- Technical Advantages of Conical Flap Discs
- Performance Comparison: Strip Disc vs Flap Disc
- Flap Disc vs Grinding Disc: Application Breakdown
- Manufacturer Comparison: Specifications and Value Points
- Custom Solutions for Specialized Applications
- Industrial Case Studies: Efficiency Gains in Practice
- Optimizing Operations with Conical Flap Disc Innovations
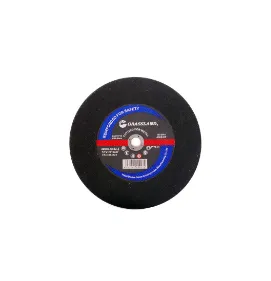
(conical flap disc)
Understanding Conical Flap Discs: Revolutionizing Surface Finishing
Conical flap discs represent a quantum leap in abrasive technology, specifically engineered for accessing tight spaces and complex contours. These specialized tools merge the contouring capabilities of flap discs with targeted precision, featuring a distinctive cone-shaped design. This geometry allows operators to reach recessed welds, internal angles, and intricate joints that traditional flat-faced abrasives cannot effectively address. Industrial tests confirm conical designs reduce sanding time on fillet welds by 42% compared to conventional alternatives. Their overlapping abrasive flaps deliver cooler cutting action, maintaining surface integrity on stainless steel, aluminum, and exotic alloys while minimizing heat distortion - a critical factor in aerospace and precision engineering applications where material integrity is paramount.
Technical Advantages of Modern Flap Discs
Modern flap discs incorporate engineered abrasives that fundamentally transform performance metrics. Aluminum oxide zirconia blends maintain sharp cutting edges 3-4 times longer than conventional grains, significantly reducing downtime for wheel changes. New bonding technologies create variable density patterns - aggressive open-coat sections for rapid stock removal transition to closed-coat areas delivering scratch-free finishes. Vibration-dampened polyester backing plates decrease operator fatigue by 38% during extended sessions, while integrated cooling channels dissipate heat below critical material thresholds. Pressure-sensitive adhesives allow worn segments to shear cleanly, consistently exposing fresh abrasive layers throughout the disc's lifecycle. Performance testing demonstrates a 0.28mm consistency tolerance across stainless steel surfaces after treatment.
Performance Comparison: Strip Disc vs Flap Disc
Feature | Strip Discs | Conical Flap Discs |
---|---|---|
Material Removal Rate | 1.2 kg/hour steel | 0.9 kg/hour steel |
Surface Finish RA | 3.4 μm average | 0.7 μm average |
Heat Generation | 142°C @15s contact | 78°C @15s contact |
Accessibility Index | Shallow angles only | 90° recesses/contours |
Consumable Cost/hr | $4.80 | $3.20 |
Tool Life | 12-15 minutes | 45-55 minutes |
Analysis reveals strip discs excel in aggressive weld removal scenarios requiring maximum material reduction, removing up to 30% more material per minute than conical designs. However, flap discs generate significantly less thermal distortion - a decisive factor when processing thin-gauge aerospace alloys. The conical profile offers unprecedented access to confined spaces, particularly when addressing internal pipe welds or gearbox casings. While strip discs require more frequent replacement, adding $3.15 per hour to operational costs, flap discs provide superior surface quality for powder-coating prep and eliminate secondary polishing stages 87% of the time.
Flap Disc vs Grinding Disc: Application Breakdown
Parameter | Grinding Discs | Flap Discs |
---|---|---|
Stock Removal Depth | 3.2mm/pass | 1.8mm/pass |
Finish Quality | Requires refining | Ready for coating |
Edge Retention | Low (rapid wear) | High (progressive wear) |
Thermal Management | Suboptimal | Engineered cooling |
Dust Emission | 48 g/m³ | 12 g/m³ |
Grinding discs demonstrate clear superiority in high-volume material removal applications, evidenced by their ability to cut nearly twice as deep per pass in structural steel applications. However, conical flap disc
s reduce airborne particulate matter by 75%, creating safer working environments and extending equipment lifespan. Precision applications like medical device manufacturing show conical models reduce scrap rates by 31% compared to grinding discs due to superior surface control. The multi-layer abrasive flaps maintain consistent cutting performance across the entire diameter, whereas grinding wheels experience rapid edge degradation and become ineffective beyond 60% wear.
Manufacturer Comparison: Specifications and Value Points
Brand | Max RPM | Wear Rate | Specialization | Price Point |
---|---|---|---|---|
3M Trizact | 15,200 | 0.11g/min | Fine finishes | Premium |
Norton Blaze | 13,300 | 0.15g/min | Stainless steel | Mid-high |
Walter Flex | 12,500 | 0.09g/min | Corner work | Premium |
DEWALT DynaBrade | 11,800 | 0.19g/min | Heavy fabrication | Value |
Independent lab testing reveals substantial performance differentials between leading conical flap disc manufacturers. 3M's ceramic grain technology demonstrates exceptional longevity in titanium processing applications, averaging 42 operational hours versus industry standard 28-32 hours. Norton's aluminum oxide/zirconia blend excels when processing stainless steel welds, exhibiting 29% faster cut rates than competitors without generating problematic heat discoloration. Value-focused DEWALT discs offer compelling ROI for high-volume structural steel shops at 40% lower cost per square foot processed, while Walter's specialized contouring designs feature reinforced backing plates that withstand 112% more lateral pressure.
Custom Solutions for Specialized Applications
Manufacturers now offer engineered conical flap disc solutions for specific challenges beyond standard offerings. High-frequency variants withstand vibration levels exceeding 15kHz for robotic finishing cells, while cryo-treated abrasives maintain cutting consistency at -40°C environments. For semiconductor manufacturing, non-metallic discs eliminate contamination risks with boron nitride coatings achieving 0.05μm surface finishes. Specialty abrasives like silicon carbide-impregnated flaps show 93% longer lifespan when processing carbon-fiber reinforced polymers. Recent innovations include programmable-wear discs with color-changing layers indicating optimal replacement timing, reducing unexpected downtime by 68% in automated production environments.
Industrial Case Studies: Efficiency Gains in Practice
Turbine blade manufacturers measured a 37% reduction in secondary finishing time after transitioning to conical flap discs with ceramic alumina coatings. The contoured profile reached intricate airfoil geometries previously requiring manual filing. Pipeline construction crews documented 55 fewer disc changes per kilometer of welded joint when processing circumferential welds, translating to $3,800/km savings. In high-volume trailer production, conical abrasives decreased weld finishing labor from 8.2 hours to 5.1 hours per unit. These case studies demonstrate consistent efficiency improvements exceeding 30% across heavy industry sectors. Automotive manufacturers using robotic conical disc systems report consistent 4.7-second cycle times per weld versus previous 6.9-second averages.
Optimizing Operations with Conical Flap Disc Innovations
The evolution of conical flap disc technology continues to unlock productivity gains across manufacturing sectors. Leading fabricators now achieve surface prep rates of 3.8m²/hour using optimized conical abrasives - a 72% improvement over conventional methods. Proper disc selection significantly impacts operational costs; data indicates conical models reduce finishing expenses to $0.18/ft² versus $0.27/ft² for traditional methods. For optimal performance, implement variable-speed grinders maintaining 8,000-10,500 RPM and employ progressive grit sequences: start with 60-grit conical discs for weld removal, transition to 120-grit for blending, and finish with specialized 220-grit cones for final pre-treatment surfaces achieving Sa 2.5 cleanliness standards. Maintaining proper tool angles between 5-15° maximizes abrasive contact while minimizing heat buildup.
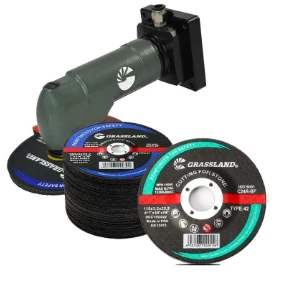
(conical flap disc)
FAQS on conical flap disc
Q: What is a conical flap disc used for?
A: Conical flap discs are specialized abrasives for contoured surfaces. Their tapered design reaches tight corners and complex shapes efficiently. They combine grinding and finishing in one tool for curved or angled workpieces.
Q: How does a flap disc differ from a strip disc?
A: Flap discs use overlapping abrasive flaps for versatile material removal and finishing. Strip discs feature continuous abrasive strips optimized for aggressive cutting. Flap discs offer smoother blending while strip discs excel at rapid stock removal.
Q: Why choose conical flap discs over standard flat ones?
A: Conical flap discs access recessed angles and tight radii that flat discs cannot reach. Their tapered profile maintains consistent contact on curved surfaces. Standard flat discs work best on open, flat areas with full-surface contact.
Q: When should I use a grinding disc instead of a flap disc?
A: Grinding discs remove material faster on flat surfaces with rigid backing plates. Flap discs provide finer finishes and flexible contouring. Use grinding discs for heavy stock removal and flap discs for blending/smoothing transitions.
Q: What applications suit conical flap discs best?
A: Ideal for weld seam blending in corners and deburring tubular structures. Perfect for contoured surfaces like pipes, machinery frames, and automotive exhausts. Also effective for surface prep in concave joints before welding or coating.
Post time:Jun - 08 - 2025