The Importance of Grinding and Polishing Flap Discs in Metalworking
Grinding and polishing flap discs are essential tools in the metalworking industry. They serve a multitude of purposes, making the processes of grinding, blending, and finishing more efficient and effective. The unique design and composition of flap discs have revolutionized how metal surfaces are treated, making them a preferred choice for professionals and hobbyists alike.
Understanding Flap Discs
Flap discs are made of multiple layers of abrasive material, usually attached to a central hub. These layers, or “flaps,” provide a larger surface area for grinding and polishing, allowing for quicker material removal and a finer finish compared to traditional grinding wheels. As the disc wears down, new layers of abrasives are exposed, which ensures a consistent cutting action throughout its lifespan. This design not only enhances performance but also prolongs the life of the disc.
Versatility in Applications
One of the standout features of flap discs is their versatility. They can be used on various materials, including steel, aluminum, and other metals, as well as on wood and plastics. Different types of flap discs are designed for specific applications, such as grinding, blending, or polishing. For example, a coarse grit flap disc is ideal for heavy material removal and surface preparation, while a finer grit disc is perfect for polishing and achieving a smooth finish.
In industries such as automotive, aerospace, and manufacturing, flap discs play a critical role. They are used for tasks such as deburring, edge grinding, and surface finishing. The ability to transition between grinding and polishing with a single tool not only saves time but also reduces the need for multiple tools, which can streamline workflows in busy environments.
Advantages Over Traditional Grinding Methods
grinding and polishing flap disc
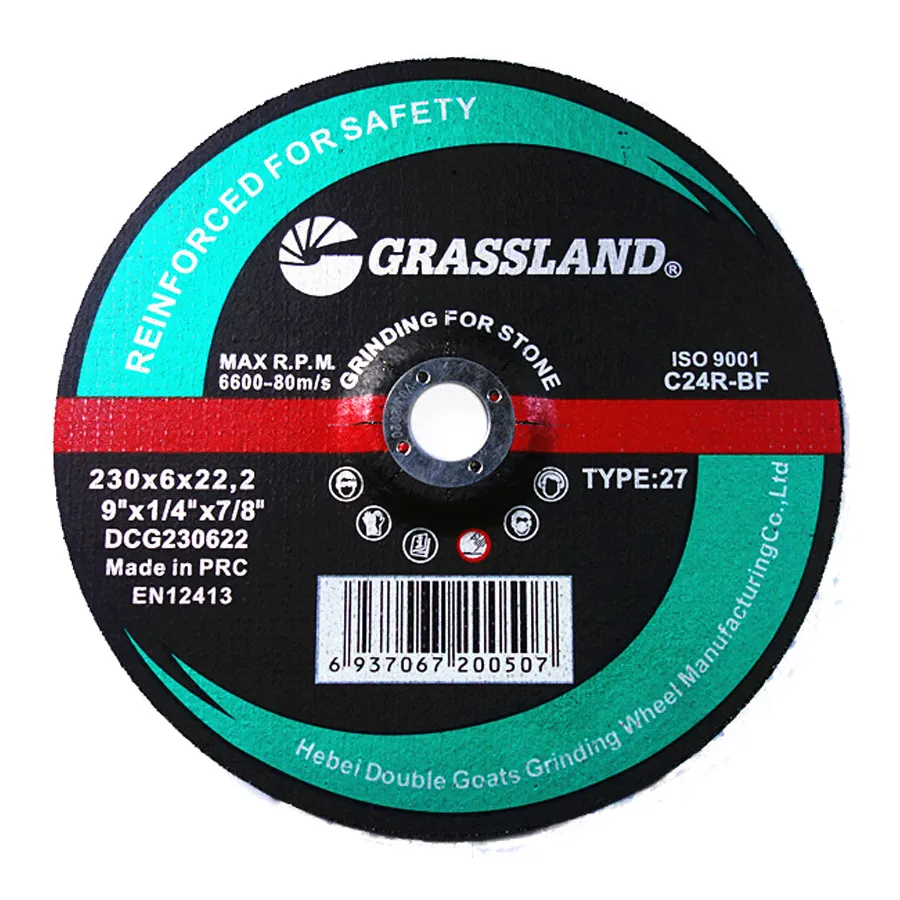
When compared to traditional grinding wheels, flap discs offer several advantages. They produce less heat and have reduced risk of warping the materials being worked on. This is particularly important in applications requiring precision, as excessive heat can lead to structural changes in metals. Furthermore, flap discs provide a smoother finish, which is essential in industries where aesthetics and surface quality are critical.
Another significant advantage is the operator control they provide. Flap discs allow for better maneuverability and more gentle pressure application, helping to reduce operator fatigue. The lightweight nature of flap discs makes them easier to handle, contributing to improved safety and efficiency in the workplace.
Choosing the Right Flap Disc
Selecting the right flap disc for a specific task involves understanding the material being worked on, the type of finishing required, and the machine being used. Flap discs come in various sizes, grades, and materials. For instance, zirconia flap discs are known for their durability and aggressive cutting action, making them suitable for heavy-duty applications. Conversely, aluminum oxide discs are often used for lighter tasks, owing to their fine grinding capabilities.
A key consideration when choosing a flap disc is the grit size, which ranges from coarse to very fine. Coarse grit discs (typically lower numbers) are best for rapid material removal, while fine grit discs (higher numbers) are ideal for final polishing and finishing tasks. The choice of disc also affects the surface finish, so it’s important to match the disc to the desired outcome.
Conclusion
In summary, grinding and polishing flap discs have become indispensable tools in a variety of industries. Their versatility, efficiency, and superior performance make them a go-to choice for metalworking professionals. As technology continues to advance, it is likely that flap discs will evolve further, offering even more capabilities and enhancements. Understanding how to use these tools effectively can lead to better quality finishes, increased productivity, and more streamlined operations in metalworking applications. Whether you are a seasoned professional or a DIY enthusiast, investing in the right flap discs is crucial for achieving outstanding results.
Post time:Dec - 13 - 2024