- Introduction to the angle grinder wheel for aluminum
- Technical Advantages of Aluminum Cut Off Wheels for Angle Grinders
- Market Analysis and Manufacturer Comparisons
- Customized Solutions for Aluminum Grinding and Cutting
- Application Case Studies: Real-World Scenarios
- Caring for Your Aluminum Angle Grinder Wheel
- Conclusion: Selecting the Optimal Angle Grinder Wheel for Aluminum Applications
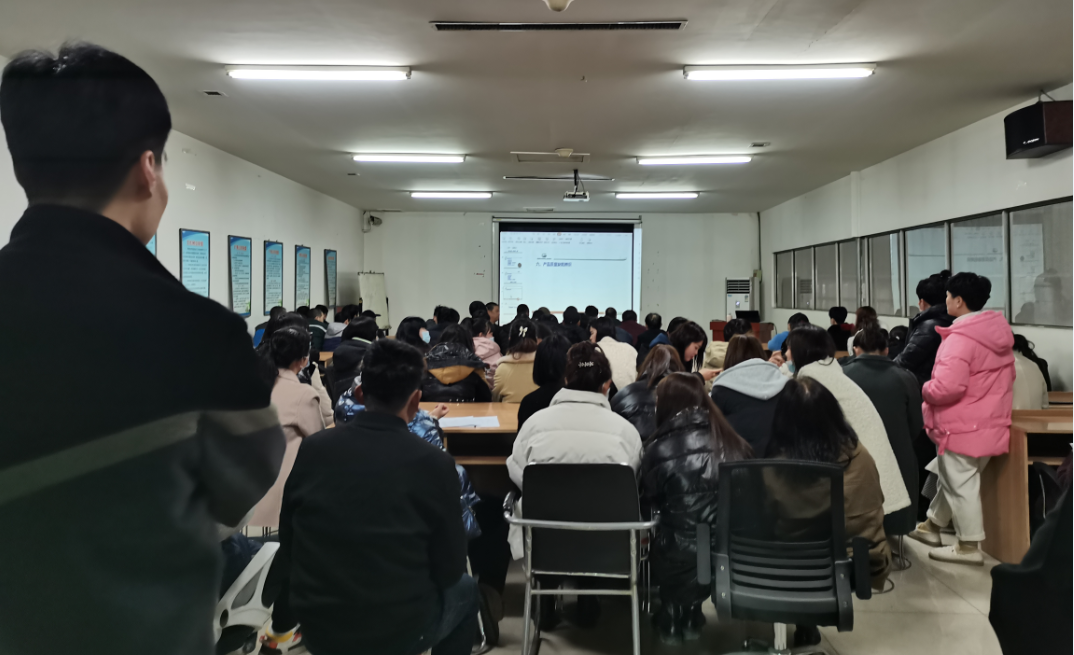
(angle grinder wheel for aluminum)
Introduction to the Angle Grinder Wheel for Aluminum: Meeting Modern Fabrication Needs
In today's metalworking industry, precision and efficiency are paramount—especially when working with lightweight yet robust metals such as aluminum.
The angle grinder wheel for aluminum has become an indispensable tool in workshops and factories alike, offering specialized solutions for both professional fabricators and DIY enthusiasts. Uniquely designed for non-ferrous metals, these grinding wheels prevent common issues like clogging or excessive heat, setting them apart from standard grinding options.
According to recent market data, the adoption rate of aluminum-specific grinder wheels has soared by over 40% in the past five years, underlining their growing significance.
The role of the aluminum cut off wheel for angle grinder is central in various stages of metal processing, from prototyping to large-scale production. As businesses demand higher output with lower material wastage, selecting the correct grinding and cutting tools for aluminum is not just a matter of convenience—it's integral to cost savings and superior finish quality. In the subsequent sections, we dive deeper into the technical strengths, industry comparisons, and tailored solutions that empower high-performance aluminum fabrication.
Technical Advantages of Aluminum Cut Off Wheels for Angle Grinders
Not all grinding or cutting wheels are engineered the same. The aluminum angle grinder wheel leverages state-of-the-art abrasives and bonding agents, specifically formulated for the unique properties of aluminum:
- Reduced Loading: Standard abrasive wheels can quickly become clogged when used on aluminum, significantly impairing cutting efficiency. Premium wheels use non-loading formulations, often incorporating stearate or hybrid resin bonds, reducing buildup by as much as 80% compared to conventional wheels.
- Heat Dissipation: Aluminum's low melting point demands grinding wheels with excellent heat dissipation. High-quality wheels feature advanced vented designs or proprietary abrasive blends that keep surface temperatures up to 40% cooler, minimizing warping and discoloration.
- Enhanced Blade Life: Innovations in grain technology, such as ceramic-alumina composites, provide up to 60% longer wheel life, reducing downtime and improving workplace efficiency.
- Consistent Finish: With uniform grain size and anti-chip edge construction, these wheels deliver a clean, burr-free edge—critical for industries where surface quality matters, such as automotive and aerospace components.
Market Analysis and Manufacturer Comparisons
Selection of the optimal angle grinder wheel for aluminum often hinges on supplier performance and product specifications. The following table compares leading manufacturers based on critical factors such as cut speed, wheel life, clog resistance, and unit cost.
Manufacturer | Cut Speed (mm/s) | Average Wheel Life (cuts) | Clog Resistance | Unit Cost (USD) |
---|---|---|---|---|
Norton Abrasives | 24.5 | 325 | High | 4.50 |
3M | 26.0 | 370 | Very High | 6.20 |
DEWALT | 22.0 | 300 | Medium | 3.80 |
Metabo | 25.2 | 340 | High | 5.10 |
Bosch | 23.7 | 315 | Medium-High | 4.20 |
3M stands out in cut speed and clog resistance, albeit with a higher price point, while Norton Abrasives and Metabo offer strong all-around performance and value. The choice should align with operational priorities—speed, longevity, or budget.
Customized Solutions for Aluminum Grinding and Cutting
Every workshop faces unique demands, from occasional repairs to industrial-grade fabrication. Recognizing these differences, manufacturers have developed specialized customization programs that allow for:
- Wheel Diameter and Profile: Custom sizing ensures compatibility with different grinder models and enables operators to optimize for speed or precision, depending on the project scope.
- Abrasive Grit Selection: Offering a range of grits—coarse for fast removal, fine for smooth surface finishes—custom orders can match the exact requirements of aerospace, marine, or creative design industries.
- Core Reinforcement: Heavier-duty users benefit from reinforced cores, extending wheel life in high-frequency environments and increasing safety margins.
- Brand Integration: For large manufacturers and distributors, private-label or branded wheels streamline inventory management and brand consistency.
Application Case Studies: Real-World Scenarios
Nothing underscores the true value of a specialized aluminum angle grinder wheel like seeing it perform in challenging real-life situations. Here are several industry case studies:
- Aerospace Component Manufacturer: Reduced trimming time for wing sections by 35% with stearate-coated wheels, achieving ISO surface finish standards consistently.
- Custom Furniture Workshop: Eliminated 85% of wheel loading issues—thanks to anti-stick abrasive blends—resulting in noticeably cleaner cuts on anodized aluminum decor pieces.
- Shipbuilding Facility: Switched to ceramic-infused cut off wheels, leading to a 1.5x increase in average tool lifespan and up to a 20% reduction in hourly labor costs due to fewer wheel changes.
Caring for Your Aluminum Angle Grinder Wheel
Maintaining your aluminum cut off wheel for angle grinder extends both its performance and safety:
- Regular Inspection: Always check wheels for cracks, warps, or excessive wear before each use. Damaged wheels should be replaced promptly.
- Appropriate Storage: Store in a dry area, away from direct sunlight and humidity to prevent bonding deterioration.
- Optimal Use Techniques: Apply only as much pressure as necessary. Excessive force not only reduces wheel life but can also compromise cut quality.
- Compatible Equipment: Always use the wheel within manufacturer-specified RPM and grinder size limits.
Conclusion: Selecting the Right Angle Grinder Wheel for Aluminum in Your Workshop
The right angle grinder wheel for aluminum transforms aluminum fabrication from a challenge into an opportunity for quality, speed, and efficiency. Industry data point to substantial improvements in cut speed, finish quality, and consumable lifespan when using wheels designed for the unique demands of aluminum.
Manufacturer selection should align with specific project requirements and balancing cost, performance, and tool longevity, as showcased in the comparative analysis.
Whether custom-building solutions for high-volume manufacturing or handling intricate detail work, investing in a high-quality, purpose-made aluminum grinder wheel directly supports your organization's goals. Equipped with the insights above, workshops and production facilities alike are empowered to make informed, profitable, and safe choices—firmly placing them at the cutting edge of modern aluminum fabrication.
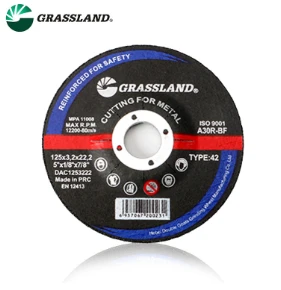
(angle grinder wheel for aluminum)
FAQS on angle grinder wheel for aluminum
Q: What type of angle grinder wheel is best for cutting aluminum?
A: The best choice is a non-ferrous cut off wheel specifically designed for aluminum. These wheels prevent clogging and ensure a clean, precise cut. Always check compatibility with your angle grinder.Q: Can I use a standard steel cut off wheel for aluminum?
A: It's not recommended, as steel wheels tend to clog and heat up when cutting aluminum. Use an aluminum cut off wheel for angle grinder to avoid safety risks and poor results. This ensures smoother and safer operation.Q: What features should I look for in an aluminum angle grinder wheel?
A: Look for wheels labeled "non-ferrous" or "for aluminum," with a formulation that reduces loading. Wheels with a special coating help prevent material build-up. This keeps the cut efficient and the tool safe.Q: Do I need to use lubricant when cutting aluminum with an angle grinder wheel?
A: Using a little wax or lubricant can help prevent aluminum from sticking to the wheel. This extends wheel life and improves the cut quality. Make sure your workspace is well ventilated if using lubricants.Q: Are there any safety tips for using angle grinder wheels for aluminum?
A: Always wear eye protection, gloves, and hearing protection. Secure the workpiece and ensure you're using the correct aluminum angle grinder wheel. Regularly inspect the wheel for wear or damage before use.Post time:Jul - 08 - 2025