Understanding the Disc Cutting Process A Comprehensive Guide
The disc cutting process, particularly in manufacturing and engineering contexts, is a crucial technique used for shaping, trimming, and refining materials to achieve desired specifications. Among various methods employed, a specific focus on the “disc de corte 9” provides insight into its applications, advantages, and technical intricacies. This article serves as an informative guide to help readers understand the significance and operational details of this cutting technique.
The Basics of Disc Cutting
Disc cutting involves the use of a circular blade or disc to cut through materials with precision and efficiency. The disc is typically mounted on a machine, such as a lathe or cutting saw, and is driven at high speeds to facilitate cutting. This process is commonly applied to metals, plastics, ceramics, and composites, showcasing versatility across multiple industries, including automotive, aerospace, and construction.
Disc de Corte 9 An Overview
The term “disc de corte 9” pertains to a specific type or size of cutting disc. The “9” likely indicates the diameter of the disc, which can vary depending on the specific application and material to be cut. These discs are usually made from robust materials such as diamond, aluminum oxide, or silicon carbide, designed to withstand the heat and friction generated during cutting operations.
Applications of Disc de Corte 9
1. Industrial Manufacturing In industrial settings, disc de corte 9 is often employed for cutting metal sheets, rods, and pipes. Its ability to offer clean cuts and minimal deformation makes it a preferred choice for fabricators.
2. Repair and Maintenance This cutting disc is also widely used in repair and maintenance tasks. Technicians frequently utilize it to cut through metal components during machinery repairs without compromising the integrity of other nearby parts.
3. Artisan Applications Beyond industrial usage, artisans and hobbyists have discovered the benefits of disc de corte 9 in crafting and woodworking applications, allowing for intricate designs and finishing touches.
Advantages of Using Disc de Corte 9
- Precision Cutting One of the most significant advantages is the precision it offers. The sharpness of the cutting edge ensures that measurements are accurate, which is essential in manufacturing.
disco de corte 9
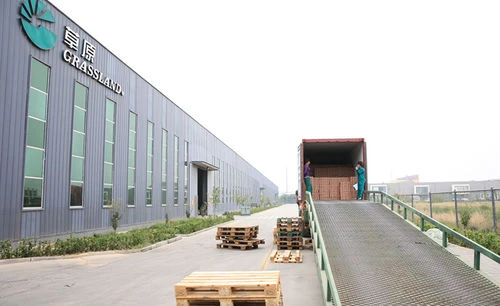
- Durability Cutting discs are designed to be durable, lasting longer than many other cutting tools. This longevity reduces the frequency of replacements, ultimately saving costs in production.
- Versatility The disc can be adapted for various cutting applications, making it suitable for a wide range of materials. This versatility is especially beneficial in environments where diverse cutting tasks are required.
- Safety Features Modern cutting tools, including the disc de corte 9, often come with safety features that minimize risk during operation, making them safer for operators.
Best Practices for Using Disc de Corte 9
To maximize the efficiency and longevity of disc de corte 9, follow these best practices
1. Correct Speed Settings Always use the recommended speed settings based on the material being cut. Adjusting the speed can improve cutting efficiency and prevent overheating.
2. Regular Maintenance Ensuring that the cutting machinery is well-maintained prolongs the life of the disc and enhances cutting performance.
3. Proper Handling Handle the disc with care to avoid damage. When changing or installing discs, always follow the manufacturer's guidelines.
4. Personal Protective Equipment (PPE) Operators should wear appropriate PPE, including gloves, goggles, and masks, to protect against flying debris and other hazards.
Conclusion
The disc de corte 9 plays a pivotal role in modern cutting operations across various industries. Understanding its applications, benefits, and operational guidelines allows manufacturers and technicians to leverage this tool effectively, enhancing both productivity and safety. As technology advances, so too will the design and functionality of such tools, promising an exciting future for the cutting process. Whether you are a seasoned professional or an enthusiast exploring cutting techniques, the insights provided here should serve as a valuable resource in mastering the art of disc cutting.
Post time:Dec - 25 - 2024