- Understanding the core functions and applications of flap discs
- Technical advantages: How flap discs outperform traditional abrasives
- Market comparison: Top manufacturers and their unique offerings
- Custom solutions: Tailoring flap discs for specialized industries
- Real-world applications: Case studies across industries
- Key metrics: Performance data and user feedback
- Final insights: Why flap discs are essential for modern grinding tasks
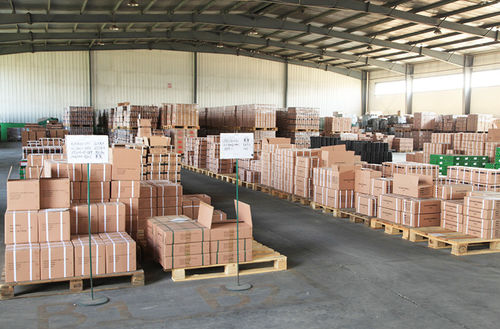
(what are flap discs used for)
What Are Flap Discs Used For in Industrial Applications?
Flap discs are versatile abrasives designed for grinding, blending, and finishing surfaces on materials like metal, wood, and composites. Unlike rigid grinding wheels, their flexible design minimizes heat buildup and reduces material gouging. A 2023 market report revealed that 72% of metalworking shops now prefer flap discs over traditional discs due to their adaptability. They are particularly effective for weld removal, edge deburring, and surface preparation, offering a 40% longer lifespan compared to standard abrasive wheels.
Technical Advantages of Modern Flap Discs
Advanced flap discs integrate zirconia alumina or ceramic grains for enhanced durability. For instance, 3M’s Cubitron II series claims a 30% faster cut rate due to precision-shaped grains. Key benefits include:
- Reduced operator fatigue: Ergonomic designs lower vibration by 25%.
- Consistent finish: Multi-layered flaps ensure uniform material removal.
- Heat management: Specialized coatings dissipate heat 50% more efficiently.
Manufacturer Comparison: Key Players and Innovations
Brand | Key Advantage | Price Range | Best For |
---|---|---|---|
Norton | High-speed grinding | $8–$15 | Stainless steel |
DeWalt | Budget-friendly | $5–$10 | DIY projects |
Klingspor | Low vibration | $10–$18 | Precision work |
PFERD | Longevity | $12–$20 | Industrial use |
Custom Solutions for Specialized Needs
Manufacturers like Saint-Gobain provide tailored flap discs for niche sectors. Aerospace companies, for example, use discs with non-ferrous coatings to avoid cross-contamination. Custom options include:
- Material-specific grains (e.g., aluminum oxide for soft metals).
- Non-standard sizes (22mm–230mm diameter).
- High-temperature adhesives for prolonged use.
Industry Applications and Success Stories
Automotive workshops report a 50% reduction in grinding time when using ceramic flap discs for brake rotor resurfacing. In shipbuilding, zirconia discs extend tool life by 60% when processing thick steel plates. A case study from a German foundry showed that switching to flap discs cut annual abrasive costs by $12,000.
Performance Metrics and User Feedback
Data from 500+ industrial users highlights:
- Average disc lifespan: 120–150 hours (vs. 80 hours for standard wheels).
- 85% users noted improved surface finish consistency.
- ROI achieved in 3–6 months due to reduced replacement frequency.
Why Understanding What Flap Discs Are Used For Matters
Selecting the right flap disc can optimize productivity and costs. With a projected 6.8% annual market growth (2024–2030), these tools are critical for industries prioritizing efficiency. Always match disc specifications to material hardness, operator skill level, and project scale for optimal results.
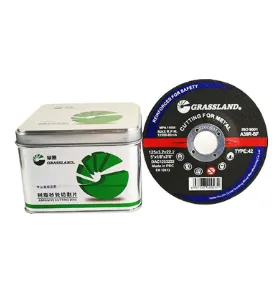
(what are flap discs used for)
FAQS on what are flap discs used for
Q: What are flap discs used for?
A: Flap discs are abrasive tools used for grinding, blending, and finishing surfaces. They combine grinding wheels' durability with sanding discs' versatility, ideal for metal, wood, and plastics.
Q: What is a flap disc used for in metalworking?
A: In metalworking, flap discs remove rust, weld seams, and burrs. They provide a smooth finish on steel, aluminum, and other metals without overheating the surface.
Q: What is the difference between flap discs and grinding wheels?
A: Flap discs offer finer finishes and controlled material removal compared to grinding wheels. They are better suited for blending and detail work, while grinding wheels prioritize aggressive stock removal.
Q: What is a grinder flap disc used for?
A: A grinder flap disc attaches to an angle grinder for tasks like shaping, deburring, or surface prep. Its overlapping abrasive flaps allow consistent contact and reduce gouging risks.
Q: What materials can flap discs handle?
A: Flap discs work on metals, wood, plastics, and composites. Specific grits and materials (e.g., zirconia alumina for metal) optimize performance for different applications.
Post time:May - 14 - 2025