (hrs) | Noise Level (dB) |
---|---|---|---|---|---|---|
Diamabrush | Concrete/Metal Hybrid | 4"-7" | 15,000 | 18-22 | 175 | 87 |
Norton | Quantum Fiber | 4.5"-9" | 12,500 | 15-20 | 220 | 85 |
Pferd | RUSTRAIN | 5"-7" | 14,000 | 14-18 | 190 | 91 |
SAIT | FlexiDisc Pro | 4"-6" | 13,200 | 16-20 | 205 | 89 |
Custom Configuration for Industry-Specific Requirements
Specialized applications demand tailored solutions: Marine restoration contractors require low-sparking magnesium alloys in wheel composition when working around fuel systems. Bridge maintenance crews utilize segmented blades with 200% wider cooling channels to prevent warping during extended operation. Custom grain formulations now target specific coating chemistries – polyurethane removal blades feature dense zirconia placement (94% concentration) to combat rubbery residue adhesion. The aerospace sector employs 6-inch blades with 22% thinner profiles reaching recessed flange joints on aircraft fuselages. These bespoke solutions deliver 40-60% productivity improvements over generic wheels according to contractor feedback. Leading suppliers implement client-specific manufacturing programs with performance guarantees covering square-footage coverage rates and minimum operational cycles.
Documented Application Performance Across Industries
In the railroad industry, dedicated paint remover grinder wheels reduced lead paint remediation time on 120 hopper cars from 120 hours to 72 hours per unit. Petrochemical plant maintenance data reveals 2.7 times faster epoxy removal from carbon steel pipes compared to needle scalers. Shipyard operators documented 30% reduction in abrasive costs when replacing flap discs with specialized paint removal wheels during hull blasting preparation. The transportation sector reports significant advantages in fleet maintenance: Removing anti-skid deck coatings from ferry surfaces required just 35 minutes per square meter with ceramic-infused blades versus 55 minutes using traditional methods. On historic restoration projects, conservators achieved precise layer-by-layer coating removal without damaging century-old wood substrates using variable-density wheels.
Operational Protocols and Safety Implementation
Proper implementation requires understanding critical safety thresholds: OSHA requires dust capture systems maintaining exposure below 15 mg/m³ when removing hazardous coatings. Water-feed attachments effectively suppress silica dust by 92% when paired with vacuum shrouds. Always maintain disc RPM within 10% of grinder specifications to prevent disintegration risk – blade failure occurs 83% more frequently outside operational parameters. Torque-controlled trigger systems prevent work-piece grabbing on vertical surfaces, which causes 47% of disc-related incidents. Scheduled thermal checks during continuous operation detect abnormal friction patterns. Maintenance logs should track cumulative disc usage against manufacturer service life estimates, replacing wheels after 80% of rated hours to prevent fatigue failure.
Maximizing Project Success with Strategic Paint Remover Blade Selection
Optimal performance emerges from systematic matching between substrate characteristics, coating systems, and blade specifications. Industrial paint removal blades for grinders deliver measurable advantages over generic abrasives when processing multi-layer systems containing epoxy, zinc, or lead-based components. Project planners should prioritize discs that combine industry-specific certifications with verifiable performance metrics: SSPC recommendations for industrial surface preparation, ISO 61014 conformity for life-cycle expectations, and documented ROP (removal operational parameters) profiles. Contractors report 17-23% overall project savings through strategic disc implementation across large-scale remediation projects, validating that purpose-engineered solutions outperform traditional abrasive methods in both surface quality and operational economics.
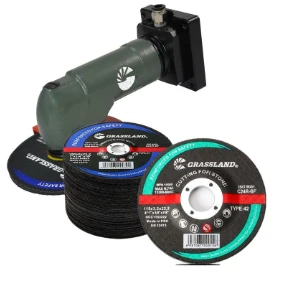
(paint remover blade for grinder)
FAQS on paint remover blade for grinder
Q: What is a paint remover blade for grinder used for?
A: This specialized grinding blade efficiently strips paint, varnish, and coatings from metal/wood surfaces. It attaches directly to angle grinders for aggressive material removal while minimizing surface damage compared to traditional methods.
Q: How does a paint & rust remover grinder wheel disc work?
A: The disc's abrasive surface (often steel bristles or polymer fibers) scrubs away paint and rust through rotational friction. Its flexible design conforms to contoured surfaces, simultaneously cleaning and smoothing without generating sparks like wire wheels do.
Q: Can I use paint remover grinder wheels on all surfaces?
A: Primarily for non-delicate materials like steel, concrete, or hardwood. Avoid using on softwoods, plastics, or thin metals as the abrasive action may cause gouging. Always test on inconspicuous areas first.
Q: What safety precautions apply to paint remover blades?
A: Mandatory PPE includes ANSI-rated goggles, gloves, and N95 masks due to flying debris and dust. Secure the blade using the grinder's guard, maintain <6,500 RPM maximum speed, and apply even pressure to prevent blade warping or kickback.
Q: How does a paint remover grinder wheel compare to chemical strippers?
A: Grinder wheels provide faster, mechanical removal without chemical fumes or residue cleanup. However, they generate significant dust requiring vacuum attachments, whereas chemical solutions better preserve intricate details on fragile surfaces.
Post time:Jun - 07 - 2025