The Role and Applications of Flap Disks An Overview
Flap disks are an innovative type of abrasive tool that has gained immense popularity in various industries for their efficiency and versatility. They are made up of multiple overlapping flaps of abrasive material, which are attached to a central hub. This unique design allows for better control over the grinding and finishing processes, making flap disks an ideal choice for numerous applications, from metalworking to woodworking and beyond.
Composition and Design
Flap disks generally consist of a backing plate made from durable materials like fiberglass or plastic, onto which multiple layers of abrasive flaps are mounted. These flaps can be made from different types of abrasives, such as aluminum oxide, zirconia, or ceramic, each suited for specific tasks. The angle of the flaps, their density, and the abrasive grit size can all influence the performance of the flap disk, allowing users to select the best combination for their needs.
The design of flap disks provides several advantages they distribute pressure more evenly across the surface of the material being worked on, which results in a smoother finish. Unlike traditional grinding wheels, which can produce heat and cause surface damage or gouging, flap disks operate at lower temperatures, reducing the risk of warping or altering the properties of the workpiece.
Applications of Flap Disks
1. Metalworking One of the primary industries benefiting from flap disks is metalworking. They are frequently used for grinding, blending, and finishing metal surfaces. Flap disks allow for swift removal of material while providing the ability to achieve a fine finish without extensive polishing. Their versatility makes them suitable for various metals, including stainless steel, aluminum, and carbon steel.
2. Woodworking In woodworking, flap disks are invaluable for sanding and finishing wood surfaces. They can effectively remove old finishes, smooth rough edges, and shape wood components. Their ability to conform to the workpiece means they can access intricate details and contours, which is often a challenge with other abrasive tools.
3. Automotive and Aerospace The automotive and aerospace industries use flap disks for tasks such as surface preparation, removing coatings, and finishing components. The lightweight design combined with their efficient cutting capabilities allows for less operator fatigue, making them ideal for prolonged use in production environments.
flap disk uses
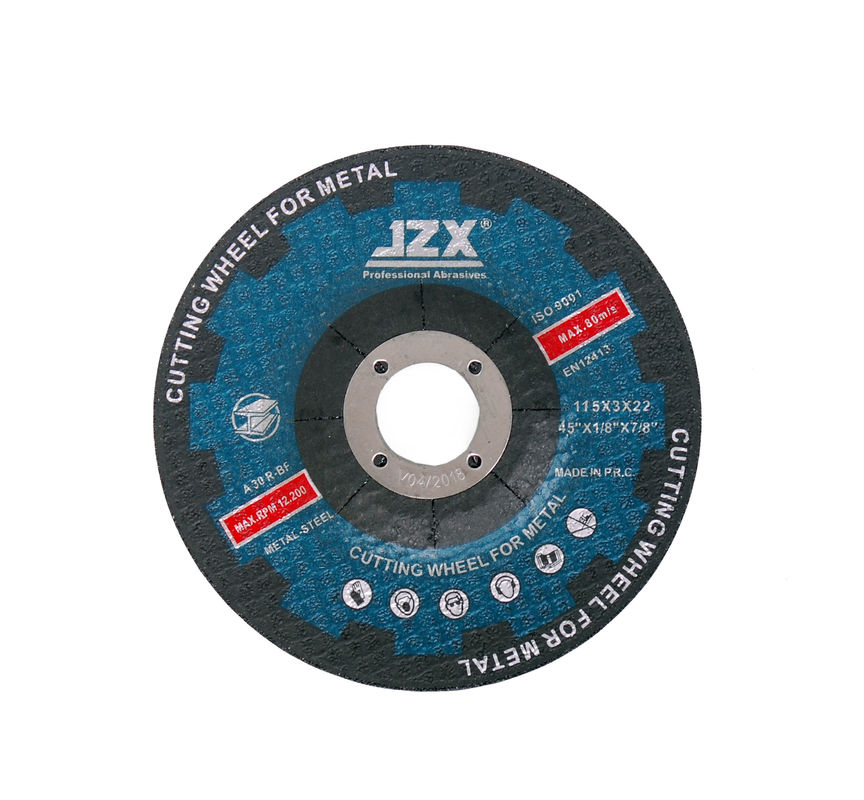
4. Construction and Renovation Flap disks are also prominent in construction and renovation projects, where they help in surface preparation, grinding concrete, and removing rust from metal structures. Their effectiveness in these applications aids in extending the lifespan of built environments by ensuring proper surface preparation before application of protective coatings.
Advantages Over Traditional Abrasives
When compared to traditional sanding discs and grinding wheels, flap disks offer several distinct advantages
- Longer Lifespan Due to their layered design, flap disks tend to last longer than traditional abrasives, providing a better cost-to-performance ratio over time.
- Reduced Loading Flap disks are less prone to loading, meaning they maintain their cutting ability over extended usage, unlike other abrasives that can become clogged with debris.
- Versatility The wide variety of grit sizes and abrasive materials available makes flap disks suitable for a multitude of applications across different industries.
- User-Friendly Flap disks are easier to handle than many traditional tools, making them a favorite among both professional tradespeople and DIY enthusiasts.
Conclusion
In conclusion, flap disks represent a significant advancement in abrasive technology. Their innovative design and versatility make them suitable for a wide range of applications, from metalworking to woodworking and beyond. Their growing popularity across various industries signifies their effectiveness in improving efficiency and enhancing the quality of work produced. As technology continues to evolve, flap disks will likely lead the way in redefining standards in surface preparation and finishing tasks.
Post time:Dec - 13 - 2024