Understanding Flap Discs for Metalworking A Comprehensive Guide
Flap discs are pivotal tools in the metal fabrication and finishing industries, offering versatility and efficiency for various applications. Whether you are grinding, deburring, or polishing metal surfaces, flap discs provide an excellent solution that enhances productivity and finish quality. This article delves into what flap discs are, their construction, advantages, and best practices for use, particularly in metalworking applications.
What are Flap Discs?
Flap discs are abrasive wheels that consist of overlapping layers or flaps of abrasive material, attached to a central hub. Unlike traditional grinding wheels that provide a flat surface, flap discs offer a more flexible option that adapts to the contours of the workpiece. They come in various sizes, materials, and grit levels, making them suitable for a range of applications on different metals.
Construction of Flap Discs
The construction of flap discs fundamentally affects their performance and suitability for various tasks. Typically, they are made from aluminum oxide, zirconia alumina, or ceramic abrasives, each chosen based on the specific needs of the job.
- Aluminum Oxide Commonly used for general-purpose grinding and finishing on metals such as steel and stainless steel. - Zirconia Alumina Ideal for tougher materials and higher stock removal rates, it is often used for stainless steel and other hard metals. - Ceramic Abrasives Best for heavy grinding applications due to their self-sharpening properties, allowing for efficient grinding of hard metals.
The backing plate of the disc can be made from fiberglass or plastic, which provides stability and durability. The flap orientation is also crucial; angled flaps allow for smoother contouring and finishing, while flat flaps are more suited for aggressive grinding tasks.
Advantages of Flap Discs
Flap discs offer several advantages over traditional abrasives and grinding wheels
1. Versatility They can perform multiple operations, including grinding, blending, finishing, and polishing, making them suitable for various metalworking applications. 2. Effective Material Removal The design allows for efficient material removal while producing a finer finish compared to standard grinding wheels. 3. Longer Lifespan Due to their layered construction, flap discs typically last longer than grinding wheels, reducing the frequency of tool changes and downtime. 4. Reduced Heat Buildup The unique design enables better cooling during use, which helps to prevent heat discoloration and warping on sensitive metal surfaces.
5. Improved Safety Flap discs are generally safer as they are less likely to shatter than traditional grinding wheels, making them a better choice for operators concerned about safety.
Choosing the Right Flap Disc
flap disc for metal
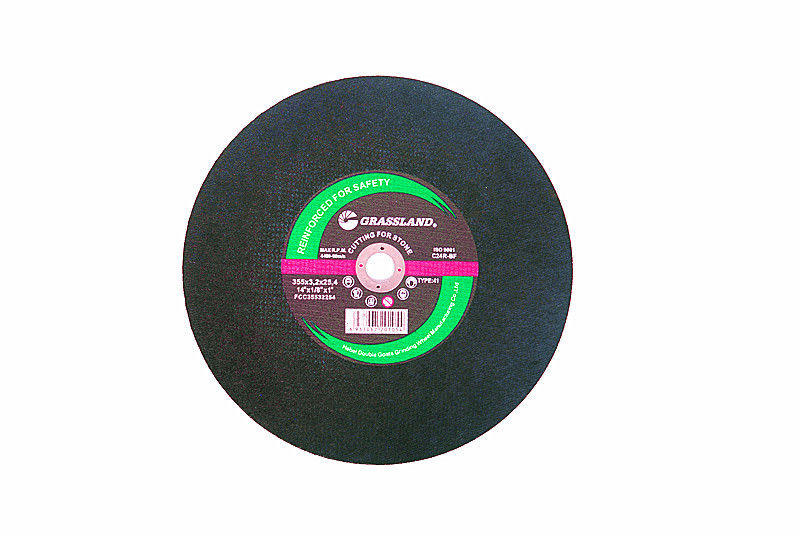
Selecting the appropriate flap disc for your specific metalworking task involves several considerations
- Material Type Determine the type of metal you will be working with. Different materials respond better to specific types of abrasives. - Grit Size Grit size indicates the disc's coarseness. A lower grit number (e.g., 36) is more aggressive and suitable for heavy material removal, while a higher grit number (e.g., 120) is better for finishing work.
- Disc Diameter The disc size should match the tool being used and the scale of the job. Larger discs can cover more area and remove more material, while smaller discs are better for detailed work.
- Operating Speed Ensure that the flap disc's maximum RPM rating is compatible with your grinder to prevent accidents.
Best Practices for Using Flap Discs
To get the most out of flap discs, follow these best practices
1. Maintain the Correct Angle Always maintain the appropriate angle between the flap disc and the workpiece for optimal material removal and surface finish.
2. Use Light Pressure Applying excessive pressure can reduce the efficiency of the flap disc and lead to faster wear. Let the abrasive do the work instead.
3. Keep the Tool Moving Avoid staying in one spot for too long to prevent heat buildup and surface damage.
4. Inspect Regularly Regularly check the condition of your flap discs and replace them as needed to ensure safety and effectiveness.
Conclusion
Flap discs are an indispensable tool in metalworking, blending versatility and efficiency in one compact solution. By understanding their construction, benefits, and best practices, operators can significantly enhance their grinding and finishing processes, ensuring high-quality results on every project. Whether you are a seasoned professional or a newcomer to metal fabrication, incorporating flap discs into your toolkit will surely optimize your workflow and improve the quality of your finished products.
Post time:Dec - 05 - 2024