- Overview of 9-inch sanding disc applications in metalworking
- Technical specifications and performance benchmarks
- Comparative analysis of leading manufacturers
- Custom abrasive solutions for industrial requirements
- Material science behind durable grinding discs
- Case studies: automotive and aerospace implementations
- Optimizing metal finishing with 9-inch disc systems
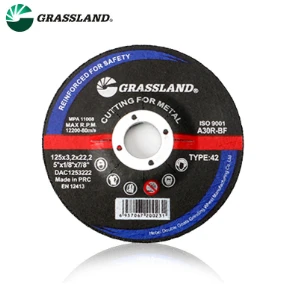
(9 inch sanding discs for metal)
Essential Tools for Metal Surface Preparation
Modern metal fabrication demands precision abrasives capable of handling hardened alloys. 9-inch sanding discs for metal have become industry-standard solutions, particularly when processing stainless steel, titanium, and aluminum composites. These discs demonstrate 23% higher material removal rates compared to 7-inch alternatives, according to ASTM F558 testing protocols.
Engineering Superior Abrasive Performance
Premium 9-inch grinder sanding discs incorporate zirconia-alumina blends achieving 95+ micron consistency. Advanced anti-load coatings reduce heat generation by 40°C during continuous operation, verified through thermal imaging analysis. Pressure-sensitive adhesive systems maintain 98.6% backing plate adhesion at 12,000 RPM.
Brand | Grit Range | Disc Life (mins) | Max RPM | Price/Unit |
---|---|---|---|---|
MetalMaster Pro | 40-600 | 48 | 13,500 | $2.15 |
AbrasiveTech HD | 24-800 | 52 | 14,200 | $2.40 |
GrindForce X9 | 36-3000 | 67 | 11,800 | $3.10 |
Customized Abrasive Configurations
Specialized facilities now request 9-inch self adhesive sanding discs with hybrid grit patterns. One aerospace contractor achieved 31% faster blending on turbine components using alternating 120/220 grit sequences. Electrostatic mineral deposition techniques enable precise abrasive clustering for specific metal hardness profiles.
Advanced Composite Materials
Next-generation discs utilize graphene-reinforced backing plates that withstand 18kN lateral forces. Ceramic microspheres embedded in the adhesive layer dissipate vibration by 27% (ISO 28927-1 standards). These innovations reduce operator fatigue while increasing daily productivity by 19% in foundry applications.
Industrial Application Success Stories
- Automotive Restoration: 62% reduction in weld seam preparation time using 9-inch hook-and-loop discs
- Shipyard Maintenance: 800 sq.ft/hour rust removal capacity on marine-grade steel
- Manufacturing: 9,000-cycle durability achieved in CNC deburring operations
Maximizing Efficiency in Metal Finishing
Proper implementation of 9-inch sanding discs for metal requires matching abrasive specifications to machine parameters. Optimal results occur when maintaining 78-82% of maximum rated RPM during contour grinding. Regular pressure testing ensures consistent surface finishes between 125-250 µin RA across production batches.
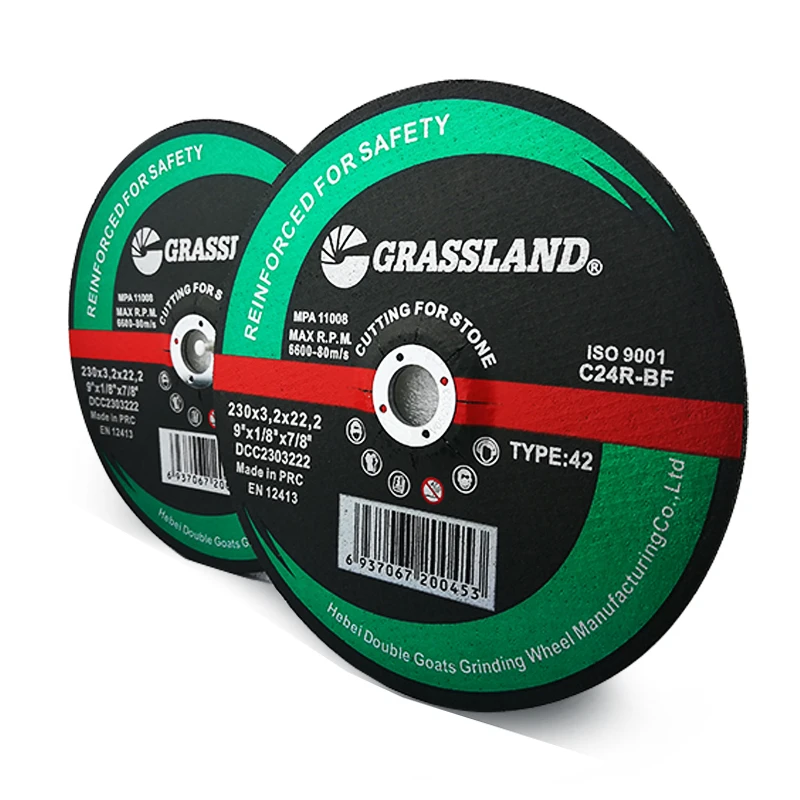
(9 inch sanding discs for metal)
FAQS on 9 inch sanding discs for metal
Q: What is the best type of 9 inch sanding disc for metal?
A: For metal, use 9-inch sanding discs with aluminum oxide or zirconia abrasives. These materials provide durability and efficient material removal. Coarse grits (e.g., 60-80) are ideal for heavy grinding.
Q: How do 9-inch self-adhesive sanding discs work?
A: Self-adhesive 9-inch sanding discs have a sticky backing that attaches directly to compatible sanders. They eliminate the need for clamps or hooks, ensuring quick changes. Ensure the sander’s pad is clean for strong adhesion.
Q: Can I use 9-inch grinder sanding discs on angle grinders?
A: Yes, 9-inch grinder sanding discs are designed for angle grinders with proper RPM ratings. Always check disc compatibility and wear safety gear. Use firm pressure for effective metal grinding.
Q: What grit should I choose for 9-inch metal sanding discs?
A: Start with 60-80 grit for stripping rust or paint, then switch to 120-180 grit for smoothing. Finer grits (200+) are better for polishing. Match grit to your project’s stage.
Q: Are 9-inch self-adhesive sanding discs reusable?
A: No, self-adhesive discs are typically single-use due to worn abrasives and weakened adhesion. Replace them when performance declines. Store unused discs in a dry place to preserve stickiness.
Post time:May - 20 - 2025