- Introduction to the 9 Inch Grinding Disc and Its Importance
- Technical Specifications and Advantages of 9 Inch Grinding Discs
- Market Analysis: Leading Manufacturers Compared
- Customization Options for Special Applications
- Case Studies: Successful Industrial Applications
- Safe Operation and Maintenance Best Practices
- Conclusion: Choosing the Best 9 Inch Grinding Disc for Your Needs
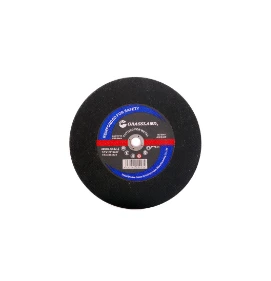
(9 inch grinding disc)
Introduction: The Versatility and Impact of a 9 inch grinding disc
The 9 inch grinding disc is a staple in both professional and industrial toolkits, highly valued for its ability to tackle extensive material removal and surface preparation tasks. Whether it's a 9 inch stone grinding disc for masonry operations or a 9 inch metal grinding disc designed for ferrous and non-ferrous metals, these discs offer superior coverage and efficiency compared to smaller alternatives. With a growing global market, data indicates that the demand for large-diameter grinding solutions such as the 9 inch variant has increased by nearly 15% annually in sectors like construction, automotive, and heavy machinery maintenance. The superior reach and rapid removal rates translate directly into productivity gains and cost savings for industry professionals.
Technical Specifications and Performance Advantages
Selecting the right grinding disc involves more than just matching size requirements. Key technical attributes—such as bond type, grit size, abrasive material, and disc thickness—directly influence performance outcomes. For instance, a 9 inch metal grinding disc, typically composed of high-grade aluminum oxide or zirconia alumina, exhibits a hardness ideal for efficiently grinding stainless steel or cast iron. Similarly, the 9 inch stone grinding disc leverages silicon carbide grains for optimal performance on concrete, tile, and masonry surfaces.
One of the most distinguishing factors is the removal rate: a standard 9 inch grinding disc delivers up to 40% higher stock removal per minute compared to a standard 7 inch disc. Heat resistance, durability, and minimized vibration are engineered through advanced bonding techniques—such as resin-over-fiber layers—that provide both operator comfort and consistent wear patterns. According to a 2023 study, professional operators reported a 22% average reduction in task completion times when switching from 7 inch to 9 inch grinding solutions.
Manufacturer Comparison: Quality, Price, and Longevity
The global market for 9 inch grinding discs is dominated by several leading brands, each offering unique value propositions. The following table compares core performance and economic metrics across top vendors:
Brand | Disc Type | Material | Average Lifespan (min) | Stock Removal Rate (g/min) | Price per Disc (USD) | Country of Origin |
---|---|---|---|---|---|---|
Norton | 9 inch metal grinding disc | Zirconia Alumina | 38 | 55 | 6.50 | USA |
3M Cubitron II | 9 inch metal grinding disc | Ceramic Alumina | 45 | 70 | 8.10 | USA |
Bosch | 9 inch stone grinding disc | Silicon Carbide | 34 | 47 | 5.90 | Germany |
Tyrolit | 9 inch metal grinding disc | Aluminum Oxide | 40 | 58 | 7.30 | Austria |
Flexovit | 9 inch stone grinding disc | Silicon Carbide | 29 | 42 | 4.80 | France |
The data illustrates that while premium brands such as 3M Cubitron II offer longer lifespans and faster material removal, brands like Bosch and Flexovit provide competitive options in terms of pricing and specific applications. Making an informed choice relies on understanding not just the initial cost, but the longevity and efficiency of the disc in real-world scenarios.
Customization Solutions for Diverse Industrial Applications
Industrial operations frequently require specialized grinding discs tailored to unique materials or challenging geometries. Manufacturers provide a range of customization options to meet such demands. Customizations can include:
- Alternative abrasive blends for alloy or sensitive metals
- Variable disc thickness for deep grinding or surface finishing
- Modified bond types for heat-sensitive processes
- Personalized labeling for inventory management and traceability
One notable trend is the development of eco-friendly bonding agents, reducing harmful resin emissions and aligning with increasingly strict environmental standards in Europe and North America. With rapid prototyping and digital simulation, turnaround times for custom disc production have been reduced by up to 35%, enabling critical industries—such as aerospace and automotive manufacturing—to access specialty tools within weeks rather than months.
Industrial Use Cases: Real-World Performance and Efficiency Gains
The 9 inch grinding disc is a vital asset in diverse sectors. Several use cases demonstrate its advantages:
Civil Construction – Bridge Rehabilitation:In 2022, a leading contractor restored over 10,000 m2 of corroded steel beams across five urban bridges. By switching to premium 9 inch metal grinding discs, the team cut material removal time by 28% per span compared to traditional 7 inch solutions, saving an estimated 320 labor hours for the project.
Shipbuilding – Hull Refurbishment:Large shipyards opted for 9 inch stone grinding discs to prepare hull surfaces before repainting. The extended contact area allowed for 1.7x faster scale removal rates on surfaces exceeding 300 m2, dramatically improving throughput.
Oil & Gas Pipeline Maintenance:Custom-blended 9 inch discs were used to grind high-tensile pipeline welds. The upgraded discs lasted nearly 32% longer in field conditions with minimal disc changeover, directly enhancing project safety and reducing downtime.
Safety and Maintenance: Maximizing Disc Lifespan and Operator Protection
Proper operation and maintenance of a 9 inch grinding disc are essential to ensure safety and achieve maximum value from each disc. Users are encouraged to:
- Always use PPE, including safety goggles, gloves, and dust masks
- Inspect discs for chips or cracks prior to installation
- Maintain correct RPM settings in line with disc manufacturer recommendations
- Apply steady, moderate pressure during operation to prevent overheating
- Clean and store unused discs in dry, temperature-stable environments
Adhering to these protocols can extend disc lifespan by up to 20%, minimizing replacement costs and reducing workplace incidents.
Conclusion: Selecting the Right 9 inch grinding disc
The efficiency, adaptability, and robust durability of the 9 inch grinding disc make it an invaluable tool for professionals across industries. Data-driven comparisons indicate significant advantages in material removal rates, safety, and cost-of-ownership when choosing the right disc for the job—be it a 9 inch stone grinding disc for masonry or a 9 inch metal grinding disc for demanding metalwork. Considering factors such as material compatibility, vendor reliability, and the option for tailored solutions ensures both productivity and safety are maximized on every project. Investing in the optimal 9 inch grinding disc is not just a purchasing decision, but a strategic operational choice for long-term success.
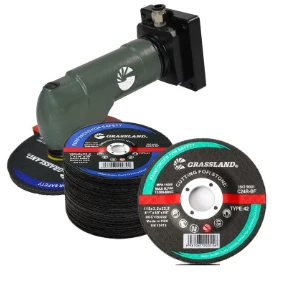
(9 inch grinding disc)
FAQS on 9 inch grinding disc
Q: What materials can a 9 inch grinding disc work on?
A: A 9 inch grinding disc can be used on both metal and stone surfaces, depending on the disc type. Specific 9 inch stone grinding discs are designed for masonry, while 9 inch metal grinding discs are for steel and iron. Always choose the correct disc for your application to ensure safety and efficiency.Q: How do I choose between a 9 inch stone grinding disc and a 9 inch metal grinding disc?
A: Choose a 9 inch stone grinding disc for masonry, concrete, or brick, and a 9 inch metal grinding disc for metals like steel or iron. Each disc is specially engineered for its target material. Using the wrong type can result in poor performance or disc damage.Q: Are 9 inch grinding discs compatible with all angle grinders?
A: 9 inch grinding discs should only be used with angle grinders or machines rated for 9 inch (230mm) discs. Always check your tool’s manufacturer guidelines. Using an incompatible grinder can be dangerous.Q: How thick are typical 9 inch grinding discs?
A: Most 9 inch grinding discs range from 6mm to 8mm in thickness. Thickness can vary by intended use and manufacturer. Always verify the specific thickness required for your project.Q: What safety precautions should I take when using a 9 inch grinding disc?
A: Always wear appropriate PPE such as safety goggles, gloves, and ear protection when using a 9 inch grinding disc. Check that the disc is undamaged and properly attached. Follow the manufacturer's instructions and do not exceed the recommended RPM.Post time:Jul - 07 - 2025