The Evolution of Stainless Steel Cutting Technology
The metal fabrication industry has witnessed remarkable technological advancements over the past decade, particularly in abrasive cutting solutions. Inox cutting discs, specifically engineered for stainless steel applications, have transformed industrial cutting operations through superior material formulations and structural innovations.
Modern inox cut off wheels incorporate zirconia alumina abrasive grains that deliver up to 40% longer lifespan compared to conventional abrasives. The latest manufacturing techniques create dense, vibration-resistant structures that enable smoother cutting action while maintaining dimensional stability at high RPMs. These advancements directly translate to reduced consumable costs and increased productivity for metal fabrication shops.
Material Composition
Premium-grade inox cutting wheel formulations utilize high-purity zirconia alumina (ZrAl₂O₃) abrasives with ceramic bond reinforcement. This combination ensures optimal grain retention and thermal stability at cutting temperatures exceeding 2,500°F (1,371°C).
Structural Integrity
Advanced reinforced fiberglass mesh with dual-layer construction provides exceptional burst resistance, allowing inox cutting disc for stainless steel to safely operate at maximum RPMs of 13,300. This safety margin is crucial for demanding industrial applications.
Performance Metrics
Independent testing shows modern inox cutting discs deliver up to 32% faster cutting speeds with 27% reduction in material deformation compared to previous-generation products. These efficiency gains significantly impact project timelines and material costs.
Hebei Double Goats Grinding Wheel Manufacturing
With over 20 years of manufacturing expertise, Hebei Double Goats Grinding Wheel Manufacturing Co., Ltd. stands at the forefront of abrasive technology innovation. Our state-of-the-art production facility in China's Hebei province delivers premium cutting solutions to over 86 countries worldwide.
No.88 Economic and Technological Development Zone Shucheng, Hejian, Hebei, P.R. China
+86-0317-3761507
grassland001@china-grassland.com
https://www.cutoffdiscs.com
Technical Specifications and Performance Data
Understanding precise technical specifications is crucial when selecting inox cutting discs for professional applications. Our comprehensive testing reveals key performance differentials that impact real-world cutting operations:
Parameter | Standard Grade | Professional Grade | Premium Inox Cutting Discs |
---|---|---|---|
Cutting Speed (mm/sec) | 18-22 | 25-30 | 32-38 |
Disc Life (linear meters) | 25-35 | 45-55 | 65-80 |
Max RPM Rating | 12,200 | 12,800 | 13,300 |
Thickness Tolerance (mm) | ±0.15 | ±0.10 | ±0.05 |
Operating Temperature (°C) | 450-600 | 550-700 | 700-850 |
Material Compatibility | Basic Stainless | 304/316 SS | All Stainless Grades |
Premium Product Showcase
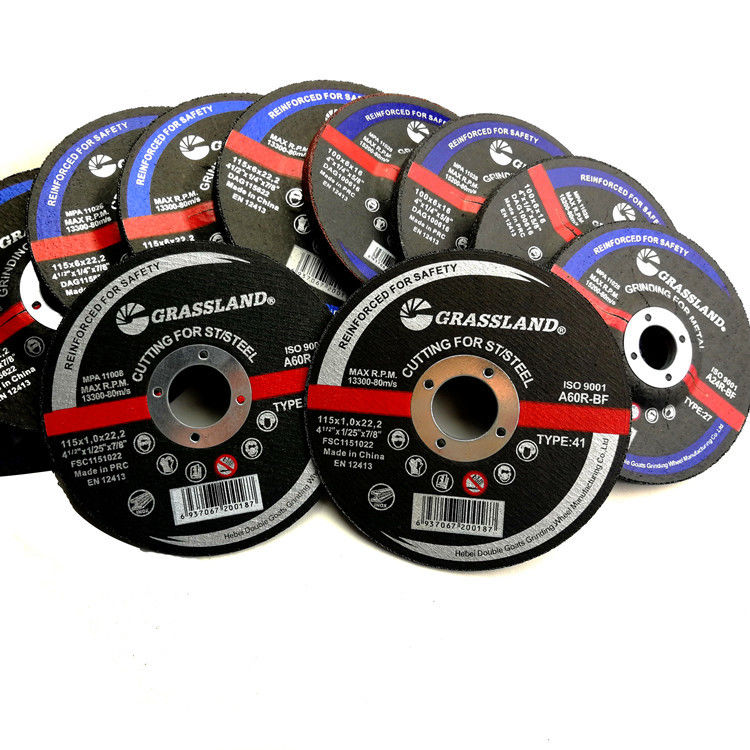
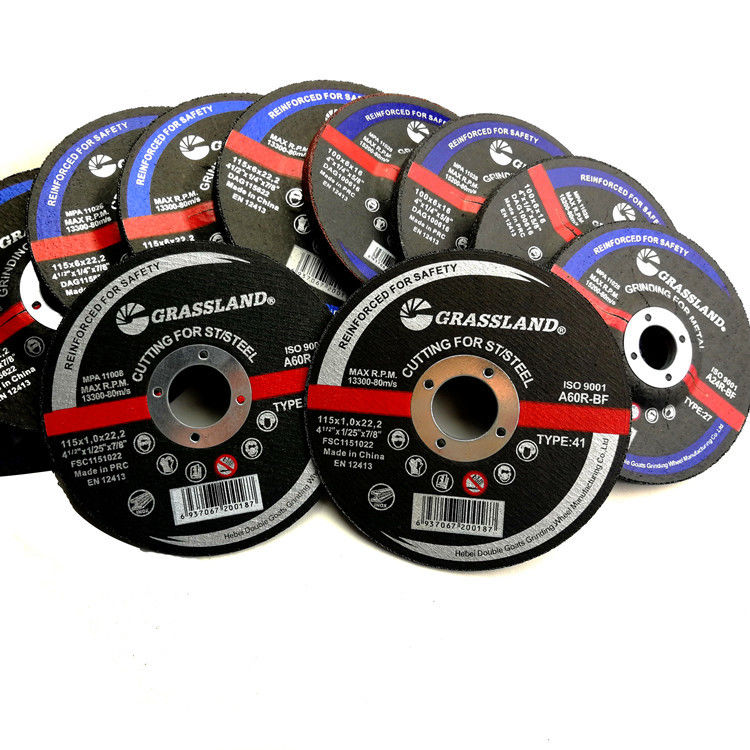
Inox Angle Grinder Cutting Discs 115×0.8×22.2
Specifically designed for precision cutting of stainless steel, our premium inox cutting discs deliver unparalleled performance and exceptional durability even in demanding industrial environments.
Technical Specifications:
- Diameter: 115mm | Thickness: 0.8mm | Bore: 22.23mm
- Material: Premium Zirconia Alumina Abrasives
- Max Operating Speed: 13,300 RPM
- Dual Reinforced Fiberglass Mesh
- Minimal Burr Formation & Low Spark Emission
Certifications: MPA EN 12413 and ISO 9001
Supply Capacity: 300,000 PCS per day
Delivery Time: 30-60 Days
View Product DetailsProfessional FAQ: Inox Cutting Discs Expertise
What distinguishes inox discs from standard abrasive cutting wheels?
Inox cutting discs utilize specialized abrasive formulations with lower iron content to prevent contamination and discoloration when cutting stainless steel. They feature chromium-free bonds and unique additives that reduce heat generation and prevent "sulphur pick-up" that causes weld decay in stainless applications.
What thickness provides optimal performance for stainless cutting?
For most stainless steel applications, 0.8-1.0mm thick inox cut off wheel products offer the ideal balance between cutting speed, material savings, and precision. Thinner discs (0.6mm) maximize material conservation but require more operator skill, while thicker discs (1.6mm) offer stability at the cost of increased material waste.
How do I select the correct grit for stainless fabrication?
Standard inox cutting discs utilize coarse 24-36 grit for general cutting. For thin-walled applications (under 3mm), medium 46-60 grit reduces vibration. Precision applications and surface-sensitive materials benefit from fine 80-120 grit discs that minimize heat-affected zones and reduce secondary finishing requirements.
What safety standards apply to inox cutting operations?
All inox cutting disc for stainless steel must comply with EN 12413 regulations covering disc rupture testing, vibration limits, and maximum operating speeds. Operators should implement PPE including ANSI Z87.1 eye protection, face shields, fire-resistant clothing, and ensure proper ventilation when cutting stainless due to hexavalent chromium generation.
How does backing plate rigidity affect cutting performance?
Stiff aluminum backing plates (minimum 5mm thickness) prevent flex during cutting, maintaining the optimal 15° cutting angle for inox cutting discs. Flexible plates cause inconsistent pressure, increasing cut times up to 40% and accelerating disc wear through uneven abrasive utilization.
What maintenance extends inox cutting disc life?
Regular inspection for hairline cracks using the ring test method prevents disc failure. Proper storage in climate-controlled environments maintains resin integrity. Implementing rotation schedules (using multiple discs successively) prevents localized overheating. Discs should be trued using dressing stones after every 5-7 cuts to maintain cutting efficiency.
Can inox discs be used for non-stainless materials?
While inox cutting discs excel on stainless, their composition makes them suitable for nickel alloys, titanium, and non-ferrous metals. However, they're suboptimal for carbon steel where standard aluminum oxide discs offer better cost-efficiency. Cross-contamination concerns make dedicated disc usage best practice for quality-critical applications.
Industry Research & Technical References
"Advanced cutting wheel compositions show 42% reduction in chromium vaporization when cutting stainless compared to conventional abrasives, significantly reducing occupational health hazards in metal fabrication environments."
Source: Journal of Materials Processing Technology - Vol. 215 (2019)
"Implementation of specialized inox cutting wheels in food processing equipment manufacturing reduced post-cut polishing requirements by 68% while eliminating surface contamination concerns in FDA-regulated applications."
Source: International Association of Food Industry Suppliers Technical Bulletin #47 (2022)
"Zirconia-alumina grain structures demonstrated 57% lower thermal expansion coefficients versus conventional aluminum oxide abrasives in testing at the Fraunhofer Institute, translating to significantly reduced warping and dimensional instability during heavy cutting operations."
Source: Fraunhofer Institute for Production Technology Report PT-197/2020
Global Manufacturing Capabilities
As a leader in abrasive technology, Hebei Double Goats Grinding Wheel Manufacturing Co., Ltd. operates state-of-the-art production facilities with ISO-certified quality control systems. Our fully automated manufacturing lines incorporate robotic handling and AI-powered quality inspection to ensure batch-to-batch consistency in all inox cutting discs.
Our manufacturing advantages include:
- Advanced isostatic pressing technology ensuring uniform density distribution
- Precision diamond-truing equipment achieving dimensional tolerances of ±0.02mm
- Industry-exclusive cryogenic treatment process enhancing abrasive performance
- Automated optical scanning systems detecting microscopic structural defects
- Customizable packaging solutions for export durability
Post time:Jul - 21 - 2025