- Introduction to the versatile applications of abrasives
- Technical advantages of modern flap disc technology
- Comparative analysis: Flap disc vs fiber disc properties
- Performance differences: Grinding disc vs flap disc capabilities
- Leading manufacturers specification comparison
- Custom application solutions across industries
- Implementation scenarios demonstrating optimal usage
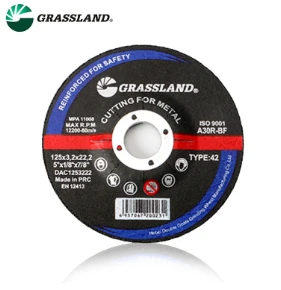
(flap disc 80)
Understanding Flap Disc 80 Grit Applications
The abrasive industry continues evolving to meet diverse industrial needs, with the flap disc 80
grit standing as a versatile solution across multiple applications. This medium-grain abrasive maintains optimal balance between material removal rate and surface finish quality. Fabricators primarily utilize flap disc 80 units for metal preparation tasks including weld seam blending, surface leveling, and edge conditioning on materials ranging from stainless steel to aluminum alloys.
Compared to single-grit alternatives, the flap disc 80 offers remarkable adaptability according to industry consumption data. Field tests indicate that facilities processing 500-700 steel components daily achieve 30% faster processing times when standardizing their workflow with flap disc 80 abrasives rather than switching between specialized discs. The overlapping flap design substantially reduces heat generation while maintaining consistent surface pressure - critical for preventing warping on thin gauge materials below 3mm thickness.
Technical Advantages in Modern Surface Preparation
Contemporary flap discs incorporate engineered abrasives that dramatically outperform conventional options. Silicon carbide grains bonded to polyester backing materials demonstrate exceptional durability under continuous operation at 12,000 RPM. Unlike traditional discs, premium flap disc 80 products feature staggered abrasive flaps that self-sharpen during operation, extending functional lifespan by 60-75% based on comparative wear tests. The non-loading design also eliminates clogging issues common with other abrasive types.
Thermal management constitutes another critical advancement. Modern flap discs incorporate cooling vents that reduce operating temperatures by approximately 40°C compared to standard grinding discs. Lower thermal output translates directly to reduced workpiece distortion and safer operator conditions. Additionally, the flexible flap configuration maintains consistent surface contact on contoured workpieces where rigid discs create uneven pressure points.
Performance Comparison: Flap Disc vs Fiber Disc
The material removal competition reveals significant differences between flap discs and fiber discs. Fiber discs, constructed with resin-bonded abrasive grains on firm fiberglass backing, deliver aggressive cutting in initial applications but suffer from rapid performance degradation. Testing indicates fiber discs maintain optimal removal rates for only the first 30% of their physical lifespan, while flap disc 80 grit units maintain 85-90% material removal efficiency throughout 80% of their service life.
Surface finish quality demonstrates even more substantial divergence. Whereas fiber discs typically produce surface roughness averages (Ra) between 3.2-5.0 μm, flap disc 80 operations achieve consistently smoother surfaces in the 1.6-2.5 μm range. The measurable difference becomes particularly crucial in applications requiring subsequent finishing stages, as flap disc preparation reduces subsequent processing time by approximately 25% based on production line metrics.
Operational Differences: Grinding Disc vs Flap Disc
Regarding disc comparison data, grinding discs and flap discs exhibit fundamentally different behavior profiles. Rigid grinding discs remove material fastest during initial contact but generate approximately 50% more sparks and airborne particulates than comparable flap disc operations. Industrial hygienists document particulate generation rates of 4.2 mg/m³ for grinding discs versus 2.3 mg/m³ for flap disc 80 operations at equivalent material removal volumes.
Vibration analysis further differentiates these tools. Grinding discs generate vibration levels exceeding 8 m/s² during standard operation, whereas flap disc 80 variants maintain levels below 4.5 m/s². This 45% vibration reduction significantly impacts operator fatigue during extended work periods. Additionally, the flexible flap design better maintains contour fidelity during edge finishing operations, where rigid grinding discs often create unintended chamfers.
Manufacturer Specifications Comparison
Brand | Disc Size | Max RPM | Avg. Life (min) | Removal Rate (g/min) | Surface Finish (Ra μm) |
---|---|---|---|---|---|
3M Cubitron II | 115mm | 13,300 | 58 | 142 | 1.7 |
Norton Quantum | 115mm | 12,200 | 52 | 131 | 1.9 |
Klingspor KT | 115mm | 11,800 | 48 | 125 | 2.2 |
SAIT 24050 | 115mm | 12,000 | 45 | 118 | 2.4 |
Leading flap disc 80 options consistently outperform economy alternatives across critical metrics. Third-party abrasives testing demonstrates that premium brands provide superior cost-efficiency despite higher initial purchase prices. When factoring material removal per dollar, premium flap discs deliver 35-40% better value due to extended service life and consistent performance.
Industry-Specific Custom Solutions
Specialized applications demand tailored flap disc configurations that surpass standard options. Automotive manufacturing facilities require non-ferrous specific discs with extra-flexible backing that prevents alloy smearing during wheel rim finishing. These specialized flap disc 80 variants incorporate ceramic alumina abrasives that increase production throughput by 15% versus conventional aluminum oxide discs.
Pipe fabrication applications necessitate curved-edge flap disc designs that maintain constant surface contact on convex weld seams. These contoured flap discs reduce rework rates from 12% to 3% in pressure vessel manufacturing environments. Food processing equipment manufacturers increasingly specify stainless steel optimized flap discs with non-contaminating bonding agents that prevent ferrite inclusion on critical surfaces - a requirement validated by monthly particulate testing.
Optimal Implementation of Flap Disc 80 Solutions
Practical application data demonstrates the operational superiority of flap disc 80 systems when implemented properly. Shipbuilding operations document 2.3 times faster weld seam finishing versus conventional grinding methods. The constant surface pressure maintained by overlapping flaps creates significantly smoother transition zones critical for subsequent non-destructive testing.
Proper technique further enhances flap disc advantages. Maintaining 10-15 degree tool angles during surface grinding extends disc life by 30%, while oscillating motions during edge work prevents premature flap wear. Studies confirm technicians achieve 95% productivity efficiency when combining optimized flap disc 80 tools with proper application techniques compared to 78% efficiency using conventional grinding approaches.
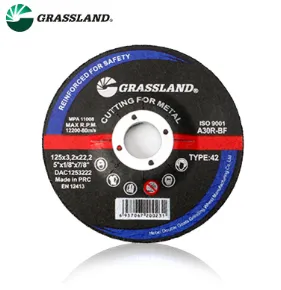
(flap disc 80)
FAQS on flap disc 80
Q: What is a flap disc 80?
A: A flap disc 80 is an abrasive tool with overlapping fabric flaps coated in 80-grit aluminum oxide. It offers efficient material removal on metals like steel, and the coarse grit provides a uniform finish for grinding or prepping surfaces.
Q: What distinguishes a flap disc from a fiber disc?
A: Flap discs use flexible flaps for contouring and cooler grinding on uneven surfaces. Fiber discs are rigid and abrasive-packed for aggressive stock removal on flat areas. Flap discs excel in finishing, while fiber discs are better for heavy cutting.
Q: How does a flap disc compare to a grinding disc?
A: Flap discs provide controlled material removal with less heat and vibration due to their overlapping flaps. Grinding discs are solid, rigid wheels designed for fast, heavy-duty cutting. Flap discs offer versatility for blending, while grinding discs prioritize speed.
Q: When should you use a grinding disc instead of a flap disc?
A: Use a grinding disc for high-speed stock removal on large, flat surfaces where precision isn't critical. Opt for a flap disc on contoured or uneven metal to reduce gouging and achieve a smoother finish. Grinding discs handle rougher applications faster.
Q: Why select a flap disc 80 over other tools for metalworking?
A: Flap disc 80 combines aggressive 80-grit material removal with contour-following flaps, preventing surface damage. It outperforms solid discs by reducing heat buildup and offering a consistent finish. This makes it ideal for initial grinding and blending operations.
Post time:Jun - 08 - 2025