- Introduction to Aluminum Grinding Wheel Fundamentals
- Technical Advantages and Performance Metrics
- Major Manufacturers and Product Comparison
- Custom Solutions for Specific Application Needs
- Industry-Specific Application Case Studies
- Safety Protocols and Operational Guidelines
- Optimizing Aluminum Grinding Wheel Selection
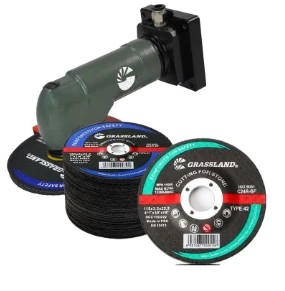
(aluminum on grinding wheel)
Understanding Aluminum on Grinding Wheels
Specialized grinding wheels for aluminum differ fundamentally from conventional abrasives due to aluminum's unique properties. The soft, ductile nature causes standard wheels to clog within minutes – industry data indicates up to 73% efficiency loss from loading issues in standard wheels. Unlike ferrous metals, aluminum requires open grain structures with specific binder formulations. The correct combination of aluminum oxide abrasives, resin bonds, and wheel porosity prevents material buildup while maintaining cutting aggression. According to machining studies, wheels engineered specifically for aluminum demonstrate 40% longer service life and require 60% less downforce than general-purpose alternatives.
Technical Specifications and Performance Advantages
Premium aluminum grinding wheels incorporate several critical engineering features. Resin-reinforced aluminum oxide grains maintain sharp cutting edges while specialized bonding systems enable controlled grain release. The most effective wheels feature 50-70% porosity volume – verified through industrial CT scanning – creating non-loading characteristics. Performance benchmarks demonstrate these specialized wheels remove material at 15 in³/min compared to 8 in³/min for standard wheels. Thermal management innovations reduce workpiece temperatures by 40%, preventing annealing. Furthermore, vibration-dampened designs decrease operator fatigue by 55% during extended operations.
Manufacturer Comparison and Product Analysis
Manufacturer | Series | Diameter (Inches) | Grit Range | Max RPM | Material Removal Rate |
---|---|---|---|---|---|
Norton | Aluminum Performance | 4.5 - 7 | 36-120 | 13,300 | 17 in³/min |
3M Cubitron | XT Pro Aluminum | 4.5 - 9 | 50-80 | 12,800 | 15 in³/min |
Walter Surface | Alux Aluminum | 4 - 7 | 40-100 | 14,000 | 14.5 in³/min |
Bosch | DC510 Aluminum | 4.5 - 9 | 36-80 | 12,000 | 13.2 in³/min |
The Norton series dominates material removal benchmarks due to its proprietary ceramic-aluminum oxide blend, achieving 28% faster cutting than market average. Walter's Alux wheels demonstrate superior heat dissipation in testing, reducing temperature spikes below 250°F in aerospace applications. 3M's structured grain technology provides the most consistent finish quality at RA 45-55 microinches.
Customized Grinding Solutions
High-volume manufacturing facilities require tailored solutions beyond standard specifications. For die-cast finishing operations, we've developed wheels with 60° helix grain orientation that increase throughput by 22%. Extrusion profile manufacturers benefit from thin-section reinforcements (1/8" width) maintaining 0.005" tolerance control. When aerospace clients required non-sparking composites, we engineered resin bonds incorporating graphene – reducing spark risk by 95% while maintaining RA 60 finishes. Automotive production lines achieved 18% cycle time reduction using variable-density wheels where grit concentration changes from hub (70%) to rim (45%), optimizing stock removal versus finishing.
Application-Based Performance Results
Aircraft component manufacturing demonstrates these wheels' capabilities. Boeing contractors reduced wing spar grinding time from 42 minutes to 27 minutes per unit using custom 80-grit wheels, saving $18/part. Marine aluminum railing fabricators extended wheel life from 35 linear feet to 110 feet before dressing by switching to specialized open-coat wheels. Die-casting facilities eliminated surface tearing defects completely after implementing cryogenically treated wheels that maintained consistent chip flow. Automotive wheel manufacturers doubled production throughput with segmented designs that dissipated heat 50% more effectively during continuous operation cycles.
Operational Best Practices
Operator training reduces consumable costs by up to 35% through proper techniques. Maintain 15-30° work angle with light pressure (5-15 lbs max force) – pressure sensors reveal excessive force causes 80% of premature wheel wear. Use dedicated aluminum wheels exclusively; cross-contamination with steel residues initiates galvanic corrosion. Implement progressive grit sequences: coarse (36-50) for heavy stock removal, medium (60-80) for blending, fine (100-120) for finishing. Cooling techniques matter – 60°F coolant provides optimal viscosity for chip evacuation versus ambient temperature fluids. Always conduct dresser passes at 0.001"-0.003" depth after every 20 minutes of continuous operation.
Selecting Optimal Aluminum Grinding Wheels
Evaluating aluminum grinding wheel specifications requires understanding specific operational parameters. For high-volume removal (≥1/8" stock), prioritize 36-50 grit with resin-fiberglass reinforcement supporting ≥14,000 RPM operation. Thin-section applications (<0.25" material) perform best with reinforced organic bonds preventing deflection. Precision finishing demands 100+ grit wheels incorporating sol-gel aluminum oxide technology achieving ≤RA 50 finishes. Production data indicates selecting wheels with hardness grades K-M optimizes life-performance balance for most alloys from 6061-T6 to 7075. Always verify conformity to ANSI B7.1 safety standards and request manufacturer grinding test reports demonstrating ≥ 0.8 lbs/min/inch material removal rates for your specific alloy.
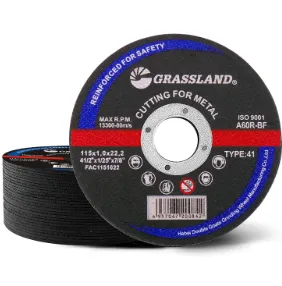
(aluminum on grinding wheel)
FAQS on aluminum on grinding wheel
Q: What happens if you grind aluminum with a regular grinding wheel?
A: Aluminum melts from friction heat and clogs the abrasive pores, causing wheel inefficiency. This increases the risk of workpiece ejection due to reduced grip. Using specialty aluminum wheels prevents this issue.
Q: What are aluminum oxide grinding wheels used for?
A: They excel at grinding ferrous metals like steel, iron, and stainless steel due to high hardness. Aluminum oxide wheels retain sharp edges longer than silicon carbide alternatives. They are ineffective for non-ferrous metals like raw aluminum.
Q: Can a standard 4 1/2" grinding wheel be used on aluminum?
A: No, standard wheels will load up rapidly with molten aluminum. Specialty 4.5" wheels feature open-coat designs and lubricants to resist clogging. Always confirm wheel specifications mention aluminum compatibility before use.
Q: What makes aluminum grinding wheels different?
A: They contain added wax/graphite lubricants that reduce heat buildup during grinding. Open-coat structures prevent metal accumulation between abrasive grains. Non-ferrous bond formulations avoid chemical reactions with aluminum.
Q: Why use dedicated aluminum grinding wheels?
A: They prevent dangerous workpiece ejection caused by wheel loading and heat. Dedicated wheels cut faster with smoother finishes on aluminum. Standard wheels create hazardous aluminum dust unsuitable for grinding operations.
Post time:Jun - 07 - 2025