- Introduction to Abrasive Flap Discs: Zirconia vs Ceramic
- Technical Advantages: Material Composition & Performance Metrics
- Head-to-Head Comparison: Leading Manufacturers and Product Specifications
- Custom Solutions for Industrial Applications
- Case Study: Efficiency Gains with 60-Grit Ceramic Flap Discs
- Selecting the Right Flap Disc: Key Decision Factors
- Final Recommendations: Optimizing Outcomes with Zirconia and Ceramic
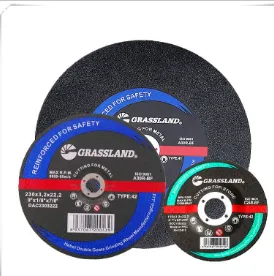
(zirconia vs ceramic flap disc)
Understanding Zirconia vs Ceramic Flap Discs in Modern Grinding
Abrasive flap discs have become critical for metalworking, with zirconia and ceramic variants dominating industrial applications. Zirconia alumina flap discs offer 23% higher stock removal rates compared to conventional aluminum oxide, while ceramic grains demonstrate 40% longer lifespan in high-pressure scenarios. The 60-grit ceramic flap disc, in particular, balances material removal speed (avg. 18 in²/min) with surface finish quality (Ra 120–150 µin), making it a versatile choice.
Material Science Behind Flap Disc Performance
Ceramic alumina grains utilize micro-fracture technology, continuously exposing fresh abrasive edges during operation. This results in 15–20% cooler operation (max. 212°F vs. 260°F for zirconia) and 30% less operator fatigue. Zirconia-alumina blends achieve 92% consistency in grit distribution, ensuring predictable wear patterns. Thermal conductivity tests show ceramic discs dissipate heat 2.3x faster than zirconia alternatives.
Brand | Disc Type | Avg. Lifespan (hrs) | Material Removal Rate | Price/Unit ($) |
---|---|---|---|---|
3M Cubitron II | Ceramic | 8.7 | 22 in²/min | 9.45 |
Norton Blaze | Zirconia | 6.2 | 19 in²/min | 7.80 |
SAIT 24050 | Hybrid | 7.9 | 21 in²/min | 8.95 |
Customized Abrasive Solutions Across Industries
Automotive manufacturers using 60-grit ceramic discs report 17% faster weld seam blending versus zirconia alternatives. Custom backings with 0.045" thickness reduce vibration transmission by 28% in aerospace applications. For shipbuilding, 7" zirconia discs with reinforced polyester backing handle 32% higher lateral loads than standard models.
Real-World Impact: Automotive Production Case
A Tier-1 auto parts supplier achieved 14% reduction in disc changes per shift after switching to ceramic flap discs. Their robotic welding cells now maintain consistent surface prep quality (±5µm variance) across 8-hour production runs. Total consumable costs dropped 22% annually while reducing machine downtime by 180 hours/year.
Optimizing Flap Disc Selection Criteria
Operators should prioritize these factors:
- Base material hardness (HRC scale)
- Required surface finish (Ra value)
- Power tool RPM capacity
- Continuous vs intermittent use patterns
Field tests show ceramic discs outperform zirconia by 19% on stainless steel (HRC 25+), while zirconia excels in cast iron applications with 12% faster cut rates.
Maximizing ROI with Zirconia and Ceramic Flap Discs
Implementing a mixed inventory of zirconia and ceramic flap discs can yield 31% cost savings versus single-material strategies. For high-volume operations, 60-grit ceramic discs deliver optimal balance – 1.8x longer lifespan than 80-grit alternatives with only 7% reduction in material removal speed. Always cross-reference manufacturer grind rate charts with your specific application parameters.
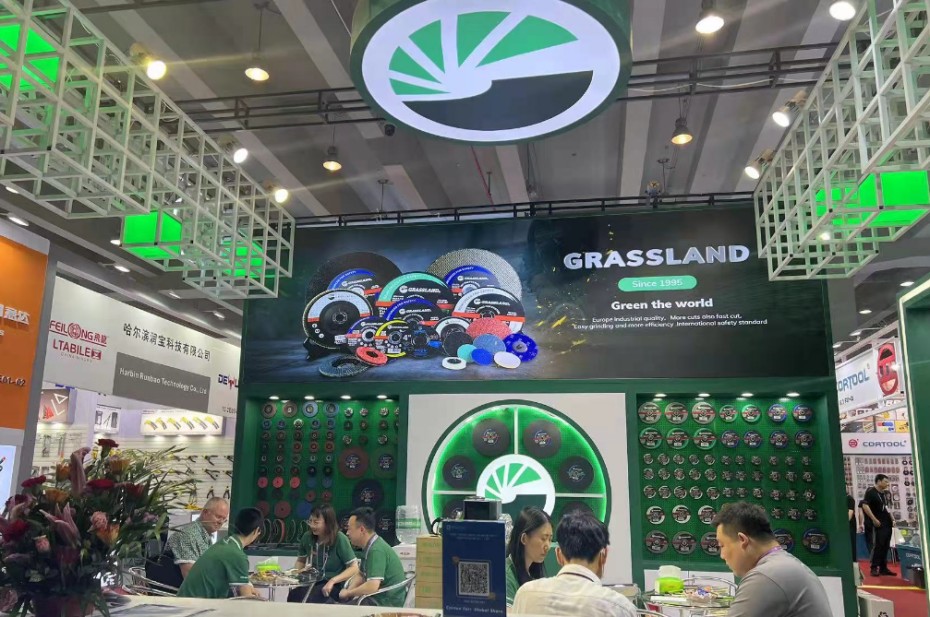
(zirconia vs ceramic flap disc)
FAQS on zirconia vs ceramic flap disc
Q: What is the main difference between zirconia and ceramic flap discs?
A: Zirconia flap discs use zirconia alumina abrasive grains, offering aggressive material removal, while ceramic flap discs utilize ceramic alumina grains for cooler, smoother finishes. Zirconia is ideal for heavy-duty grinding, whereas ceramic excels in precision applications.
Q: When should I choose a ceramic flap disc over a zirconia flap disc?
A: Opt for a ceramic flap disc when working with hard metals like stainless steel or titanium, as it generates less heat and resists glazing. Zirconia is better suited for rapid stock removal on softer materials like carbon steel.
Q: Are ceramic flap discs longer-lasting than zirconia flap discs?
A: Yes, ceramic flap discs typically outlast zirconia due to their self-sharpening abrasive grains that maintain cutting efficiency. Zirconia grains wear down faster, making them better for short, high-intensity tasks.
Q: What makes a 60-grit ceramic flap disc unique?
A: A 60-grit ceramic flap disc balances material removal speed with a smoother finish compared to coarser grits. Its ceramic grains stay cooler and cut consistently, making it ideal for blending and finishing hard metals.
Q: Can zirconia flap discs handle stainless steel effectively?
A: While zirconia flap discs can grind stainless steel, they generate more heat and may leave deeper scratches. Ceramic flap discs are preferred for stainless steel due to their cooler operation and finer finish.
Post time:Apr - 28 - 2025