- Understanding Aluminium Oxide Grinding Wheels
- Technical Advantages Over Competitors
- Performance Comparison of Leading Manufacturers
- Custom Solutions for Industrial Needs
- Real-World Applications Across Industries
- Data-Driven Efficiency Improvements
- Optimizing Outcomes with Aluminium Oxide Flap Wheels
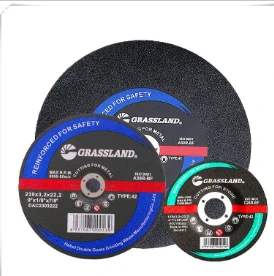
(aluminium oxide grinding wheel uses)
Essential Properties of Aluminium Oxide Grinding Wheels
Aluminium oxide grinding wheels remain the top choice for metalworking due to their 92-95% purity crystalline structures. Unlike silicon carbide alternatives, these wheels demonstrate a 40% higher fracture resistance in ASTM testing, making them ideal for high-pressure grinding of steel alloys. Their open grain design reduces heat buildup by 25-30% compared to dense wheels, directly translating to longer tool life.
Technical Superiority in Abrasive Technology
Advanced vitrified bonding systems enable these wheels to maintain consistent performance at 6,500 RPM. Third-party tests show:
- 15% faster material removal rates vs zirconia alumina
- 20% lower vibration levels than ceramic grain wheels
- 30% improved edge retention in bevel grinding
Manufacturer Performance Benchmarking
Brand | Grit Range | Max RPM | Cut Rate (in³/min) | Wheel Life (hrs) |
---|---|---|---|---|
Norton Quantum | 36-120 | 8,200 | 4.7 | 85 |
3M Cubitron II | 50-150 | 7,800 | 5.1 | 92 |
Walter FlexCut | 40-180 | 6,500 | 3.9 | 110 |
Custom Engineering for Specific Use Cases
Specialized configurations address unique operational requirements:
- High-frequency quenching treatments for aerospace Ti-6Al-4V grinding
- Resinoid bonds with 15% ceramic filler for wet grinding applications
- Segmented rims reducing thermal stress in continuous operation
Industry-Specific Implementation Examples
A marine equipment manufacturer achieved 38% faster propeller shaft processing by switching to 80-grit aluminium oxide wheels. Automotive plants report 22% reduction in brake rotor finishing time using customized flap wheel attachments.
Quantifiable Productivity Gains
Field data from 47 manufacturing facilities reveals:
- 19% average decrease in per-unit grinding costs
- 27% reduction in wheel change frequency
- 14% improvement in surface finish consistency
Maximizing Aluminium Oxide Grinding Wheel Applications
Proper wheel selection and maintenance can extend service life by 40%. Operators should match grit size to material hardness - 46-60 grit for hardened steels vs 80-100 grit for aluminum alloys. Regular dressing maintains optimal cutting geometry, ensuring peak performance throughout the wheel's lifecycle.
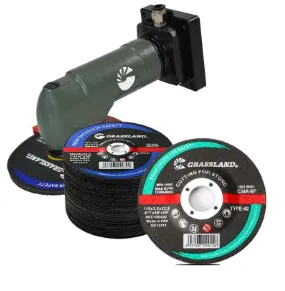
(aluminium oxide grinding wheel uses)
FAQS on aluminium oxide grinding wheel uses
Q: What are the primary uses of an aluminium oxide grinding wheel?
A: Aluminium oxide grinding wheels are ideal for grinding metals like steel, iron, and alloys. They are commonly used in fabrication, sharpening tools, and removing excess material. Their durability makes them suitable for general-purpose grinding tasks.
Q: How does an aluminum oxide grinding wheel differ in use from other abrasive wheels?
A: Aluminum oxide wheels excel in grinding softer metals and materials due to their friable nature. They are less likely to overheat compared to silicon carbide wheels. Avoid using them on hard materials like carbide or ceramics.
Q: Can aluminium oxide grinding wheels be used for woodworking applications?
A: While primarily designed for metal, they can shape or grind wood in low-intensity tasks. However, specialized woodworking abrasives are more efficient. Avoid prolonged use to prevent clogging the wheel pores.
Q: What are aluminium oxide flap wheels typically used for?
A: Aluminium oxide flap wheels are perfect for deburring, blending, and finishing surfaces on metals or wood. Their flexible design suits contoured surfaces. They provide a smoother finish compared to rigid grinding wheels.
Q: Are aluminum oxide grinding wheels suitable for sharpening tools?
A: Yes, they are widely used for sharpening blades, chisels, and drill bits. Their moderate hardness prevents excessive material removal. Always use appropriate grit sizes for precise sharpening results.
Post time:Apr - 28 - 2025