Understanding the Role of Flap Disc Manufacturers in the Abrasives Industry
In the world of metalworking and fabrication, the importance of high-quality abrasives cannot be overstated. Among these abrasives, flap discs have become increasingly popular due to their versatility, efficiency, and effectiveness in various applications. As a crucial component in this industry, flap disc manufacturers play a significant role in ensuring that these products meet the varying needs of their users. This article delves into the world of flap disc manufacturing, exploring the processes, materials, and significance of these essential tools in the metalworking domain.
What Are Flap Discs?
Flap discs are abrasive tools made of multiple overlapping layers or flaps of abrasive material attached to a central backing plate. They are primarily used for grinding, blending, and finishing surfaces, making them ideal for tasks such as weld preparation, surface smoothing, and edge deburring. Unlike traditional grinding wheels, flap discs offer a combination of durability, flexibility, and ease of use, making them the go-to choice for many professionals in the metalworking industry.
The Manufacturing Process
The production of flap discs involves a series of intricate steps, starting with the selection of materials. The key components include the abrasive grain, the backing material, and the adhesive. Abrasive grains vary in type, including aluminum oxide, zirconia, and ceramic, each suitable for different applications based on the material being worked on and the desired finish.
1. Material Selection Flap disc manufacturers must choose the appropriate abrasive grain based on the intended use. For instance, zirconia grains are known for their longevity and effectiveness on harder metals, while aluminum oxide is often chosen for softer materials.
2. Backing Preparation The backing material, usually made from fiberglass or plastic, provides stability and support to the flaps. The thickness and stiffness of the backing can significantly influence the performance of the flap disc.
3. Flap Cutting and Layering After preparing the backing, manufacturers cut the flaps from sheets of abrasive material. These flaps are then layered and arranged at specific angles to maximize surface contact and enhance the grinding action during use.
flap disc manufacturer
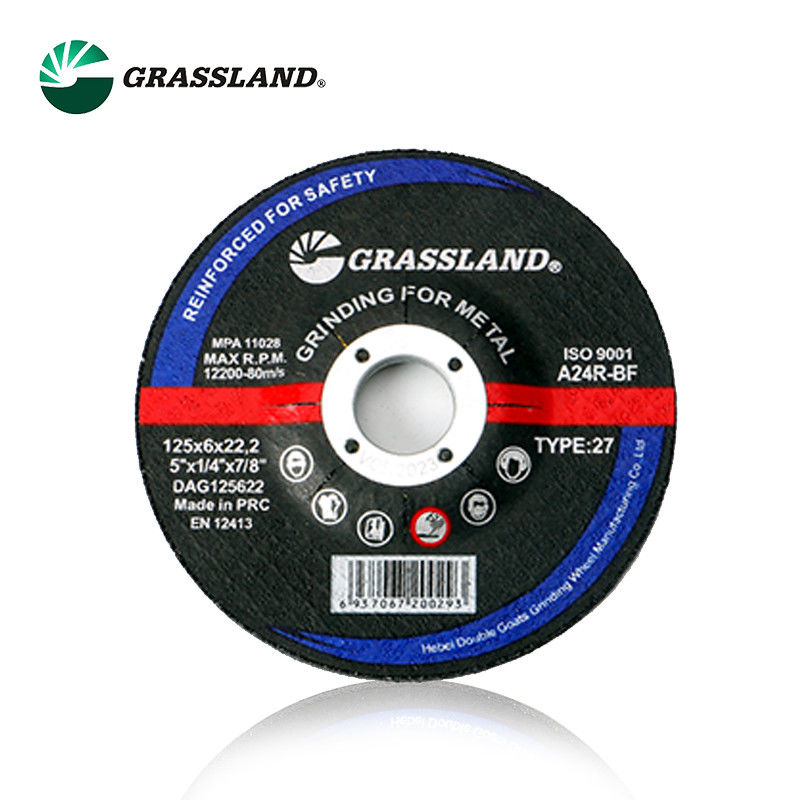
4. Adhesive Application An adhesive is then applied to secure the flaps to the backing. This step is critical, as a well-bonded disc can withstand the rigors of grinding without losing its flaps prematurely.
5. Curing Process Once assembled, the flap discs undergo a curing process, where they are heated to ensure that the adhesive bonds securely. This enhances the overall durability and performance of the discs.
6. Quality Control Flap disc manufacturers implement rigorous quality control measures throughout the production process. Each batch is tested for performance, consistency, and safety standards to ensure that the end product meets industry requirements.
The Importance of Quality in Flap Disc Manufacturing
The quality of flap discs directly impacts the efficiency and safety of the grinding process. Manufacturers invest in advanced technology, research, and development to create products that not only meet but exceed customer expectations. High-quality flap discs lead to faster material removal, improved surface finishes, and reduced operator fatigue—all critical factors in professional metalworking environments.
Moreover, with the growing emphasis on sustainability and environmental responsibility, leading flap disc manufacturers are also exploring eco-friendly materials and production methods. This shift not only addresses consumer demand for greener products but also plays a vital role in the industry’s overall sustainability initiatives.
Conclusion
Flap discs are indispensable tools in the abrasives industry, with manufacturers playing a critical role in their development. By focusing on quality materials, innovative manufacturing processes, and stringent quality control, flap disc manufacturers ensure that professionals in metalworking have access to reliable and efficient tools. As the industry evolves, these manufacturers will continue to adapt and innovate, driving advances in abrasive technology that meet the ever-changing needs of their clients. Whether in automotive repair, construction, or metal fabrication, the impact of high-quality flap discs is profound, underscoring the significance of their manufacturing in shaping the future of metalworking.
Post time:Dec - 12 - 2024