- Introduction: The Importance of Grinder Pads for Paint Removal
- Understanding Abrasive Technologies and Technical Advantages
- Evaluating Leading Manufacturers: A Comparative Data Table
- Customization Options for Demanding Applications
- Application Scenarios and Industry Case Studies
- Maintenance and Optimization for Longevity
- Conclusion: Maximizing Efficiency with Grinder Pads for Paint Removal
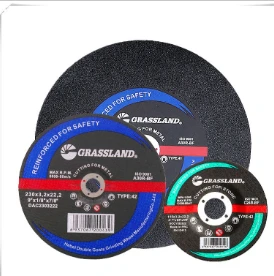
(grinder pads for paint removal)
Introduction: The Importance of Grinder Pads for Paint Removal
The process of removing paint from surfaces in industrial, automotive, and renovation settings relies heavily on the efficiency of abrasive tools, with grinder pads for paint removal
being a pivotal element. Selecting the right pads, such as 9 inch sanding pads or flap disc sanding pads, can be the determining factor between rapid, uniform surface preparation and a sluggish, inconsistent finish. Industry data indicates that over 4.2 million square meters of painted steel surfaces are restored annually in the United States alone, with more than 65% of professionals preferring grinder-based solutions for paint stripping. The performance of the pad directly impacts labor hours, material usage, and surface quality, making the initial selection process critical for both cost efficiency and outcome reliability.
Technical Advances in Abrasive Pad Technology
Modern abrasive technologies have transformed the landscape of paint removal. Early sanding pads utilized basic aluminum oxide grains, but contemporary solutions integrate advanced ceramic abrasives that offer up to 40% greater material removal rates and increased heat resistance.
Technical improvements, such as multi-layered flap constructions and cooling additives in flap disc sanding pads, provide significant advantages:
- Heat Dissipation: Innovative substrates minimize heat buildup, reducing paint smearing and surface warping.
- Durability: Hybrid resin bonding and reinforced fiberglass backings extend pad lifespans by up to 60% compared to standard resin-fiber discs.
- Precision Grading: Uniformity in abrasive grain size ensures smoother, more predictable finishes and limits substrate gouging.
- Dust Management: Many grinder pads now include perforated surfaces for improved dust extraction, which is crucial in environments with strict air quality regulations.
Evaluating Leading Manufacturers: Comparative Data Analysis
Selecting the best abrasive pad involves comparing core metrics across reputable manufacturers. Below is a data-driven comparison of major suppliers in the market for grinder pads for paint removal, focusing on product longevity, removal efficiency, price per unit, and compatibility with industrial equipment:
Brand | Type | Average Lifespan (sq. ft.) | Paint Removal Rate (sq. ft./hr) | Price per Pad (USD) | Heat Resistance | Machine Compatibility |
---|---|---|---|---|---|---|
Norton Blaze | Flap Disc Sanding Pad | 550 | 96 | 8.85 | Up to 475°F | 7"-9" Grinders |
3M Cubitron II | 9 Inch Sanding Pad | 700 | 105 | 11.20 | Up to 500°F | 7"-9" Grinders |
Weiler Tiger | Resin Fiber Disc | 380 | 84 | 7.50 | Up to 400°F | 4.5"-9" Grinders |
Makita Premium | Flap Disc Sanding Pad | 420 | 89 | 6.95 | Up to 450°F | 7"-9" Grinders |
The data shows that 3M Cubitron II pads surpass others in both lifespan and removal rate, though they are priced higher. Norton's Blaze excels in heavy-duty environments with superior durability, while Makita offers budget-friendly, reliable performance for mid-scale operations.
Customization Options for Challenging Paint Removal
Not all paint removal scenarios are identical; substrate type, paint formulation, layer thickness, and contaminant levels can necessitate custom solutions. Manufacturers frequently collaborate with industrial users to tailor:
- Abrasive grain composition: Ceramics, zirconia alumina, or silicon carbide mixes are chosen based on the hardness of the paint and underlying material.
- Pad structure: Varying the density and angle of flaps for flap disc sanding pads to optimize for either aggressive cut or fine smoothing.
- Backing material: Fiberglass versus reinforced plastic or paper for optimal support and flexibility for curved or irregular surfaces.
- Attachment method: Hook-and-loop, quick-change, or direct arbor fitment, depending on the requirements for workflow efficiency.
Industry Applications and Real-World Case Studies
The real-world impact of advanced grinder pads is evident across diverse industries. In one high-profile example, a ship repair company used 9 inch sanding pads to strip over 36,000 square feet of lead-based marine paint in under one week—reducing labor time by 28% versus the previous cycle using standard resin fiber discs. In automotive restoration, specialized flap disc sanding pads have enabled body shops to halve the hours required for complete panel refinishing without introducing scratching or heat damage that complicates repainting.
For municipal infrastructure, concrete barriers coated in anti-graffiti paint have been successfully reconditioned using variable grit grinder pads, restoring surface integrity while maintaining stringent dust and noise controls. Quantitative feedback from these projects demonstrates that premium pads deliver measurable ROI through reduced consumable costs, fewer tool changes, and higher productivity.
Maintenance and Optimization for Lifespan Extension
Even the most advanced abrasive pads require proper care to realize their full potential. Best practices for maximizing pad longevity and sustaining cutting performance include:
- Operating at Correct RPM: Always match grinder speed to pad rating. Over-speeding can degrade bonds and cause premature wear.
- Periodic Cleaning: Use a dressing tool or compressed air to clear embedded paint chips, especially important for porous flap discs.
- Storage: Store pads in a dry, temperature-stable environment to prevent adhesive failure or backing warping.
- Regular Inspection: Check for pad imbalance, cracks, or excessive wear before each use to ensure operator safety and consistent performance.
Conclusion: Maximizing Efficiency with Grinder Pads for Paint Removal
Choosing the right grinder pads for paint removal—whether 9 inch sanding pads for large-scale renovations or flap disc sanding pads for detailed work—not only accelerates project timelines but also ensures superior results and cost savings. Advances in abrasive technology, data-driven manufacturer comparisons, and tailored customization all empower users to achieve peak performance from their grinding workflows. Integrating stringent maintenance routines further extends pad value, benefitting both operators and project budgets. For anyone seeking reliable, efficient paint removal, investing in top-tier grinder pads is an essential step toward optimal surface restoration.
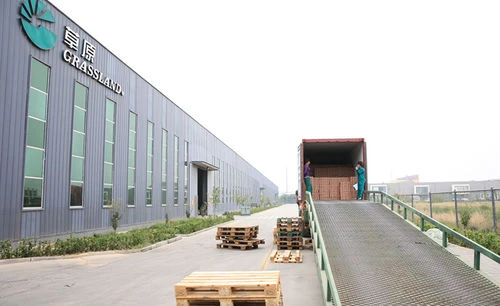
(grinder pads for paint removal)
FAQS on grinder pads for paint removal
Q: What are grinder pads for paint removal used for?
A: Grinder pads for paint removal are designed to efficiently strip paint from metal, wood, or concrete surfaces. They help prepare surfaces for repainting or refinishing. These pads fit standard grinders for fast, effective results.Q: Can I use 9 inch sanding pads on any type of angle grinder?
A: 9 inch sanding pads are compatible with large angle grinders with a corresponding disc size. Always check your grinder’s specifications to ensure proper fit and safe operation. Using the correct size prevents damage and maximizes performance.Q: What’s the difference between flap disc sanding pads and traditional sanding disks?
A: Flap disc sanding pads have overlapping abrasive flaps that provide smoother, more consistent sanding compared to flat disks. They are suitable for blending, shaping, and paint removal. Traditional sanding disks offer a flat surface but may wear out faster.Q: How often should grinder pads for paint removal be replaced?
A: Replace grinder pads when you notice reduced effectiveness or excessive wear. Frequent checks ensure optimal performance and safety. Heavy usage or tough paint may require more frequent pad changes.Q: Are there special precautions when using grinder pads for paint removal?
A: Always wear protective gear like goggles, gloves, and a dust mask when using grinder pads for paint removal. Ensure the work area is well-ventilated to avoid inhaling dust. Follow the manufacturer’s safety instructions for both the pad and the grinder.Post time:Jun - 24 - 2025