Understanding Abrasive Flap Discs A Comprehensive Overview
Abrasive flap discs are indispensable tools in the industrial realm, particularly in metalworking and woodworking applications. Known for their versatility and effectiveness, these discs are increasingly replacing traditional grinding wheels and other abrasive tools. This article explores the construction, applications, advantages, and maintenance of abrasive flap discs, emphasizing their critical role in enhancing productivity and ensuring quality results.
Construction of Abrasive Flap Discs
Abrasive flap discs are composed of multiple layers of abrasive sheets that are bonded to a backing material. This backing, typically made of fiberglass or plastic, provides structural integrity and support during use. The flaps are arranged in a way that allows for maximum surface contact while ensuring flexibility. The abrasive materials commonly used include aluminum oxide, zirconia alumina, and ceramic, each offering distinct advantages depending on the application.
The flaps are typically angled to allow for efficient grinding, blending, and finishing. This design not only maximizes the surface area in contact with the workpiece but also helps dissipate heat, which can otherwise lead to premature wear of tools and potential damage to the workpiece.
Applications of Abrasive Flap Discs
Abrasive flap discs are highly versatile and can be employed in a multitude of applications
. They are primarily used for1. Grinding and Stock Removal Flap discs are efficient at removing material quickly and are commonly used in industries such as metal fabrication, automotive, and general manufacturing.
2. Blending and Finishing The flexibility of the flaps enables smooth blending of weld seams and surface finishes, making them ideal for achieving a refined look on metal and wood surfaces.
3. Deburring Flap discs excel at removing burrs and sharp edges from machined or cut materials, improving both safety and aesthetics.
4. Sanding In woodworking and metalworking, these discs provide effective sanding capabilities, allowing users to prepare surfaces for painting or other finishing processes.
Advantages of Abrasive Flap Discs
The popularity of abrasive flap discs can be attributed to their numerous advantages over traditional grinding methods
abrasive flap
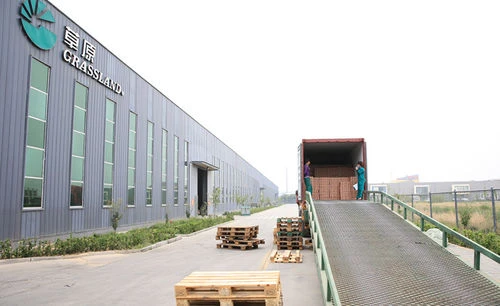
- Extended Life Flap discs generally have a longer lifespan compared to conventional grinding wheels, reducing the frequency of replacement and associated costs.
- Versatility They can be used on a variety of materials, including metals, wood, and plastics, making them a one-stop solution for different grinding, blending, and finishing needs.
- Effective Cooling The design of flap discs allows for better heat dissipation, minimizing the risk of overheating the material and preserving the quality of the workpiece.
- User-Friendly Flap discs are easy to handle and can be used with standard angle grinders, making them accessible to both professionals and DIY enthusiasts.
- Reduced Vibration Due to their flexible nature, flap discs produce less vibration during operation, which enhances user comfort and control.
Maintenance and Best Practices
To maximize the lifespan and performance of abrasive flap discs, proper maintenance and usage practices are essential. Here are some best practices
- Select the Right Disc Choose the appropriate grit and material type based on your specific application. Coarser grits are suitable for grinding, while finer grits are ideal for finishing.
- Use the Correct Speed Always follow the manufacturer’s recommended speed settings for the specific disc used. Exceeding these speeds can lead to premature wear or disc failure.
- Maintain a Consistent Angle When using flap discs, maintain a consistent angle and light pressure against the workpiece to ensure an even finish and avoid damage.
- Inspect Regularly Regularly check flap discs for signs of wear or damage, and replace them as needed to maintain optimal performance.
In conclusion, abrasive flap discs are essential tools that provide significant advantages in various applications. Their unique construction, coupled with their versatile applications and user-friendly nature, makes them a staple in both professional and DIY environments. By understanding their properties and adhering to best practices, users can enhance their productivity and achieve superior results in their projects.
Post time:Dec - 13 - 2024