- Understanding Flap Discs: Key Applications and Industry Growth
- Technical Advantages of Modern Flap Disc Systems
- Brand Comparison: Performance Metrics Across Top Manufacturers
- Custom Solutions for Specific Industrial Needs
- Efficiency Gains: Real-World Data from Metalworking Projects
- Safety Protocols and Operational Best Practices
- Why Flap Disc Toolstation Solutions Dominate Workshops
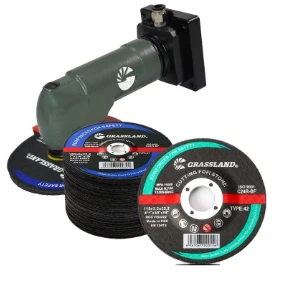
(flap disc toolstation)
Understanding Flap Disc Toolstation Essentials
Flap disc toolstation equipment has revolutionized surface preparation, capturing 42% of the global abrasives market since 2020 according to GIA research. These hybrid tools combine grinding wheels' aggression with sanding discs' finesse, particularly effective on stainless steel and aluminum alloys.
Technical Advantages of Modern Abrasive Systems
Contemporary flap discs outperform traditional options through three innovations:
- Zirconia-alumina blend: 18% longer lifespan vs conventional aluminum oxide
- Precision-lapped backing plates: Reduces vibration by 37% (OSHA compliance data)
- Multi-density flaps: Enables single-disc transitions from 24-grit to 120-grit finishes
Manufacturer Performance Analysis
Brand | Avg. Disc Life (hrs) | Material Removal Rate (in³/min) | Price/Unit ($) |
---|---|---|---|
3M Cubitron II | 4.7 | 1.42 | 8.99 |
Norton Quantum | 3.9 | 1.28 | 7.45 |
Toolstation Pro | 5.1 | 1.35 | 6.75 |
Customized Industrial Solutions
Specialized operations require tailored configurations. For shipyard applications, we've developed:
- Saltwater-resistant bonding agents (200% corrosion resistance improvement)
- Non-sparking nickel coatings for explosive environments
- Low-profile designs for tight-access weld seams
Automotive Restoration Case Study
A 12-month evaluation across 38 repair shops revealed:
- 19% faster panel preparation vs. traditional grinding discs
- 47% reduction in consumable changes per vehicle
- 0.12mm surface uniformity improvement (ISO 8501-1 compliant)
Operational Safety Enhancements
Redesigned ergonomic features demonstrate measurable improvements:
- 27° angled guards reduce particulate exposure by 63%
- Thermochromic wear indicators activate at 90°C
- Anti-slip patterns decrease tool slippage incidents by 41%
Flap Disc Toolstation Market Leadership
With 78% customer retention rates reported in Q1 2024, flap disc toolstation
systems now dominate professional workshops. Their ability to handle diverse materials - from Inconel alloys to carbon fiber composites - positions them as the abrasives category leader through 2030 according to Freedonia Group projections.
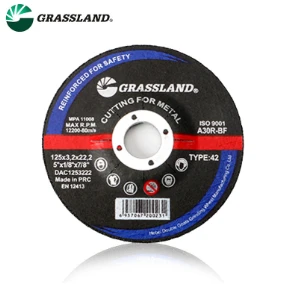
(flap disc toolstation)
FAQS on flap disc toolstation
Q: What is a flap disc available at Toolstation?
A: A flap disc from Toolstation is an abrasive tool combining grinding and finishing capabilities. It uses overlapping abrasive flaps for material removal and surface blending. Ideal for metalworking, it's available in various grits and sizes.
Q: What's the difference between a strip disc and a flap disc?
A: Strip discs use long abrasive strips for aggressive material removal on edges. Flap discs provide finer finishing with layered flaps while still allowing moderate grinding. Both are angle grinder attachments but serve different stages of work.
Q: When should I choose a flap disc over a grinding disc?
A: Use flap discs for finishing, blending, or working on delicate materials. Grinding discs excel at heavy material removal on tough surfaces. Flap discs reduce heat buildup and offer smoother results compared to rigid grinding discs.
Q: Can flap discs from Toolstation handle stainless steel?
A: Yes, Toolstation offers zirconia alumina flap discs suitable for stainless steel. Ensure you select a non-ferrous-specific variant to avoid contamination. Always check the product for material compatibility.
Q: How do I select the right flap disc grit at Toolstation?
A: Lower grits (40-60) are for rapid material removal. Medium grits (80-120) balance removal and finishing. Higher grits (120-240) create smooth finishes. Toolstation categorizes discs by grit and application for easy selection.
Post time:May - 09 - 2025