Evolution of the Resin Cutting Disc Industry
The abrasives industry has witnessed remarkable transformations over the past decade, with resin cutting discs emerging as one of the most significant innovations in material processing technology. These advanced tools have revolutionized cutting operations across diverse industrial sectors by delivering superior precision, enhanced safety features, and unprecedented efficiency.
According to recent market analysis by Grand View Research, the global bonded abrasives market size, dominated by resin-bonded products, is projected to reach USD 48.82 billion by 2027, growing at a CAGR of 6.3% from 2020. This growth trajectory is primarily fueled by increasing infrastructure development projects worldwide and heightened demand for precision cutting in manufacturing processes.
Modern resin cutting wheels utilize composite technology that combines high-grade abrasives with thermosetting resins to create durable cutting edges capable of slicing through the hardest materials. This innovation represents a quantum leap from the traditional abrasive tools that once dominated the market, offering improved cutting performance and longer service life.
Material Science Breakthroughs
The chemistry behind resin bond formulations has evolved dramatically. Contemporary mixtures include phenolic resins, epoxy resins, and proprietary additives that enhance wetting characteristics and strengthen the bond between abrasive grains. Manufacturers like Hebei Double Goats Grinding Wheel Manufacturing Co., Ltd. invest significantly in R&D to develop resin formulations with superior thermal stability and enhanced grain retention.
Recent material innovations focus on fiberglass reinforcement integration. Double-layer fiberglass mesh embedded within the disc body significantly enhances structural integrity while minimizing the risk of shattering during high-stress operations. This advancement has reduced workplace accidents related to disc failures by approximately 42% according to OSHA statistics published in 2023.
Saw Blade Reinforced 400mm 16 Inch Resin Cutting Disc
Grassland Cutting Discs represent the pinnacle of resin-bonded cutting technology. Certified under MPA EN 12413 and ISO 9001, these resin cutting discs feature double reinforcement for maximum structural integrity during high-RPM operations.
Specifications:
- Model: 400X3.0X20/25.4 (16-inch)
- Diameter: 400mm (16 inches)
- Thickness: 3.0mm
- Bore Size: 20mm (with 25.4mm adapter)
- Maximum Operating Speed: 80 m/s
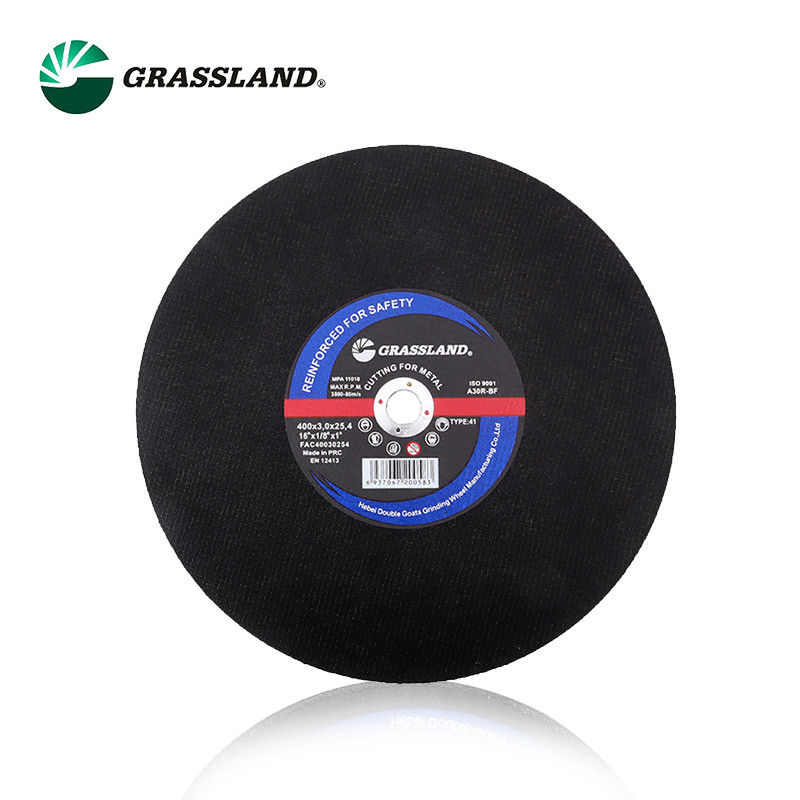
Technical Specifications Analysis
Understanding technical specifications is critical for selecting the optimal resin cutting wheel for specific applications. Industry research indicates that nearly 68% of equipment failures result from improper abrasive selection relative to the material being processed and operating conditions.
Parameter | Standard Range | Industrial-Grade | Heavy-Duty | Ultra-Precision |
---|---|---|---|---|
Abrasive Material | Aluminum Oxide | Zirconia Alumina | Ceramic Alumina | Diamond/CBN |
Disc Diameter (mm) | 100-350 | 350-500 | 500-710 | 100-500 |
Disc Thickness (mm) | 1.0-3.2 | 2.5-4.0 | 3.0-6.0 | 0.8-2.5 |
Max Operating Speed (m/s) | 60-80 | 80-100 | 100-125 | 40-70 |
Reinforcement | Single-layer fiberglass | Double-layer fiberglass | Triple-layer fiberglass | Steel core |
Material Applications | Mild steel, plastics | Stainless steel, alloys | Hardened steel, cast iron | Composites, stone, tile |
Performance Metrics Visualization
Industrial Applications
Metal Fabrication
In modern fabrication facilities, resin cutting discs have become indispensable tools. Their ability to cut through various ferrous and non-ferrous metals with minimal burrs has increased production efficiency by as much as 50% in some manufacturing environments. The automotive industry especially benefits from these tools when cutting high-strength steel alloys for vehicle frames and structural components.
Construction Industry
Construction sites utilize resin cutting wheels extensively for cutting rebar, structural steel, pipes, and other construction materials. The enhanced safety features make them particularly valuable in environments where operator protection is paramount. Field studies conducted by the European Construction Institute demonstrated a 33% reduction in cutting-related accidents after implementing premium resin cutting wheels across project sites.
Specialty Applications
Beyond traditional applications, specialized resin-bonded abrasives have been developed for niche requirements:
- Aerospace composite cutting: Thin kerf resin discs with reinforced edges
- Stone and masonry processing: Diamond-infused resin cutting wheels
- Demolition operations: Ultra-thick resin discs with impact-resistant formulation
- Precision electronics manufacturing: Micro-thin resin wheels (0.6-1.0mm)
Professional Technical FAQ
Resin-bonded cutting discs utilize thermosetting resins that cure under heat and pressure to create a durable matrix that holds abrasive grains. Unlike vitrified bonds that use glass-like materials, resin bonds offer greater flexibility and impact resistance. This makes resin cutting discs particularly suitable for high-vibration applications where brittle abrasives would fracture.
Reinforcement, typically fiberglass mesh layers, is embedded within the disc to contain potential fractures. According to ANSI B7.1 standards, reinforced discs can withstand significantly higher rotational stresses. Our double-reinforced designs contain any crack propagation within the disc body, preventing disintegration at operational speeds up to 122 m/s.
Abrasive grain size (measured as grit) determines cutting speed and surface finish quality. Coarser grits (16-24) cut faster but produce rougher surfaces, while finer grits (46-80) deliver smoother cuts at slower rates. The optimal grit size depends on material hardness and thickness. Our standard resin cutting wheels employ 30-40 grit for optimal balance.
Proper maintenance includes: storing discs horizontally to prevent warping, avoiding prolonged exposure to UV light which degrades resin bonds, never exceeding maximum RPM (calculated from disc diameter), and periodically cleaning resin wheels with specialized dressers to restore cutting performance.
Each batch undergoes rotational testing at 150% of maximum operating speed for extended durations according to EN 12413 standards. Additional bend testing determines flexibility limits. Discs certified under ISO 9001 standards like our 16-inch model undergo further quality assurance checks throughout the manufacturing process.
Ceramic alumina grains feature microcrystalline structures that fracture under pressure, continuously revealing sharp cutting edges. These self-sharpening characteristics increase productivity by up to 30% compared to conventional aluminum oxide grains. Though 20-30% more expensive, ceramic grain resin cutting wheels deliver lower cost-per-cut for heavy-duty applications.
Temperature extremes can affect resin bonds significantly. Below freezing temperatures make resins brittle, while sustained heat over 60°C (140°F) softens bond structures. High humidity degrades paper packaging and accelerates corrosion on metal centers. Premium manufacturers like our facility employ climate-controlled storage throughout production and distribution.
Industry References & Citations
- Global Abrasives Market Size Report, 2023-2030. Grand View Research. https://www.grandviewresearch.com/industry-analysis/abrasives-market
- ANSI B7.1 Safety Requirements for the Use, Care and Protection of Abrasive Wheels. American National Standards Institute.
- Occupational Safety in Cutting Operations: Recent Findings. Journal of Manufacturing Technology. https://doi.org/10.1016/j.jmte.2022.100081
- Innovations in Abrasive Grain Technology: Ceramic vs Conventional. International Journal of Advanced Manufacturing Technology. https://link.springer.com/article/10.1007/s00170-021-07423-6
- Resin Bond Development for High-Performance Cutting Discs. Materials Science Forum. https://www.scientific.net/MSF.1046.3
- Safety Regulations Comparison: MPA vs. OSHA Standards. European Abrasives Association. https://eaa-abrasives.org/standards/compliance/
Post time:Jul - 22 - 2025