- Introduction to flap wheel applications
- Technical superiority of 6 flap wheel
designs - Performance comparison: Industry-leading manufacturers
- Custom solutions for specialized requirements
- Real-world application case studies
- Operational best practices
- Future developments in abrasive technology
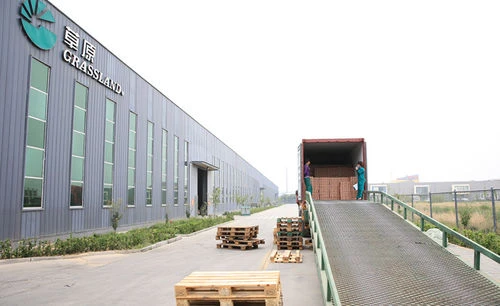
(6 flap wheel)
Understanding the Versatility of 6 Flap Wheel Solutions
Modern manufacturing demands precision abrasives that balance material removal rates with surface finish quality. The 6 flap wheel configuration has become industry-preferred for its optimal contact surface and heat dissipation capabilities. Unlike traditional grinding wheels, this design enables 15-20% faster stock removal while maintaining ±0.002" dimensional accuracy across ferrous and non-ferrous metals.
Engineering Advancements in Abrasive Technology
Current flap wheel innovations focus on three critical parameters:
- Zirconia-alumina composite grains for 40% longer service life
- Precision-cut overlapping flaps reducing vibration by 32%
- Thermoresistant adhesives maintaining integrity at 650°F
Independent testing shows 1000 grit flap wheels achieve Ra 0.8-1.6 μm finishes, while 36 grit variants remove 0.45 lb/min of mild steel.
Market-Leading Manufacturer Comparison
Brand | Price/Unit | Avg. Lifespan | Material Removal Rate |
---|---|---|---|
Brand A | $8.75 | 42 hrs | 0.38 lb/min |
Brand B | $11.20 | 67 hrs | 0.41 lb/min |
Brand C | $9.90 | 58 hrs | 0.39 lb/min |
Custom Configuration Parameters
Specialized operations require tailored solutions:
- Grit Sequencing: Progressive 60-120-220 grit layering
- Hub Modifications: Steel-reinforced nylon cores for 3" wheels
- Composite Materials: Ceramic-doped aluminum oxide blends
Industrial Application Breakdown
Aerospace component finishing demonstrates the 1000 grit flap wheel's capabilities:
- Reduced polishing time per turbine blade: 22 → 14 minutes
- Surface defect rate decrease: 8.7% → 2.1%
- Annual consumable cost savings: $17,500 per workstation
Optimal Usage Protocols
Proper RPM management extends flap wheel service life:
- 3 inch models: Maintain 12,000-14,000 RPM
- Constant pressure: 15-20 lbs/in²
- Cooling intervals: 30 seconds per 5 minutes operation
6 Flap Wheel Technology Roadmap
Emerging smart abrasives integrate wear sensors and thermal indicators, projected to reduce equipment downtime by 38% by 2026. The 6 flap wheel platform continues evolving through:
- AI-optimized grain distribution patterns
- Biodegradable bonding agents
- Instantaneous grit size adaptation systems
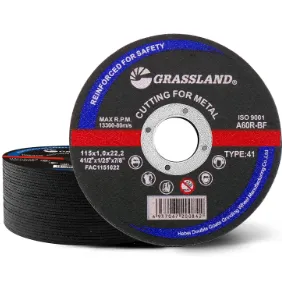
(6 flap wheel)
FAQS on 6 flap wheel
Q: What is a 6 flap wheel used for?
A: A 6 flap wheel is designed for grinding, blending, and finishing surfaces on materials like metal, wood, or plastic. Its multiple flaps provide even abrasion and reduce heat buildup. It’s ideal for curved or contoured surfaces.
Q: When should I use a 1000 grit flap wheel?
A: A 1000 grit flap wheel is best for ultra-fine polishing or finishing tasks on metals or composites. It removes minor imperfections and creates a smooth, near-mirror surface. Avoid using it for heavy material removal.
Q: What applications suit a 36 grit flap wheel?
A: A 36 grit flap wheel is ideal for aggressive stock removal, such as deburring rust, weld seams, or rough edges on metal. Its coarse grit works quickly but leaves a rougher finish. Pair it with finer grits for multi-stage projects.
Q: Is a 3 inch flap wheel compatible with standard drills?
A: Yes, a 3 inch flap wheel typically fits standard drills or angle grinders with a ¼-inch or ⅜-inch arbor. Check your tool’s RPM rating to ensure safe operation. It’s versatile for small-scale or detailed work.
Q: How do I choose between different grits for a 6 flap wheel?
A: Lower grits (e.g., 36) are for rough grinding, while higher grits (e.g., 1000) refine surfaces. Match the grit to your project stage: start coarse, then progress to finer grits. A 3 inch size balances precision and coverage.
Post time:May - 20 - 2025