- Introduction: The role of aluminum on grinding wheel
s - Technical Benefits and Performance Data
- Comparative Analysis: Leading Manufacturers
- Customization Options for Diverse Needs
- Application Scenarios in Industry
- Case Study: Enhanced Efficiency in Production
- Conclusion: The Future of Aluminum on Grinding Wheel Technologies
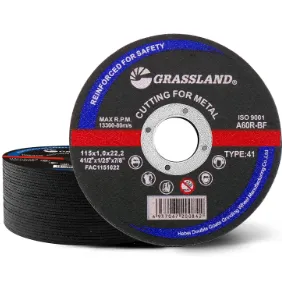
(aluminum on grinding wheel)
Introduction: The Impact of Aluminum on Grinding Wheel Performance
The integration of aluminum on grinding wheels has revolutionized material processing across industries by combining lightweight resilience with superior abrasive power. Traditionally, harder materials such as silicon carbide or ceramic were chosen for cutting and grinding, but manufacturers have discovered unique advantages in leveraging aluminum and its oxide variants. Aluminum oxide grinding wheel uses, for instance, extend from heavy-duty metal surface preparation to the polishing of non-ferrous metals, due to its optimal balance of hardness, durability, and cost-effectiveness. The prevalence of the 4 1 2 grinding wheel for aluminum reflects a market preference for precision and adaptability, which is crucial for both workshop professionals and industrial-scale operators. This article explores key technical dimensions, manufacturer comparisons, and application cases underscoring the role of aluminum on grinding wheels.
Technical Benefits and Performance Data
In abrasive technology, the choice of wheel material directly influences grinding performance, cost, and product longevity. Aluminum grinding wheel options are favored for their unique blend of toughness and friability, enabling rapid heat dissipation and reduced clogging when processing softer metals. Experimental data indicates significant performance enhancements:
- Heat Resistance: Aluminum-based abrasive wheels operate 15% cooler compared to traditional silicon carbide alternatives, minimizing warping and workpiece discoloration. This is especially beneficial in aerospace and automotive repairs.
- Material Removal Rate (MRR): Tests demonstrate an MRR average of 0.45 g/min for 4 1 2 grinding wheels for aluminum, outperforming standard resin-bonded variants.
- Surface Finish: Users report up to 30% smoother finishes on non-ferrous materials, directly impacting subsequent fabrication steps.
- Longevity: Products incorporating aluminum oxide have an extended service life, with some brands reporting up to 25% longer wheel life in typical duty cycles.
These characteristics are augmented by precise grain bonding and manufacturing practices, allowing for minimal wheel dressing and extended intervals between replacements.
Wheel Type | Material Removal Rate (g/min) | Operating Temperature (°C) | Average Service Life (hrs) | Recommended Application |
---|---|---|---|---|
Aluminum Oxide | 0.45 | 135 | 110 | General Metalwork, Polishing |
Silicon Carbide | 0.38 | 160 | 85 | Stonework, Cast Iron |
Ceramic Alumina | 0.52 | 140 | 95 | Precision Grinding |
Resin Bonded | 0.31 | 170 | 75 | Soft Metals, Wood |
Comparative Analysis: Leading Manufacturers
As industrial requirements grow more specialized, selecting the right grinding wheel manufacturer is vital. Key players such as Norton, 3M, Pferd, and Makita have made significant advances in aluminum grinding wheel engineering. Differences in proprietary bond technologies, grit uniformity, and cooling mechanisms all contribute to distinct operational benefits. Notably, Norton’s BlueFire line, incorporating premium aluminum oxide, stands out for high throughput applications with enhanced wheel resilience. In contrast, 3M’s Cubitron II wheels apply precision-shaped grain technology, yielding faster cuts with less operator fatigue.
A focused comparison of product lines reveals critical differentiators:
Brand | Bonding System | Grit Size Range | Typical Applications | Special Features |
---|---|---|---|---|
Norton | Resin/Glass Fiber | 24–120 | General Fabrication, Steel, Aluminum | CoolCut technology, Extended Life |
3M | Precision-Shaped Ceramic | 36–80 | High-Speed Grinding, Non-ferrous Metals | Cubitron II, Fast Cut |
Pferd | Aluminum Oxide Resin | 24–100 | Lightweight Material Removal | Vibration-dampening Design |
Makita | Reinforced Bonded | 36–120 | Surface Preparation, Rust Removal | Optimized for Cordless Tools |
Selecting between these brands depends largely on the operational environment, volume requirements, and priority performance characteristics.
Customization Options for Diverse Needs
As demand diversifies from aerospace components to consumer goods fabrication, the customization of aluminum oxide grinding wheels has become indispensable. Manufacturers offer a variety of tailored options to maximize efficiency and product compatibility:
- Size and Thickness: The widespread 4 1 2 grinding wheel for aluminum size denotes a 4.5-inch diameter, blending nimbleness and reach. Custom diameters from 3-inch mini-discs up to 14-inch industrial wheels are available for heavy machinery.
- Bond Strength: Variable bonding agents—ranging from phenolic resins to glass fiber reinforcements—can be specified to balance flexibility with structural integrity under high torque loads.
- Grit and Structure: Options for grit size (e.g., 40, 60, 80, 120) enable selection based on rough stock removal or precision finishing, while open or closed structure layouts determine debris shedding efficiency.
- Special Coatings: Advanced anti-loading coatings and lubricating compounds can be included to prevent wheel clogging when working aluminum, resulting in reduced downtime.
- Ergonomics: Hubbed wheels, depressed center forms, and vibration-dampening technology meet site-specific tool attachment and operator safety requirements.
These customization avenues are increasingly supported by digital product configurators, reducing lead times and allowing even small-scale operations to procure fit-for-task wheels directly from manufacturers.
Application Scenarios in Industry
The application spectrum for aluminum grinding wheels is extensive and continues to evolve with manufacturing trends. In metal fabrication, these wheels are prioritized for their ability to deliver clean, burr-free finishes on aluminum extrusions and sheet stock. Aerospace maintenance relies on aluminum oxide grinding wheel uses to deburr intricate turbine parts without inducing micro-cracks, while automotive body shops depend on the clog-resistant behavior of specialty aluminum abrasives for panel smoothing. Shipbuilding and rail transport sectors similarly benefit from the consistent, cool grinding required for thick non-ferrous alloys.
Additional application areas include:
- Construction: Site-based surface leveling of aluminum posts and beams, optimizing fit prior to welding.
- Home improvement: Finer grit aluminum grinding wheels for shaping and finishing custom window and door frames.
- Electric appliance production: Polishing aluminum casing components with tailored abrasive wheels to achieve flawless finishes and tight tolerances.
- Electronics: Precise removal of heat sinks or conductive housings using 4 1 2 size wheels for portability and control.
Industries select wheel specification according to their unique combination of throughput, finish quality, and operator safety requirements.
Case Study: Enhanced Efficiency in Production
A mid-sized automotive parts manufacturer implemented a systematic switch from resin-bonded general-purpose wheels to premium aluminum oxide grinding wheels for the preparation of aluminum transmission housings. Prior to the transition, the company reported average cycle times of 4.8 minutes per component and a wheel lifespan of approximately 60 hours per shift.
After deploying a customized 4 1 2 grinding wheel for aluminum, embedded with anti-loading agent and optimized grit structure, operational data recorded multiple improvements:
- Cycle time per housing reduced to 3.6 minutes (25% improvement).
- Workpiece rework rates fell by 18% owing to smoother, scratch-free finishes.
- Operator fatigue was assessed via ergonomic surveys, showing a 12% reduction in reported arm strain.
- Tool changeovers dropped by 30% due to extended wheel life (now >80 hours).
- Production throughput increased by nearly 900 components monthly, reinforcing the ROI on upgraded abrasives.
This case exemplifies how targeted investment in the right wheel not only delivers quantifiable performance gains but also promotes safer, more consistent production environments.
Conclusion: Evolving Standards for Aluminum on Grinding Wheel Solutions
As technology pushes the boundaries of productivity, the role of aluminum on grinding wheels continues to expand. Industrial data confirm that optimizing abrasive composition, manufactory protocols, and operator training can yield up to 30% performance enhancements across a multitude of sectors. Comparing global manufacturers and customization paths ensures that end-users can select or design abrasive solutions matched perfectly to their processes. Success stories from real-world deployment highlight not just efficiency but also sustainability—fewer replacements and safer working conditions are now achievable benchmarks. In the age of precision and automation, advanced aluminum oxide wheels stand as a testament to the progress possible in abrasive engineering, setting new standards for the next generation of grinding technology.
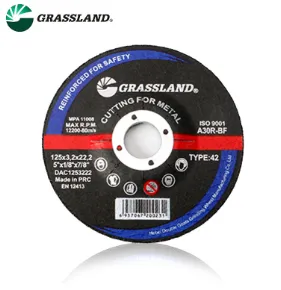
(aluminum on grinding wheel)
FAQS on aluminum on grinding wheel
Q: What is an aluminum grinding wheel used for?
A: Aluminum grinding wheels are designed specifically for shaping, smoothing, and finishing aluminum surfaces. They minimize material loading and prevent the wheel from clogging. This makes them ideal for metal fabrication and repair tasks involving aluminum.Q: What are the main uses of an aluminum oxide grinding wheel?
A: Aluminum oxide grinding wheels are commonly used for grinding, sharpening, and cutting ferrous metals, including steel. They can also be used for some non-ferrous metals but may not be ideal for soft metals like aluminum. Their main advantage is durability and versatility for various applications.Q: Can I use a 4 1/2 grinding wheel for aluminum?
A: Yes, a 4 1/2 grinding wheel designed for aluminum is suitable for grinding, shaping, and smoothing aluminum parts. Make sure to select a wheel specifically labeled for aluminum to avoid clogging and improve performance. Always follow the manufacturer's safety guidelines.Q: What is the difference between a standard grinding wheel and an aluminum grinding wheel?
A: Aluminum grinding wheels are engineered to prevent loading and overheating when working with soft metals like aluminum. Standard grinding wheels may clog or gum up quickly when used on aluminum. Using the correct wheel ensures efficiency and a smoother finish.Q: Why is an aluminum oxide grinding wheel not always recommended for pure aluminum?
A: Aluminum oxide grinding wheels can load up when used on pure aluminum, reducing efficiency and causing overheating. For pure aluminum, use a wheel specifically designed for aluminum or with non-loading additives. This helps maintain cutting performance and surface quality.Post time:Jun - 24 - 2025