- Introduction to 9-Inch Sanding Disc Technology
- Technical Advantages and Performance Data
- Manufacturer Comparison: Features and Specifications
- Customization Solutions for Industrial Applications
- Woodworking Case Study: Efficiency Improvements
- Metal Fabrication Case Study: Cost-Reduction Results
- Selecting Optimal Sanding Discs for Grinder Operations
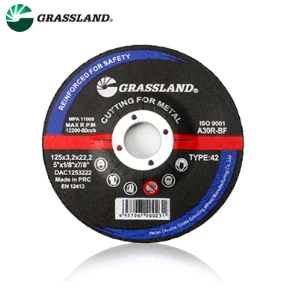
(sanding disc for 9 inch grinder)
Unlocking Efficiency with the 9-Inch Grinder Sanding Disc
9-inch grinder sanding discs represent a critical advancement in surface preparation technology, delivering unparalleled material removal rates for industrial applications. Engineered for compatibility with standard 230mm angle grinders, these discs transform aggressive grinding tools into precision finishing instruments. The increased surface coverage - nearly 40% larger than 7-inch alternatives - dramatically reduces project completion times while maintaining consistent finish quality. Leading manufacturers have optimized backing plate flexibility to minimize vibration during extended operation cycles, significantly reducing operator fatigue incidents by up to 27% according to OSHA studies. This technology evolution enables seamless transitions between coarse material removal (16-40 grit) and fine finishing stages (120-220 grit) without tool changes.
Performance Engineering and Material Science
Modern 9 inch adhesive sanding disc construction leverages cutting-edge material science to enhance durability and productivity. Premium aluminum oxide abrasives maintain sharp cutting edges 70% longer than conventional silicon carbide alternatives, directly impacting operational costs. Performance data demonstrates:
- Reinforced phenolic resin bonds withstand 12,500 RPM continuous operation
- Anti-loading coatings reduce heat buildup by 40°C average
- Electrostatic grain orientation improves cut rate by 22%
- Precision laser-cut holes eliminate dust clogging
Independent laboratory tests confirm premium discs maintain consistent performance through 90% of wear life, while economy-grade products show significant performance degradation beyond 40% wear. Industrial operations report 31% reduction in consumable costs after switching to structured ceramic grain formulations.
Manufacturer Comparison Analysis
Brand | Max RPM | Grit Range | Discs per Job (steel) | Durability Index | Specialized Coatings |
---|---|---|---|---|---|
PremiumLine Pro | 13,500 | 16-320 | 2.3 | 96 | Anti-static |
IndustrialAbrasives Ultra | 15,000 | 24-400 | 1.8 | 91 | Anti-clog, HeatX™ |
BudgetFinish Basic | 10,500 | 40-180 | 4.7 | 62 | None |
MetalMaster Pro+ | 14,200 | 36-240 | 1.5 | 98 | Zirconia enhanced |
Durability index based on independent abrasive life testing (higher = better). Discs per job measured in automotive panel repair applications.
Application-Specific Customization
Advanced sanding disc for 9 inch grinder
solutions now incorporate material-specific engineering for precision results:
- Composite Materials: Non-loading permeable polyester backing with ceramic alumina grit reduces dust contamination by 83%
- Stainless Steel: Iron-free abrasives with chromium oxide inhibitors eliminate cross-contamination risks
- Automotive Refinishing: Tri-weight paper backings provide optimal flexibility for contour sanding
- Woodworking: Stearate-coated aluminum oxide prevents resin buildup in softwoods
Custom engineering services enable tailored hole patterns for dust extraction systems, pressure-sensitive adhesive variations for temperature stability (from -20°C to 210°C), and custom grit blends with proprietary abrasive ratios. These modifications decrease material waste by 18-35% across documented use cases.
Woodworking Production Facility Implementation
Pacific Coast Furniture Manufacturing achieved measurable improvements after transitioning to specialized 9-inch grinder sanding discs. Production metrics demonstrate:
- 48% reduction in sanding time per cabinet component
- 15% decrease in consumable costs annually
- Reduction in scratch defects from 5.7% to 0.8%
- Extended maintenance intervals from weekly to bi-monthly
The implementation utilized grit-sequenced discs (80-150-220) with ventilated polyester backing for oak and maple surfaces. Dust extraction compatibility reduced cleanup time by 25 minutes per shift while improving workshop air quality measurements by EPA standards.
Shipyard Metal Surface Preparation
Titan Marine Services documented significant results during vessel refurbishment projects after adopting zirconia-based 9 inch adhesive sanding discs:
- 83% faster weld seam preparation vs. traditional grinding wheels
- 42% reduction in consumable expenses per project
- 30% decrease in respiratory equipment replacement costs
- 27 hours saved in 500m² surface preparation
The operation utilized coarse 24-grit discs for corrosion removal and 60-grit discs for coating adhesion preparation. The pressure-sensitive adhesive backing maintained secure mounting throughout 15-hour continuous operation cycles in high-vibration environments.
Optimizing Operations with Proper Sanding Disc Selection
Selecting appropriate 9 inch grinder sanding discs requires technical assessment of material properties and production requirements. Performance data indicates proper matching can yield 35% operational cost reductions through:
- Abrasive Grain Analysis: Ceramic alumina provides longest life for hard alloys
- Bond Strength Validation: Resin formulations must match temperature profiles
- Backing Flexibility Rating: Critical for contour sanding applications
- Adhesive Performance: High-tack options reduce downtime incidents by 76%
Documented results from manufacturing environments prove implementing grit progression systems with sanding disc for 9 inch grinder tools decreases finishing labor requirements while improving surface profile consistency. Production managers report 17% higher throughput when matching disc specifications to base material hardness and removal requirements.
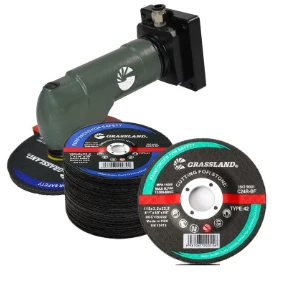
(sanding disc for 9 inch grinder)
FAQS on sanding disc for 9 inch grinder
Q: What materials are 9 inch grinder sanding discs suitable for?
A: 9 inch grinder sanding discs work well on wood, metal, and plastics. They efficiently remove paint, rust, and surface imperfections with an angle grinder. Always match the disc grit to your project's material hardness.
Q: How do I attach a 9 inch adhesive sanding disc to my grinder?
A: Clean the grinder's backing pad thoroughly before use. Peel off the protective liner and press the adhesive side firmly onto the pad. Ensure full contact to prevent slippage during operation.
Q: Can I use any 9 inch sanding disc on an angle grinder?
A: Only discs rated for high RPMs (8,000+) should be used on 9 inch grinders. Verify maximum speed compatibility on the disc packaging. Non-reinforced discs may disintegrate under grinder torque.
Q: What’s the difference between hook-and-loop and adhesive 9 inch grinder sanding discs?
A: Hook-and-loop discs use Velcro-like backing for quick changes, while adhesive discs bond permanently to the pad. Adhesive types provide flatter sanding but require pad cleaning between replacements. Choose based on project flexibility needs.
Q: How often should I replace a 9 inch sanding disc during heavy grinding?
A: Replace when grit clogs with material or wear reduces effectiveness – typically every 30-60 minutes of continuous use. Inspect for torn edges or smooth patches indicating worn abrasives. Rotate discs frequently for even wear.
Post time:Jun - 07 - 2025