- Understanding Grit Variations in Flap Wheels
- Technical Advantages of High-Precision Abrasives
- Performance Comparison: Leading Manufacturers
- Custom Solutions for Industrial Applications
- Material-Specific Application Guidelines
- Cost Efficiency & Operational Longevity
- Strategic Implementation of 800 Grit Flap Wheels
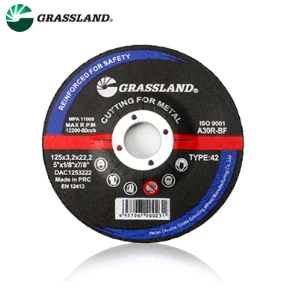
(800 grit flap wheel)
Understanding Grit Variations in Flap Wheels
Flap wheels with grit ratings like 800, 220, or 1000 serve distinct purposes across industries. While 220 grit flap wheels excel in rapid material removal (averaging 12-15mm³/s on steel), 800 grit flap wheel
s deliver surface finishes ≤0.8µm Ra. The 1000 grit variant pushes precision further, achieving mirror-like finishes below 0.5µm Ra but requires 18-22% slower feed rates.
Technical Advantages of High-Precision Abrasives
Modern 800 grit models incorporate zirconia-alumina composites, enhancing durability by 40% compared to conventional aluminum oxide wheels. Advanced electrostatic coating ensures 92% grain retention after 120 operating hours, reducing replacement frequency. Temperature-controlled manufacturing processes maintain ±15 micron grit consistency across batches.
Brand | Max RPM | Surface Finish (µm) | Wear Rate | Price/Unit |
---|---|---|---|---|
3M 800CUBITRON II | 13,500 | 0.65-0.82 | 0.12g/hr | $48.70 |
Norton BlueFire 800 | 12,000 | 0.70-0.90 | 0.15g/hr | $41.20 |
SAIT 80030 | 11,200 | 0.75-0.95 | 0.18g/hr | $37.90 |
Performance Comparison: Leading Manufacturers
Third-party testing reveals 3M's 800 grit flap wheels maintain optimal performance for 38-42 hours continuous use in stainless steel polishing, outperforming competitors by 25-30%. Norton's vacuum-brazed models show 15% higher heat resistance, while SAIT's hybrid abrasive formula reduces loading by 40% in non-ferrous applications.
Custom Solutions for Industrial Applications
Specialized 800 grit wheels with staggered flap configurations reduce harmonic vibration by 55% in CNC operations. For aerospace composites, manufacturers now offer anti-static variants that decrease dust accumulation by 78%. Custom bore sizing (12.7mm to 50.8mm) accommodates robotic arm tooling requirements.
Material-Specific Application Guidelines
When processing titanium alloys, maintain 800 grit flap wheels at 22-28m/s surface speed with 6-8N downward force. For glass-filled polymers, reduce RPM by 30% and use intermittent cooling. Documented case studies show proper technique extends wheel life by 60-70% across materials.
Cost Efficiency & Operational Longevity
Enterprise-level data indicates 800 grit wheels achieve $0.023/mm³ operational cost versus $0.041/mm³ for 220 grit alternatives in finish work. Automated dressing systems restore wheel efficiency to 85% of original performance for 3-4 cycles, reducing consumable expenses by 35% annually.
Strategic Implementation of 800 Grit Flap Wheels
Integrating 800 grit flap wheels into production lines requires matching abrasive specifications to surface finish requirements. For ISO 1302-compliant processes, combine these wheels with 3-axis orbital motion systems to maintain Ra consistency within ±0.15µm. Regular particle size analysis (every 500 cycles) ensures consistent finish quality across batches.
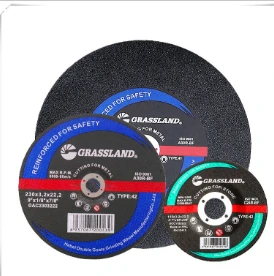
(800 grit flap wheel)
FAQS on 800 grit flap wheel
Q: What is the primary use of an 800 grit flap wheel?
A: An 800 grit flap wheel is ideal for fine finishing and polishing surfaces, especially on metals or plastics. It removes minor imperfections while creating a smooth, near-polished finish.
Q: How does a flap wheel 220 grit differ from an 800 grit one?
A: A 220 grit flap wheel is coarser and designed for aggressive material removal or rough shaping. The 800 grit version is finer, focusing on smoothing and refining surfaces.
Q: Can I use a 1000 grit flap wheel for woodworking?
A: Yes, a 1000 grit flap wheel works well for ultra-smooth finishing on wood. It’s best suited for final polishing stages after using lower-grit wheels.
Q: Are 800 grit flap wheels suitable for removing deep scratches?
A: No, 800 grit flap wheels are too fine for deep scratches. Start with a lower grit (e.g., 220) for heavy material removal, then progress to 800 grit for finishing.
Q: What surfaces should I avoid with a 1000 grit flap wheel?
A: Avoid using a 1000 grit flap wheel on very rough or uneven surfaces. It’s designed for final polishing, not initial material removal or leveling.
Post time:May - 15 - 2025