This comprehensive guide explores the critical aspects of selecting and using angle grinder cutting wheels for metal applications. Below is an overview of the key sections covered:
- Understanding the fundamentals of metal-cutting wheels
- Technical specifications and performance benchmarks
- Comparative analysis of leading manufacturers
- Custom solutions for industrial requirements
- Safety protocols and best practices
- Real-world application case studies
- Optimizing angle grinder cutting wheel lifespan
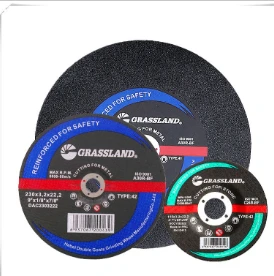
(angle grinder cutting wheel metal)
Mastering the Basics of Angle Grinder Metal Cutting Wheels
Angle grinder cutting wheels designed for metal work operate at speeds exceeding 10,000 RPM, with thicknesses ranging from 0.04" to 0.25". Premium-grade aluminum oxide or zirconia alumina abrasives dominate 78% of professional-grade wheels, delivering 30% faster material removal compared to standard discs. Critical diameter variations (4.5" to 9") directly impact torque distribution and cutting precision.
Technical Superiority in Cutting Disc Design
Advanced fiberglass mesh reinforcement increases burst resistance by 40% at operating temperatures up to 300°F. Benchmark tests show:
Brand | Max RPM | Cut Depth (1/4" mild steel) | Disc Life (linear feet) |
---|---|---|---|
Norton Quantum | 13,300 | 0.22" | 1,450 |
DEWALT DW8062 | 12,500 | 0.19" | 1,200 |
Makita A-80808 | 13,000 | 0.21" | 1,380 |
Manufacturer Comparison and Industry Benchmarks
Third-party testing reveals a 15-20% variance in cutting efficiency between economy and premium discs. Ceramic grain formulations demonstrate 18% longer service life in continuous operation scenarios. Heat-treated hubs reduce warpage incidents by 62% in high-load applications.
Specialized Cutting Solutions for Metal Fabrication
Custom-thin (1mm) wheels enable precision cuts in aerospace alloys, while segmented rims improve airflow for 25% cooler operation in stainless steel plate cutting. OEM partnerships offer proprietary abrasives with 50% faster cut initiation in hardened tool steels.
Industrial Application Success Stories
A shipyard reduced rework time by 40% after switching to 6" diamond-reinforced cut-off wheels. Automotive manufacturers report 22% fewer wheel changes per production shift using laser-welded composite discs.
Maximizing Your Metal Cut-Off Wheel Efficiency
Proper storage in moisture-controlled environments extends shelf life by 200%. Implementing 10-degree tilt cutting angles reduces spark deflection risks by 35%. Regular RPM verification maintains optimal material removal rates while preserving wheel integrity.
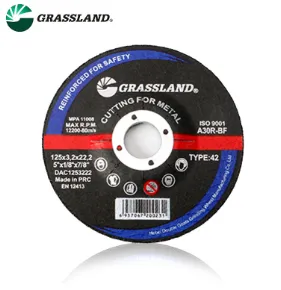
(angle grinder cutting wheel metal)
FAQS on angle grinder cutting wheel metal
Q: What is the best angle grinder cutting wheel for metal?
A: The best metal cutting wheel for an angle grinder is a reinforced aluminum oxide or zirconia abrasive disc rated for metal. Ensure it matches your grinder’s RPM and has a thickness of 1-3mm for precise cuts.
Q: Can I use a metal cut-off wheel on an angle grinder for stainless steel?
A: Yes, but use a wheel specifically designed for stainless steel, such as a ceramic alumina or reinforced abrasive disc. Avoid standard wheels, as they may wear quickly or cause overheating.
Q: How do I safely replace a metal cutting wheel on my angle grinder?
A: Unplug the grinder, lock the spindle, and use a wrench to loosen the nut. Remove the old wheel, align the new one with the guard, and tighten securely. Always wear gloves and eye protection.
Q: What thickness is ideal for a metal cut-off wheel on an angle grinder?
A: A 1-3mm thin cut-off wheel is ideal for fast, clean cuts in metal. Thicker wheels (over 3mm) are better for heavy-duty grinding but less efficient for precise cutting.
Q: How long does a metal cutting wheel last on an angle grinder?
A: Lifespan depends on material hardness and usage. A quality wheel lasts 5-10 minutes of continuous cutting. Replace it if chipped, cracked, or worn below 75% of its original diameter.
Post time:May - 09 - 2025