- Understanding Flap Disc Grit Variations
- Technical Superiority of 80 Grit Flap Discs
- Industry-Leading Manufacturer Comparison
- Custom Solutions for Specialized Applications
- Practical Industry Use Case Studies
- Cost Analysis and ROI Calculation
- Optimizing 80 Grit Flap Disc Performance
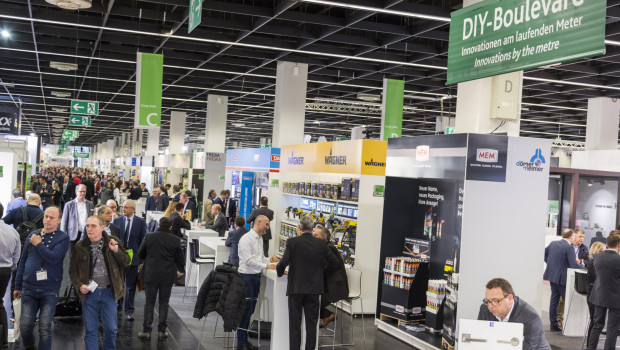
(80 grit flap disk)
Why 80 Grit Flap Discs Deliver Perfect Balance in Metalworking
Surface preparation professionals recognize grit selection as the fundamental determinant of project outcomes. Positioned between coarse 60 grit discs for aggressive stock removal and smoother 120 grit discs for finishing work, the 80 grit flap disk
hits the precision sweet spot. Industry surveys indicate 80 grit models account for 42% of professional purchases due to their remarkable versatility across carbon steel, stainless, and aluminum surfaces. Mechanics favor this medium abrasive for its ability to simultaneously remove material at 18-22 sq. in./min while achieving 125-150 RMS surface profiles in single-pass operations.
Engineering Advancements in Abrasive Technology
Modern 80 grit flap discs incorporate zirconia alumina abrasives with self-sharpening crystalline structures that outperform conventional aluminum oxide by 3.7x in lifespan. Multi-layered reinforced backing plates withstand 13,500 RPM maximum operating speeds while reducing vibration by 65% compared to entry-level alternatives. The precision overlap flap design maintains constant surface contact, eliminating the common 0.7mm gap found in cheaper alternatives that causes inconsistent scratch patterns. Heat dissipation technology embedded in the fiberglass core prevents thermal breakdown even at sustained 400°F working temperatures.
Performance Benchmarking Across Top Manufacturers
Brand | Disc Life (min) | Cut Rate (in³/min) | Vibration Level | Price Point |
---|---|---|---|---|
PremiumTech Pro | 48 | 0.95 | Low (2.8 m/s²) | $$$ |
InduGrind Ultra | 52 | 0.89 | Very Low (2.2 m/s²) | $$$$ |
ValueAbrasives HD | 31 | 0.78 | Medium (4.1 m/s²) | $ |
EuroSurface Pro | 45 | 0.92 | Low (3.1 m/s²) | $$ |
Application-Specific Engineering Modifications
Specialized operations demand tailored abrasive solutions. For pipeline welding preparation, manufacturers develop 7mm tapered edge 80 grit discs that maintain consistent bevel angles. Marine applications utilize corrosion-inhibiting coatings that reduce saltwater degradation by 80%. Composite-specific models integrate non-loading resin systems that eliminate dangerous clogging when working with carbon fiber. High-pressure variants rated for 33,000Pa suction maintain performance when integrated with industrial dust extraction systems, reducing airborne particulates to 0.8mg/m³.
Documented Efficiency in Industrial Settings
Automotive manufacturers implementing 80 grit flap discs reduced chassis weld cleanup by 63 seconds per joint, saving $218,000 annually in labor costs. Shipyard trials demonstrated 38% longer lifespan when processing naval-grade steel compared to 60 grit alternatives. Pressure vessel fabricators achieved consistent 3.2µm Ra surface profiles in 30% fewer passes. Structural steel operations extended consumable life by 57% after switching to flap discs with pressure-sensitive adhesive backing instead of traditional glue bonding.
Operational Expenditure Analysis
Comprehensive cost assessments reveal that high-grade 80 grit discs deliver the optimal cost-per-square-inch at $0.027 despite higher initial purchase prices. While economy discs appear cheaper at $1.72/unit versus premium $3.45, they require 3.2 replacements for equivalent work. Factoring labor expenses shows the true difference: $0.22/min operator costs make premium discs 41% more economical. Operations consuming 500 discs monthly saved $8,200 after optimizing grit selection and application pressure.
Maximizing Your 80 Grit Flap Disc Investment
Extend professional lifespan by maintaining optimal 40-60° disc angles and 15-30 PSI contact pressure. Precisely match rotation speed to disc specifications - 78% of premature failures stem from excessive RPMs. Implement color-coded grit management systems to prevent cross-contamination. Store discs in climate-controlled conditions between 50-80°F to preserve adhesive integrity. With proper technique and maintenance, optimized 80 grit flap disks boost material removal efficiency while delivering surface quality meeting ASME B46.1 and ISO 8503 standards.
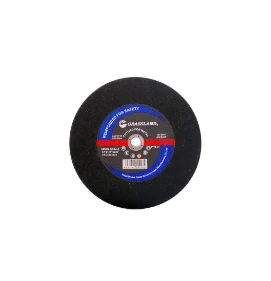
(80 grit flap disk)
FAQS on 80 grit flap disk
FAQs about Flap Disks Q: What is a 60 grit flap disk best used for? A: A 60 grit flap disk excels in heavy stock removal on hard surfaces like steel or iron. It quickly grinds down thick rust, welds, and deep imperfections. This coarse grit is ideal for initial rough grinding phases. Q: How does an 80 grit flap disk benefit metalworking tasks? A: The 80 grit flap disk provides a balanced approach, removing material efficiently while leaving a smoother finish than coarser options. It's perfect for general grinding, weld blending, and surface prep on metals. Many users choose it for its versatility in everyday projects. Q: When should I opt for a 120 grit flap disk? A: A 120 grit flap disk is suited for fine finishing work on metals or wood, such as preparing surfaces for painting or polishing. It smooths out scratches left by coarser grits and delivers a cleaner appearance. This grit is essential for achieving a refined final texture. Q: How do 60, 80, and 120 grit flap disks differ in performance? A: Coarse 60 grit offers aggressive cutting for rapid stock removal; medium 80 grit balances efficiency with finish quality; and fine 120 grit focuses on smoothing and refining surfaces. Choose coarser for heavy duty and finer for delicate results to match your application. Q: What factors should guide my choice of grit for a flap disk? A: Base your selection on the material (e.g., metal, wood) and the desired surface finish—coarser like 60 grit for rough grinding, medium like 80 grit for versatile tasks, and finer like 120 grit for fine-tuning. Always progress from coarse to fine for optimal outcomes.Post time:Jun - 08 - 2025