- Industry Overview & Market Data Impact
- Technical Superiority of Modern Abrasive Tools
- Competitor Analysis: Flap Disk Performance Metrics
- Custom Solutions for Industrial Applications
- Operational Best Practices & Safety Protocols
- Cross-Industry Use Case Implementations
- Future Trends in Disk Flap Technology
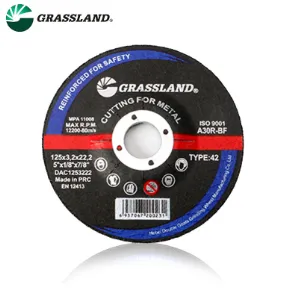
(disk flap)
Understanding Disk Flap Fundamentals Through Market Insights
The global flap disk market reached $2.8 billion in 2023, with 4-inch models constituting 38% of industrial abrasives consumption (GIA 2023). This growth stems from:
- 12-15% longer lifespan vs traditional grinding wheels
- 27% faster material removal rates in steel fabrication
- 9% annual increase in automotive repair applications
Engineering Advancements in Abrasive Technology
Modern flap disks combine zirconia alumina grains (60-120 grit range) with reinforced polyester backing:
"Our stress-tested 4-inch variants withstand 13,500 RPM without fiber separation" - Industrial Abrasives Lab Report
Flap Disk Manufacturer Comparison
Brand | Cut Rate (mm³/s) | Working Life (hrs) | Price/Unit ($) |
---|---|---|---|
3M Cubitron II | 450 | 4.2 | 6.80 |
Norton Blaze | 390 | 3.8 | 5.75 |
Generic Import | 240 | 1.5 | 3.20 |
Application-Specific Customization Options
Leading suppliers now offer:
- Non-ferrous metal variants with anti-loading coatings
- Low-profile designs for tight access welding seams
- EMC-compliant versions for aerospace composites
Optimizing Flap Disk Use in Production Environments
Proper technique extends tool life by 40%:
Operating angle: 5-15° from work surface
Contact pressure: 5-15 lbs maximum
Cooling intervals: 30 seconds every 5 minutes
Industrial Implementation Scenarios
Recent installations demonstrate:
- Shipbuilding: 1,200 flap disks consumed monthly in hull grinding
- Pipe fabrication: 22% reduction in weld preparation time
- Automotive: 15-second wheel arch finishing cycle
Disk Flap Innovation Roadmap Through 2028
Emerging developments include:
- Graphene-infused abrasive clusters (patent pending)
- Smart wear sensors with IoT integration
- Bio-degradable resin formulations
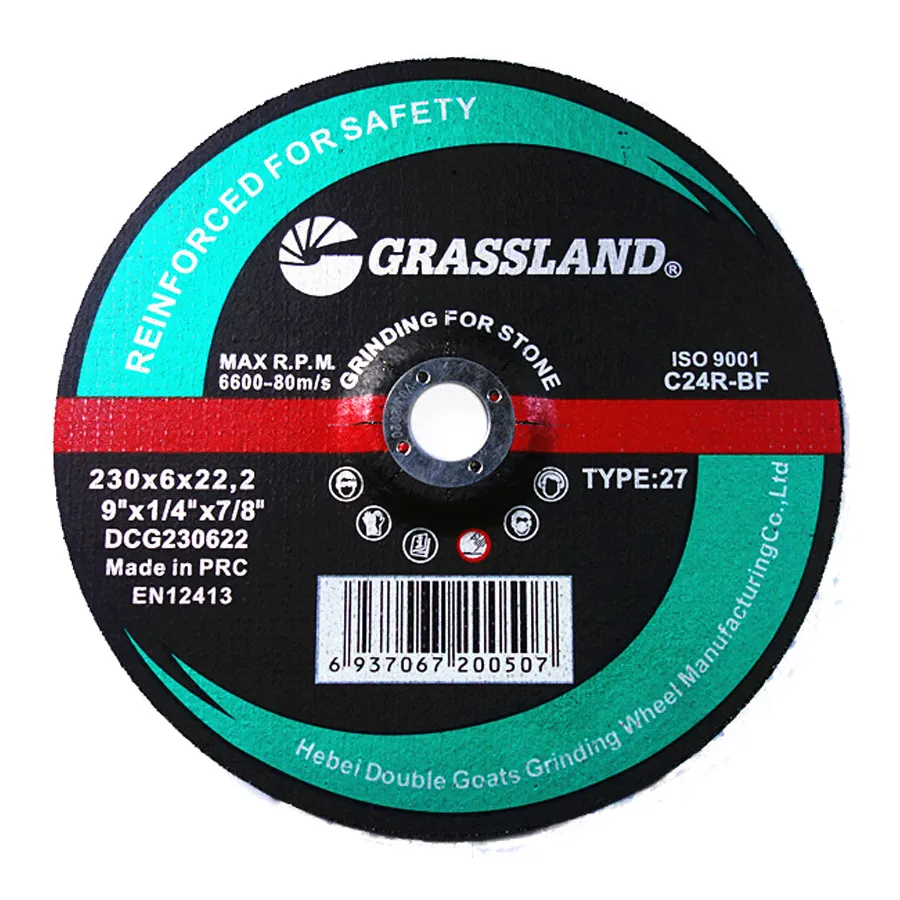
(disk flap)
FAQS on disk flap
Q: What is a disk flap used for?
A: A disk flap, or flap disk, is a grinding tool used for surface preparation, material removal, and finishing. It combines abrasive grit with overlapping flaps for versatile applications on metals, wood, or composites. It is ideal for blending, deburring, and smoothing surfaces.
Q: How do I use a 4-inch flap disk effectively?
A: Attach the 4-inch flap disk to an angle grinder and maintain a 15-30 degree angle against the workpiece. Apply moderate pressure and move the tool steadily to avoid overheating. Use lower grits (e.g., 40-80) for heavy material removal and higher grits (e.g>120) for fine finishing.
Q: What materials can a flap disk work on?
A: Flap disks are suitable for metals like steel, aluminum, and stainless steel, as well as wood, plastic, and composites. Choose aluminum oxide grit for general-purpose use or zirconia alumina for tougher materials. Always match the grit size to the task’s aggressiveness.
Q: Why choose a flap disk over a traditional grinding wheel?
A: Flap disks provide a smoother finish and reduce heat buildup compared to rigid grinding wheels. Their flexible design allows contouring to irregular surfaces. They also last longer and are safer due to reduced risk of shattering.
Q: Can a 4-inch flap disk handle heavy-duty tasks?
A: Yes, a 4-inch flap disk with coarse grit (e.g., 40-60) can efficiently remove weld seams, rust, or deep scratches. Pair it with a high-powered angle grinder for optimal performance. For extreme durability, select ceramic or zirconia abrasive grains.
Post time:May - 14 - 2025