The Importance of Flap Disks Enhance Your Metalworking Experience
In the realm of metalworking, the efficiency and quality of finishing processes can significantly influence the overall outcome of a project. One of the essential tools that has gained popularity among metalworkers and fabricators is the flap disk. This versatile abrasive tool is designed to improve grinding, blending, and finishing operations, making it an indispensable part of any professional's toolkit.
What is a Flap Disk?
A flap disk consists of multiple overlapping abrasive flaps attached to a backing material. These flaps are typically made of materials like aluminum oxide, zirconia, or ceramic, chosen based on the specific application needs. The unique design allows them to conform to the surface of the material being worked on, providing a uniform finish while maintaining efficient material removal rates.
Flap disks come in various shapes and sizes, catering to different tasks, from deburring to polishing. They are compatible with angle grinders, making them easy to use in various settings, whether in fabrication shops or on construction sites.
Advantages of Using Flap Disks
1. Versatility Flap disks can be used on a variety of materials, including metals, wood, and plastics. This versatility makes them suitable for diverse applications, ranging from heavy material removal to fine finishing.
2. Efficiency Compared to traditional grinding wheels, flap disks offer a higher removal rate while generating less heat. This efficiency not only speeds up the process but also minimizes the risk of warping or damaging the workpiece due to excessive heat.
flap disk use
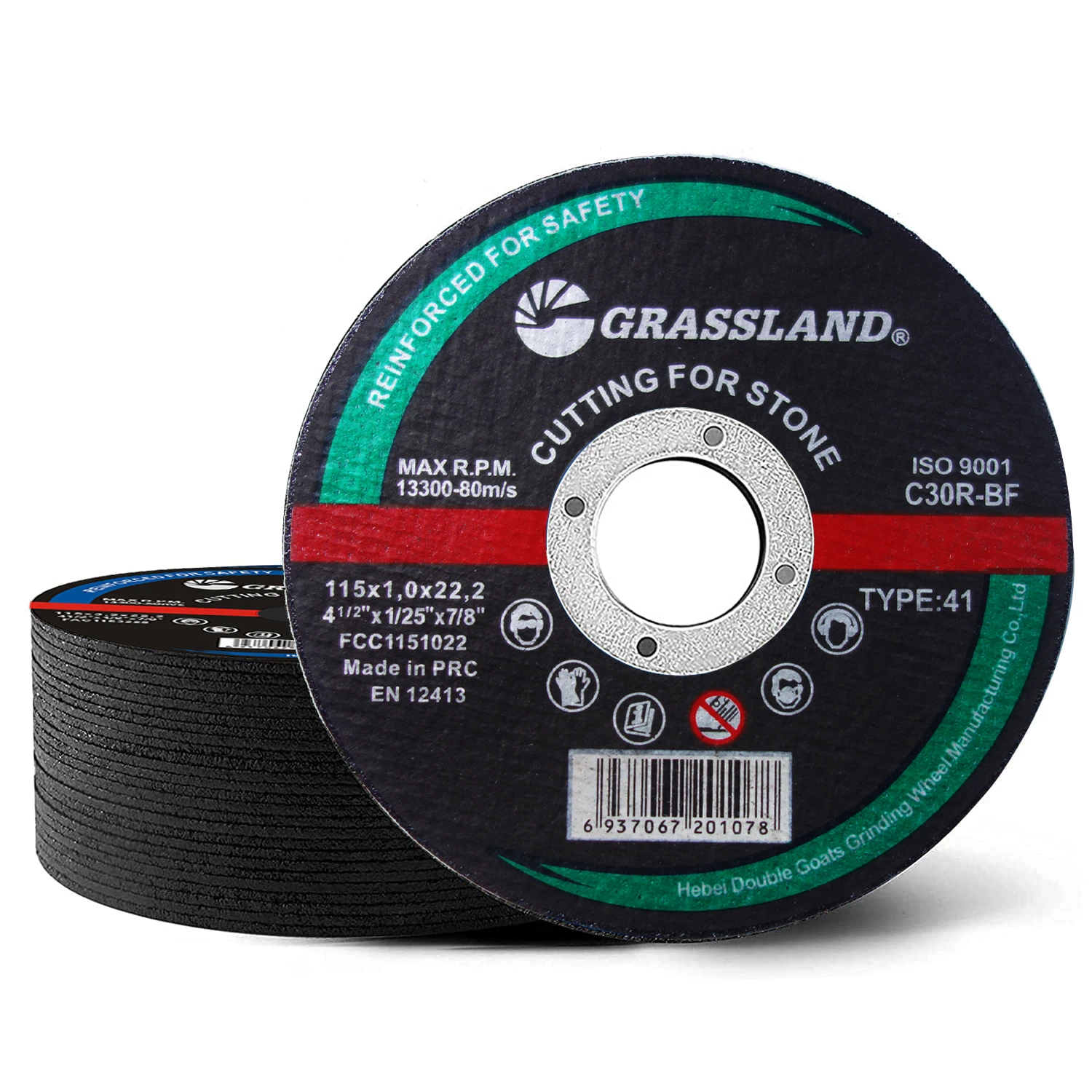
3. Consistent Performance The inherent design of flap disks ensures that they maintain consistent performance throughout their lifespan. As the flaps wear down, new abrasive material is exposed, providing a steady level of aggressiveness and durability.
4. Enhanced Finish Quality The flexibility of the flaps allows for better conformability to the surface of the material being worked on. This adaptability results in smoother finishes compared to conventional disks, reducing the need for additional finishing processes.
5. Safer Operation Flap disks generally produce less vibration and noise than traditional grinding methods, making them safer and more comfortable to use over extended periods. This reduction in stress on the operator can lead to better productivity and quality of work.
Selecting the Right Flap Disk
When choosing flap disks, it is crucial to consider factors such as the type of material being worked on, the desired finish, and the grinder's specifications. Flap disks are available in various grits, from coarse to fine, allowing users to select the most appropriate abrasiveness for their specific tasks.
Additionally, the angle of the flap disk can affect its performance. Disks designed for grinding typically have a flat-face design, while those for finishing and polishing may come with angled flaps, enabling greater flexibility and better adherence to contours.
Conclusion
Flap disks have revolutionized the way metalworkers approach finishing tasks, providing an innovative solution that combines efficiency, versatility, and quality. As the industry continues to evolve, the role of flap disks will likely expand, becoming even more integral to modern metalworking practices. Whether you're a seasoned professional or a DIY enthusiast, incorporating flap disks into your tool arsenal can lead to enhanced productivity and superior results in your projects. Embrace the future of metalworking with flap disks, and experience the difference they can make in your work!
Post time:Dec - 25 - 2024