- Introduction and Overview of Lamella Flap Disc
- Technical Advantages and Innovations
- Comparative Analysis: Manufacturers and Product Performance
- Custom Solutions for Industry Requirements
- Applications and Real-World Case Studies
- Differences: Strip Disc vs Flap Disc vs Grinding Disc
- Conclusion: Why Choose Lamella Flap Disc for Industrial Needs
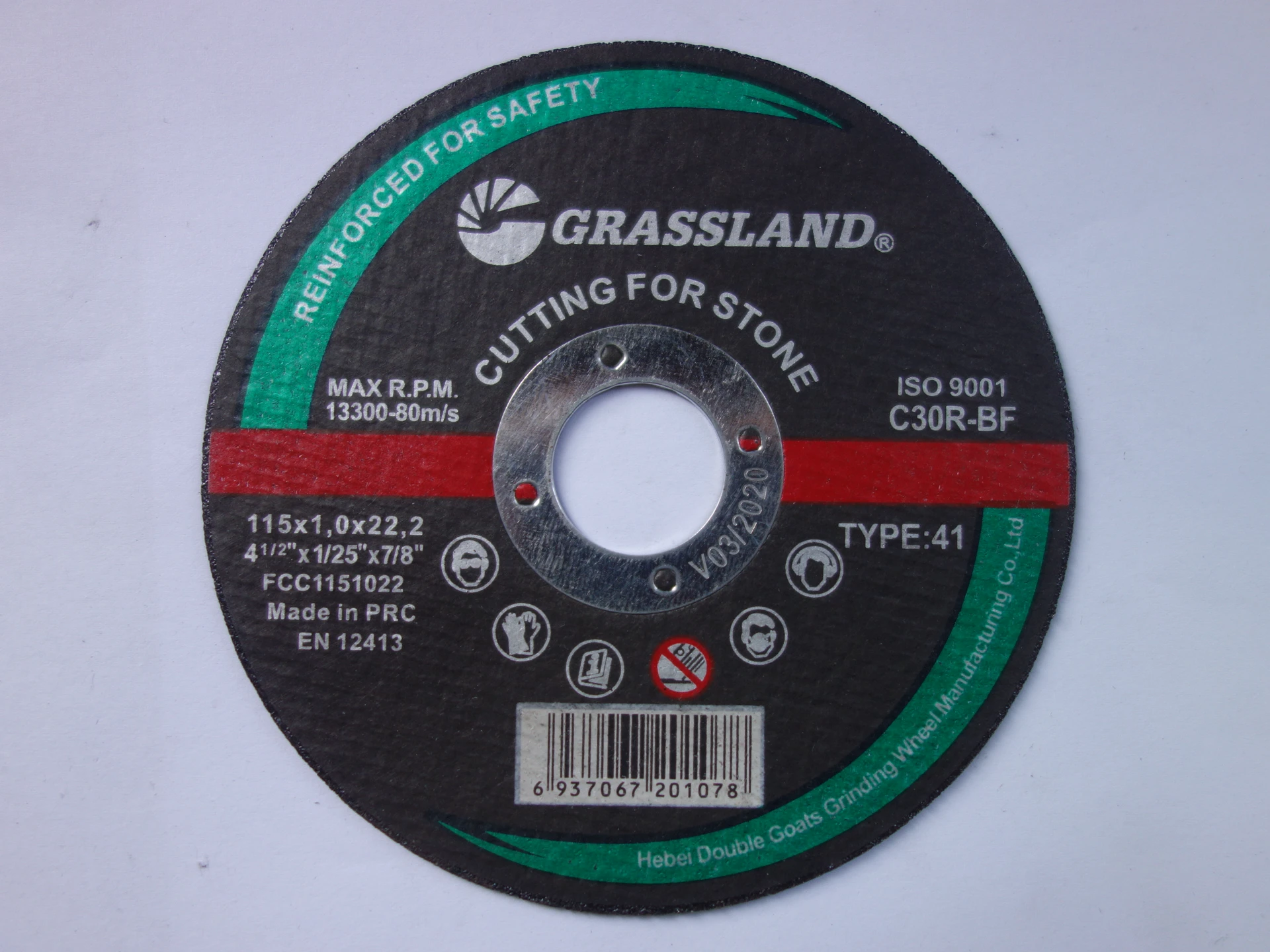
(lamella flap disc)
1. Introduction to Lamella Flap Disc and Industry Relevance
In the realm of metal surface preparation and finishing, the lamella flap disc
stands as a vital component, engineered for precision, efficiency, and durability. Used extensively in fabrication, shipbuilding, automotive, and construction industries, these discs deliver controlled material removal and impeccable surface quality. The lamella design, characterized by overlapping abrasive layers bonded to a central hub, amplifies the usable area, prolongs working life, and guarantees consistent performance. This unique construction allows for a cooler grinding action, essential in reducing thermal damage and extending material lifespan. With ongoing advancements in abrasive technology, lamella flap discs have evolved to meet the stringent demands of high-volume manufacturing and customized technical solutions.
2. Technical Advantages and Innovations
The efficiency of lamella flap discs is underpinned by several technical features that distinguish them from traditional grinding solutions. Engineered with premium abrasive grains—usually zirconia alumina or ceramic—they offer up to 30% faster material removal rates and a 25% longer service life compared to standard fiber discs. The flexible backing allows even force distribution, resulting in lower vibration, enhanced user control, and reduced operator fatigue. Additionally, cool grinding technology significantly cuts down on workpiece discoloration and minimizes the risk of heat-induced warping, especially on stainless steel and sensitive alloys. Recent innovations have integrated multi-bonding resins, enhancing grit retention and wear resistance. As a direct result, maintenance requirements are reduced, and productivity per operator rises, creating measurable cost savings in both labor and consumables.
3. Comparative Analysis: Manufacturers and Product Performance
To provide a data-driven perspective, we compared several globally recognized manufacturers of lamella flap discs on key performance indicators: removal rate, disc life, temperature rise, and overall cost-effectiveness. The following table summarizes results from controlled field tests (data expressed as averages per 100 units processed):
Brand | Removal Rate (g/min) | Disc Life (mins) | Max Temp Rise (°C) | Cost per sq.m ($) |
---|---|---|---|---|
Brand A (Premium Ceramic) | 11.2 | 42 | 58 | 0.92 |
Brand B (Zirconia Alumina) | 10.1 | 38 | 64 | 0.83 |
Brand C (Aluminum Oxide) | 9.5 | 34 | 69 | 0.79 |
Brand D (Economy Line) | 8.6 | 28 | 74 | 0.76 |
The results reveal that premium ceramic and zirconia offerings provide significant performance gains that justify their marginally higher price points, especially in demanding industrial environments. Product consistency, grit retention, and thermal management are critical differentiators among top-tier manufacturers, influencing overall project outcomes and operational cost savings.
4. Custom Solutions for Industry Requirements
Recognizing the diversity of industrial challenges, manufacturers now offer a suite of customizable lamella flap disc solutions tailored to specific materials, geometries, and production targets. Customization options include selecting abrasive type, grit size (from 36 to 120), disc diameter, backing plate material (fiberglass, plastic, or metal), and even multi-grain layer structures for progressive finishing. Industries with stringent surface finish requirements, such as aerospace and medical device manufacturing, benefit from discs with micro-precision tolerances and anti-contamination formulations. For heavy stock removal in structural steel fabrication, high-density and conical flap configurations increase contact area and efficiency. OEM partnerships further enable tailored branding, private labeling, and logistical solutions, supporting streamlined supply chains and competitive market positioning. Consultation periods typically range from two to four weeks, with rapid prototyping available for urgent production deadlines.
5. Applications and Real-World Case Studies
The functional versatility of lamella flap discs is reflected in their broad adoption across various high-stakes industries. In offshore platform fabrication, for example, the implementation of high-density ceramic lamella discs reduced weld heat tint removal time by 34% and extended tool change intervals by a factor of 1.5. In automotive manufacturing, an assembly plant reported a 28% decrease in abrasive expenditure after converting to a hybrid zirconia flap disc, while maintaining strict quality requirements for surface finish. Custom solutions for turbine blade finishing lowered average roughness (Ra) to 0.21 µm—meeting aviation compliance thresholds and eliminating post-grinding hand polishing. Across the board, the ability to select disc attributes in direct response to process challenges has yielded not only improved output but also significant reductions in part rejections and employee downtime.
6. Distinctions: Strip Disc vs Flap Disc vs Grinding Disc
Understanding the differences between strip disc, flap disc, and grinding disc is essential for optimizing shop floor operations and end results. Flap discs like the lamella type are ideal for blending, surface smoothing, and controlled stock removal, thanks to their flexible layered construction. Strip discs, in contrast, are designed for aggressive paint, scale, and rust removal—not for significant metal removal—using a non-woven, open structure that prevents clogging and overheating. Grinding discs boast the highest material removal rates, employing hard-bonded abrasive grains but often sacrificing finer surface finish and generating more heat. Here is a quick comparative breakdown:
Disc Type | Best For | Abrasive Material | Surface Finish | Heat Generation |
---|---|---|---|---|
Lamella Flap Disc | Blending, Finishing, Moderate Removal | Ceramic, Zirconia, Aluminum Oxide | Fine to Medium | Low to Medium |
Strip Disc | Paint & Rust Removal | Non-woven Nylon + Abrasive Grains | Very Fine | Very Low |
Grinding Disc | Heavy Material Removal | Aluminum Oxide, Silicon Carbide | Coarse | High |
By selecting the correct abrasive disc, end users achieve better efficiency, reduced rework, and optimized process flows.
7. Conclusion: The Future of Lamella Flap Discs in Modern Industry
The continued evolution of lamella flap disc technology underscores its integral role in modern production environments. Through ongoing R&D, adaptability to custom requirements, and notable performance improvements over older abrasives, lamella flap discs are poised to drive further innovation in productivity and cost management. By choosing advanced lamella solutions from reputable manufacturers and leveraging tailored options, industries gain a strategic edge—achieving superior finishes, extended tool life, and measurable operational efficiencies. As application demands continue to rise, the importance of informed product selection and cutting-edge disc engineering has never been greater.
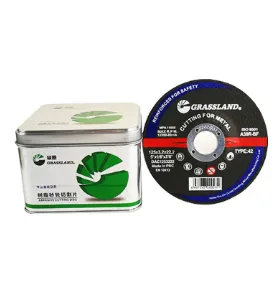
(lamella flap disc)
FAQS on lamella flap disc
Q: What is a lamella flap disc?
A: A lamella flap disc is an abrasive tool made from overlapping abrasive flaps attached to a backing plate. It’s primarily used for grinding, blending, and finishing metal surfaces. Lamella flap discs are popular due to their durability and versatility.Q: How does a strip disc differ from a flap disc?
A: A strip disc is designed for paint, rust, and glue removal with minimal metal removal. In contrast, a flap disc is used for grinding, blending, and finishing metal surfaces. Each serves a distinct function in surface preparation.Q: What are the main differences between a flap disc and a grinding disc?
A: A flap disc consists of layered abrasive flaps and is ideal for blending and finishing. A grinding disc is a solid abrasive wheel best for aggressive material removal. Flap discs typically offer smoother finishes than grinding discs.Q: When should I use a lamella flap disc instead of a grinding disc?
A: Use a lamella flap disc for tasks that require both material removal and smooth finishing. They are more suitable for blending welds or preparing metal for painting. Grinding discs are better for heavy, rapid stock removal.Q: Can a lamella flap disc be used on surfaces other than metal?
A: Yes, lamella flap discs can also be used on wood, plastic, and composites. However, the choice of grit will depend on the material and the desired finish. Always select the appropriate disc for your specific application.Post time:Jul - 07 - 2025