The Evolution and Importance of Cutting Wheels in the Modern Industry
In the world of manufacturing and construction, cutting wheels play an indispensable role. These specialized tools are fundamental for cutting through various materials, including metals, concrete, and plastics. As industries evolve and demand for precision and efficiency increases, cutting wheels have undergone significant advancements, particularly under the topic of cutting wheel 5.
Understanding Cutting Wheels
Cutting wheels are circular blades designed for grinding, cutting, and finishing materials. Traditionally made from abrasive particles bonded together, these wheels are mounted on electric or pneumatic tools. The performance and durability of a cutting wheel largely depend on its material composition, design, and application. The introduction of cutting wheel 5 exemplifies the latest innovations that address the industry's diverse needs.
Key Features of Cutting Wheel 5
Cutting wheel 5 is characterized by several enhanced features that set it apart from its predecessors. Among its most significant improvements is the use of advanced materials, such as high-performance ceramics and polycrystalline diamond (PCD). These materials boast greater durability and longevity, which ultimately leads to cost savings for manufacturers and builders alike.
Another notable aspect of cutting wheel 5 is its engineered thickness and diameter options. The design allows for optimized cutting efficiency, reducing the time and effort needed for various tasks. This feature is especially beneficial for industries requiring intricate cuts, such as automotive design and aerospace engineering.
Applications Across Industries
cutting wheel 5
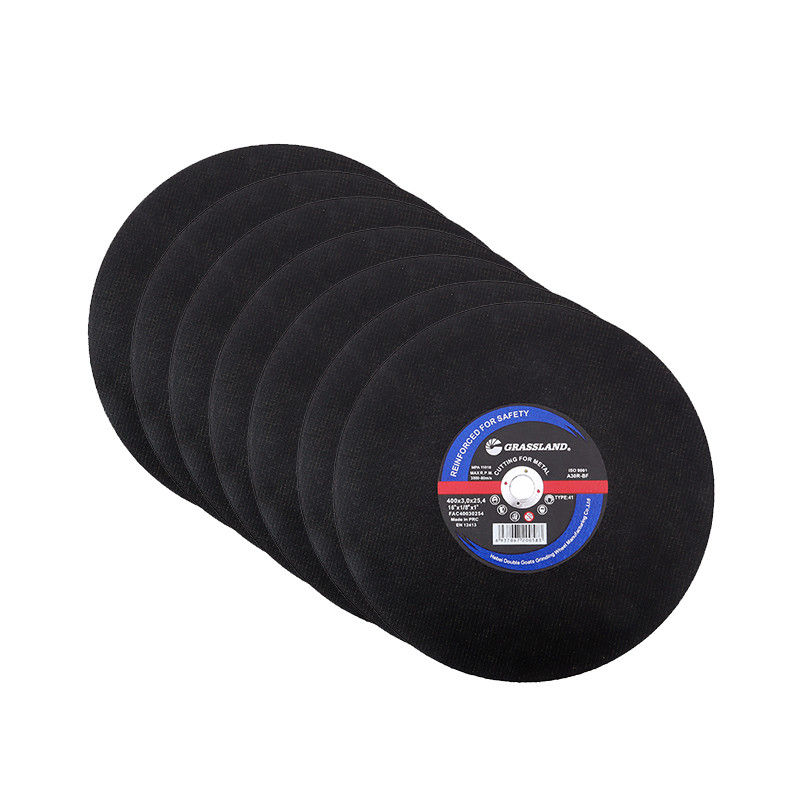
The versatility of cutting wheel 5 makes it suitable for a wide range of applications. In construction, cutting wheels are essential for cutting steel rebar, concrete slabs, and masonry. The speed and efficiency offered by cutting wheel 5 help contractors meet tight deadlines without sacrificing quality.
In the metalworking industry, these wheels are crucial for fabricating components and finishing surfaces. The precision cutting ability ensures minimum material waste, promoting sustainability—a vital aspect in today’s manufacturing processes. Moreover, the performance of cutting wheel 5 contributes to smoother finishes, reducing the need for additional polishing or grinding.
Safety and Handling
With the advancements in cutting wheel technology also comes an increased responsibility regarding safety. Cutting operations can pose risks, including accidents from wheel breakage or operator injuries. Therefore, cutting wheel 5 often includes additional safety features, such as reinforced edges and vibration reduction technology. These enhancements not only protect the operator but also extend the lifespan of the wheel itself.
To further promote safe handling, manufacturers provide extensive training and guidelines. Understanding the correct usage and maintenance practices is crucial for maximizing the efficacy of cutting wheel 5. Regular inspections and adhering to manufacturer recommendations can significantly reduce the risk of accidents.
Conclusion
The introduction of cutting wheel 5 heralds a new era of precision cutting and efficiency across various industries. Its advanced materials, optimized design, and versatility position it as a valuable tool for manufacturers and contractors alike. As technology continues to evolve, the cutting wheel will undoubtedly play a central role in shaping the future of manufacturing, paving the way for faster production rates and increased safety standards. Embracing these innovations is essential for any professional aiming to succeed in today's competitive landscape.
Post time:Dec - 05 - 2024