Understanding the Differences Between Cutting and Grinding Discs
In the realm of manufacturing and metalworking, efficient material removal is crucial for achieving precision and quality in various projects. Among the essential tools for this purpose are cutting discs and grinding discs. Although they may appear similar, they serve different functions and are designed specifically for distinct tasks. Understanding the differences between these two types of discs can significantly enhance your workflow and the quality of your work.
Cutting Discs
Cutting discs, often referred to as cutting wheels or blades, are designed for slicing through materials with minimal effort. Typically, they are thinner and constructed to withstand high rotational speeds. These discs are primarily used in operations where the goal is to cut through hard materials such as metal, stone, or ceramics.
The primary characteristic of cutting discs is their sharp edge, which enables them to make clean and precise cuts. This sharpness is critical because it minimizes heat generation and wear on the disc, prolonging its life. Along with that, cutting discs are generally made from abrasive materials such as aluminum oxide or silicon carbide, depending on the type of material being cut.
When using cutting discs, operators must be aware of the cutting speed and the feed rate to ensure optimal performance. Cutting too quickly can result in overheating, leading to disc failure, while cutting too slowly may cause excessive friction and potential damage to the material being worked on.
Grinding Discs
In contrast, grinding discs are designed for different applications. Their primary function is to grind or shape materials rather than cut through them. These discs are thicker than cutting discs and are designed to remove material by abrasion. Grinding discs are commonly used for surface preparation, smoothing rough edges, and sharpening tools.
These discs also come in various grits, ranging from coarse to fine, which allows users to achieve different finishes depending on their project requirements. The coarse-grit discs are effective for heavy material removal, while fine-grit discs are perfect for polishing and achieving a smoother finish.
disco de corte y desbaste diferencia
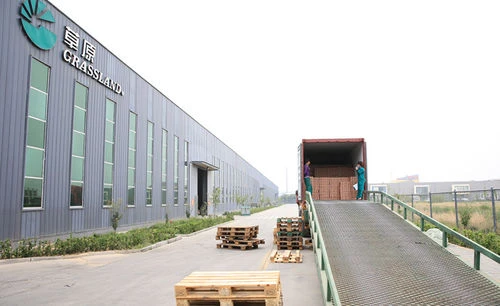
Grinding discs can be made from similar materials as cutting discs but often include additional bond materials that help retain the abrasive particles and provide stability during operation. The design and structure also allow for better control and maneuverability when shaping materials.
Key Differences
1. Purpose The most significant difference between cutting and grinding discs lies in their purpose. Cutting discs are meant for slicing through materials, while grinding discs are intended for shaping and finishing surfaces.
2. Thickness and Composition Cutting discs are generally thinner to allow for easier cuts, whereas grinding discs are thicker and more durable to withstand the pressures of abrasion.
3. Design and Usage Cutting discs are sharper and designed for cutting actions, while grinding discs are rougher and made for grinding actions. This fundamental difference necessitates varying speeds and pressures during use.
4. Applications Cutting discs are typically used in applications where precision cuts are needed, such as metal fabrication and construction. In contrast, grinding discs are often utilized in finishing processes, welding preparation, and sharpening tasks.
Conclusion
When selecting between cutting and grinding discs, it is essential to understand the specific requirements of your project. Utilizing the correct type of disc not only improves efficiency but also enhances the quality of the finished product. By recognizing the unique characteristics and applications of each disc, professionals can make informed choices, ensuring better results in their work. Whether you are cutting, grinding, or shaping materials, having the right tools at your disposal is key to achieving success in any metalworking or manufacturing environment.
Post time:Dec - 12 - 2024