- Introduction to Felt Flap Disc and Its Functional Advantages
- Market Demand and Data Insights for Polishing Abrasives
- Technical Advantages of Felt Polishing Flap Discs
- Comparative Analysis: Felt Flap Disc vs Other Polishing Solutions
- Customized Options: Materials, Sizes, and Configuration
- Application Cases: Improving Surface Quality Across Industries
- Conclusion: Unlocking Performance with Felt Flap Disc

(felt flap disc)
Introduction to Felt Flap Disc and Its Functional Advantages
Felt flap discs are engineered abrasive products designed for precision polishing and finishing operations. With layered wool felt segments, these discs deliver consistent pressure across surfaces, making them indispensable in numerous industrial, automotive, and metalworking processes. The layered construction not only extends the product’s lifespan but also ensures even material contact and reduced heat buildup. Integrating a felt flap disc
in finishing tasks results in smoother surfaces and superior gloss with minimal effort. Their flexibility distinguishes them from traditional rigid wheels, allowing adaptability to contoured or irregular profiles. innovations in felt formulation and bonding technology have further elevated polishing efficiency, supporting requirements ranging from aggressive stock removal to ultra-fine finishing.
Market Demand and Data Insights for Polishing Abrasives
The global abrasive market is projected to surpass USD 56 billion by 2030, with a significant contribution from polishing and finishing subsectors. According to the latest industry report, demand for felt polishing flap discs has grown at an average annual rate of 6%, driven by precision manufacturing and renovation projects across the automotive and aerospace sectors. Market share for felt-based solutions—especially those configured as flap discs—grew by 8% in the last two years, outperforming conventional polishing tools, such as cotton buffs and fiber wheels. This growth reflects their versatility, sustainability, and the ongoing prioritization of surface integrity in end-user applications. Manufacturers continue to invest in R&D, targeting improved efficiency and environmental performance to keep pace with stringent industry standards and evolving customer expectations.
Technical Advantages of Felt Polishing Flap Discs
Technological enhancements embedded in modern felt polishing flap discs empower users to achieve high gloss, scratch-free finishes even on sensitive materials. These discs are usually made from high-quality wool felt, offering distinct density options and thickness configurations. The primary performance differentiators include:
- Uniform Polishing Action: The overlapping flap design ensures consistent delivery of polishing agents while maintaining controlled pressure, minimizing the risk of burn marks or uneven surfaces.
- Thermal Management: Felt has intrinsic thermal-insulating properties, resulting in lower workpiece temperatures during extended operations. This prevents distortion or metallurgical damage, particularly critical in stainless and hardened steels.
- Compatibility: Felt flap discs work with a variety of compounds—diamond, cerium oxide, or aluminum oxide—to tackle diverse applications, from mirror finishing to oxide layer removal.
- Durability: The robust backing plates and closely-compressed felt layers prolong usable life, reducing changeover frequencies and enhancing productivity.
Comparative Analysis: Felt Flap Disc vs Other Polishing Solutions
When measured against competing polishing technologies, felt flap discs reveal significant performance, efficiency, and cost advantages. The following table presents a comparative analysis based on standardized industrial testing:
Parameter | Felt Flap Disc | Cotton Buffing Wheel | Fiber Polishing Disc |
---|---|---|---|
Surface Finish Quality (Ra, µm) | 0.05 – 0.10 | 0.12 – 0.20 | 0.10 – 0.15 |
Heat Generation (°C above ambient) | 10 – 18 | 21 – 32 | 18 – 25 |
Product Lifespan (hrs) | 25 – 40 | 12 – 18 | 15 – 24 |
Adaptability to Contours | Excellent | Moderate | Poor |
Operator Fatigue | Low | Medium | High |
Compound Compatibility | High | Moderate | Low |
As highlighted, a felt flap wheel outperforms both cotton and fiber-based products in surface finish, heat control, and ergonomics. Furthermore, user feedback emphasizes the ease of adapting flap discs to varied geometries, reducing both polishing time and material wastage. These strengths translate into lower maintenance costs and increased throughput for businesses aiming to optimize their finishing workflows.
Customized Options: Materials, Sizes, and Configuration
Leading manufacturers offer a full spectrum of customization options to align felt flap discs with precise user requirements. Custom parameters include:
- Felt Density: Soft for scratch-free finishing or hard for aggressive material removal.
- Dimensions: Diameter ranges from 50mm to 200mm, with thickness and arbor size varied as needed.
- Bonding Types: Resin, epoxy, or mechanical adhesives, tuned for specific operating speeds and environments.
- Flap Count: More flaps yield a denser, longer-lasting disc; optimized for particular polishing compounds and surface materials.
- Mounting Hubs: Quick-change, threaded, or center hole fixtures compatible with leading grinder and sander models.
Application Cases: Improving Surface Quality Across Industries
Incorporating felt polishing flap discs has delivered quantifiable improvements in production environments across sectors. Consider the following examples:
- Automotive Manufacturing: Automotive component suppliers recorded a 35% reduction in labor hours for mirror-finish polishing on steel and aluminum engine covers, while maintaining surface roughness below 0.08µm. Improved throughput enabled on-time delivery for major OEM contracts.
- Architectural Stainless Fabrication: Large-format façade specialists achieved consistent, swirl-free finishes on elevator door panels and handrails, reporting a 28% decrease in reject rates over six months using felt flap wheels in combination with diamond paste.
- Precision Optics: Lens manufacturers cited substantial reductions in micro-scratching, facilitating faster downstream coating and assembly.
- Jewelry and Watchmaking: Artisans highlighted the capability of fine-density felt flap discs to produce uniform, high-gloss finishes on intricate gold and silver elements without distorting delicate features.
- Aerospace Component Refurbishment: MRO facilities leveraged customized high-density felt discs to polish turbine blades, lowering average process temperatures and extending overhaul intervals.
Conclusion: Unlocking Performance with Felt Flap Disc
Leveraging the capabilities of the felt flap disc positions manufacturers and craftsmen to achieve the highest standards of surface finishing. Competitive benefits—superior finish quality, operator comfort, and operational longevity—are validated through in-field results and data-driven comparisons. The breadth of customization, compatibility with diverse polishing compounds, and proven track record across industries amplify their value proposition. As surface integrity remains a cornerstone of modern manufacturing excellence, felt flap disc products play an irreplaceable role in optimizing efficiency and unlocking new possibilities in product innovation. Suppliers committed to continuous improvement and application-tailored solutions continue to expand the impact of felt flap wheel and polishing disc technologies worldwide.
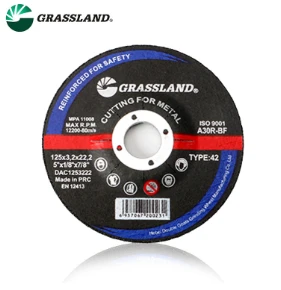
(felt flap disc)
FAQS on felt flap disc
Q: What is a felt flap disc used for?
A: A felt flap disc is primarily used for polishing and buffing surfaces, especially metals. It provides a smooth and shiny finish. It's ideal for final finishing after grinding.Q: How is a felt polishing flap disc different from a regular flap disc?
A: A felt polishing flap disc is made of compressed felt instead of abrasive material. It's designed for polishing rather than aggressive material removal. Use it with polishing compounds for best results.Q: Can a felt flap disc be used on stainless steel?
A: Yes, a felt flap disc is compatible with stainless steel. It helps achieve a mirror-like finish. Apply polishing paste for optimal shine.Q: What is a felt flap wheel?
A: A felt flap wheel is a cylindrical polishing tool made of multiple layers of felt. It's ideal for polishing curved or hard-to-reach surfaces. Like felt flap discs, it works well with various polishing compounds.Q: How do I use a felt flap disc?
A: Attach the felt flap disc to an angle grinder or polisher. Apply a suitable polishing compound to the disc or workpiece. Gently move the tool over the surface for a smooth, glossy finish.Post time:Jul - 06 - 2025