Understanding Grinding Flap Discs A Comprehensive Overview
Grinding flap discs are essential tools in the world of metalworking and fabrication. They are widely used for various applications, including grinding, blending, and finishing surfaces. This article covers the fundamentals of grinding flap discs, their construction, applications, benefits, and tips for effective use.
What Are Grinding Flap Discs?
Grinding flap discs consist of overlapping pieces of abrasive material, or flaps, adhered to a backing plate. The flaps are typically made from materials such as aluminum oxide, zirconia, or ceramic, which provide different levels of aggressiveness and durability depending on the application. The backing plate can be either fiberglass or plastic, which adds stability and support to the disc.
These discs come in various shapes and sizes, typically with a conical or flat design. The choice of shape and size depends on the specific requirements of the job, such as the type of material being worked on and the desired finish.
Applications of Grinding Flap Discs
Grinding flap discs are incredibly versatile and can be used on a variety of materials, including metal, wood, and plastics. Common applications include
1. Metal Fabrication Ideal for smoothing welds, removing rust, and preparing surfaces for painting or coating. They are frequently used in industries like automotive, aerospace, and construction.
2. Woodworking When used on wood surfaces, flap discs can create a smooth finish while effectively removing imperfections and preparing surfaces for staining or sealing.
3. Maintenance and Repair Flap discs are used for maintaining and repairing various equipment. Their versatile nature allows for quick and effective restoration of surfaces.
Benefits of Using Grinding Flap Discs
1. Efficiency Grinding flap discs offer faster material removal rates compared to traditional grinding wheels. Their design allows users to cover more surface area quickly, enhancing productivity.
grinding flap discs
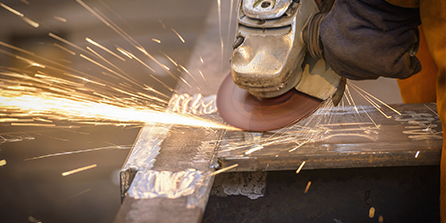
2. Versatility With various grit sizes and materials available, flap discs can be tailored to suit specific needs, whether it’s heavy stock removal or delicate finishing work.
3. Reduced Heat Build-Up The open design of flap discs promotes better airflow, reducing heat build-up during operation. This helps to prevent damage to the workpiece and extends the lifespan of the disc.
4. Improved Control Flap discs provide greater control over the grinding process, allowing for more precise work. Their flexibility accommodates the contours of the workpiece, resulting in a uniform finish.
Tips for Effective Use
To maximize the performance and lifespan of grinding flap discs, consider the following tips
1. Choose the Right Grit Size Select a grit size that corresponds with the job at hand. Coarser grits are suitable for heavy stock removal, while finer grits are best for finishing tasks.
2. Maintain Proper Angle When using a flap disc, maintain a consistent angle against the surface, typically between 15 to 30 degrees. This ensures efficient material removal and prevents excessive wear on the disc.
3. Use Appropriate Pressure Apply light to moderate pressure when grinding. Excessive force can lead to premature wear of the disc and potential damage to the workpiece.
4. Regularly Inspect Discs Check your flap discs frequently for signs of wear or damage. Replacing worn discs ensures consistent performance and prevents potential hazards.
5. Practice Safe Operation Always wear appropriate personal protective equipment (PPE) such as goggles, gloves, and dust masks. Follow the manufacturer's guidelines for safety and operation.
Conclusion
Grinding flap discs are indispensable tools in many industries due to their versatility and efficiency. Understanding their construction, applications, and proper usage techniques can significantly enhance your metalworking skills. By selecting the appropriate flap disc for your specific needs and following best practices, you'll achieve superior results while prolonging the life of your tools. Whether you're a professional fabricator or a hobbyist, integrating flap discs into your toolkit can elevate the quality of your work.
Post time:Dec - 05 - 2024